Curing Our Lack of Knowledge on Polymer Concrete
Ever wondered about the fabric of the structures that surround us everyday?
Have you heard about polymer concrete and its increasing popularity in the construction industry?
Wondered if it’s going to shift the future of construction as we know it?
Well, say goodbye to being in the dark because we are about to explore and understand polymer concrete. Dive in and learn more about what it is, why it’s becoming the go-to material for many contemporary constructions, and how it compares to traditional concrete options.
So strap in, and let’s learn about the world of polymer concrete.
Table of Contents
Prefer to watch instead of read? Click below.
Understanding Polymer Concrete
What is Polymer Concrete?
When it comes to construction materials, polymer concrete is a unique blend that offers superior performance characteristics compared to traditional concrete. This material is a type of concrete that uses polymers (resins) as a binding agent in place of the more commonly used cement.
Key Characteristics of Polymer Concrete:
- Higher tensile strength
- Improved durability
- Increased resistance to chemicals
- Enhanced flexibility
- Reduced permeability
Applications of Polymer Concrete:
Polymer concrete finds applications in various construction projects where its unique properties are beneficial. Some common uses include:
- Bridge decks
- Industrial flooring
- Chemical containment structures
- Wastewater treatment plants
- Highway repair and maintenance
With its versatility and durability, polymer concrete has become a popular choice for demanding construction applications that require resilience and longevity.
How To Make Polymer Concrete
Components of Polymer Concrete:
- Aggregate: The choice of aggregate can vary based on the desired properties and application of the final product. Fine and coarse aggregates are commonly used to provide strength and bulk to the material.
- Polymer Resin: The resin acts as the binder for the aggregates, replacing cement and water used in traditional concrete. Epoxy, polyester, and acrylic are among the most commonly used resins.
- Fillers and Additives: To enhance certain properties like strength, durability, and workability, various fillers and additives can be incorporated into the mix.
Making Polymer Concrete: Step-by-Step
Step 1: Selecting the Right Materials
Begin by choosing the appropriate type of aggregate, polymer resin, and any additional fillers or additives needed for your specific application. The choice of materials will significantly influence the properties of the final product.
Step 2: Preparing the Aggregate
The aggregate should be clean and dry to ensure proper bonding with the resin. It’s typically pre-mixed to ensure an even distribution of different sizes.
Step 3: Mixing the Resin
Prepare the polymer resin as per the manufacturer’s instructions. This often involves mixing two components together to initiate the chemical reaction that sets the resin.
Step 4: Combining the Aggregate and Resin
Gradually add the prepared aggregate to the resin, ensuring thorough mixing to coat the aggregate particles evenly with the resin. This step might require mechanical mixers for larger batches to achieve a uniform mixture.
Step 5: Pouring and Curing
Once mixed, the polymer concrete should be poured into the prepared molds or forms immediately due to its rapid curing time. The material then needs to be left to cure, which can take from a few hours to a day, depending on the resin system used and ambient conditions.
Step 6: Demolding and Finishing
After curing, the polymer concrete can be demolded. It may require additional finishing, such as sanding or polishing, depending on the intended use.
Applications and Considerations
Polymer concrete’s versatility and superior properties make it suitable for a wide range of applications, including drainage channels, industrial flooring, repair works, and even decorative elements.
However, it’s important to consider the cost implications, as polymer resins can be more expensive than traditional cement.
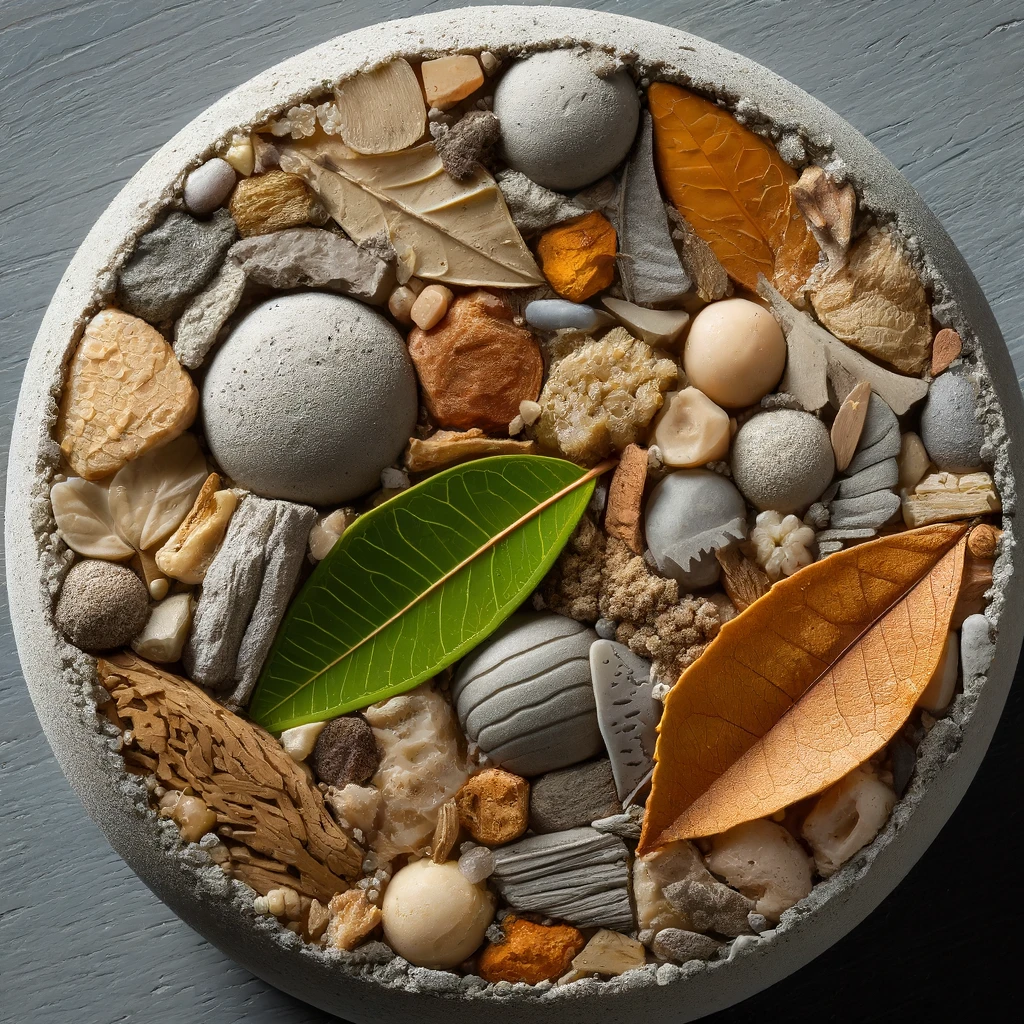
Getting the Bigger Picture Of Polymer Concrete
The Stunning Benefits of Polymer Concrete
Polymer concrete’s properties not only make it a highly attractive choice in the construction world, but it brings several enormous benefits too.
Let’s shed some more light on these advantages, shall we?
Reduced Curing Time:
Because of its unique chemical composition, polymer concrete offers faster curing times than traditional concrete. This increased efficiency leads to expedited project timelines, ensuring on-time project completion and lower labor costs.
Superior Aesthetic Properties:
The use of polymers in the concrete composition better preserves color and texture, enhancing the overall aesthetic appeal of the finished structure. This aspect is particularly desirable for architectural projects requiring visually striking results.
Unparalleled Environmental Resistance:
Polymer concrete’s elevated resistance to corrosive environments, including salts, acids, alkalis, and solvents, further extends its life. It is an ideal material for use in harsh environments, widely utilized in coastal defense and railroad applications.
Innovative Implementation of Polymer-Concrete Composites:
Progressive strides in the construction industry have led to the innovative implementation of polymer concrete composites. Its excellent variability in design, coupled with its impressive strength-to-weight ratio, fosters its use in thin-wall structures or intricate designs that demand high tensile strength and improved flexibility.
Cost Savings with Polymer Concrete:
Considering polymer concrete’s properties, its initial cost may be higher than conventional concrete.
However, its long-term benefits manifest in the form of reduced maintenance costs, long lifespan, and superior performance, thus offering excellent value for money.
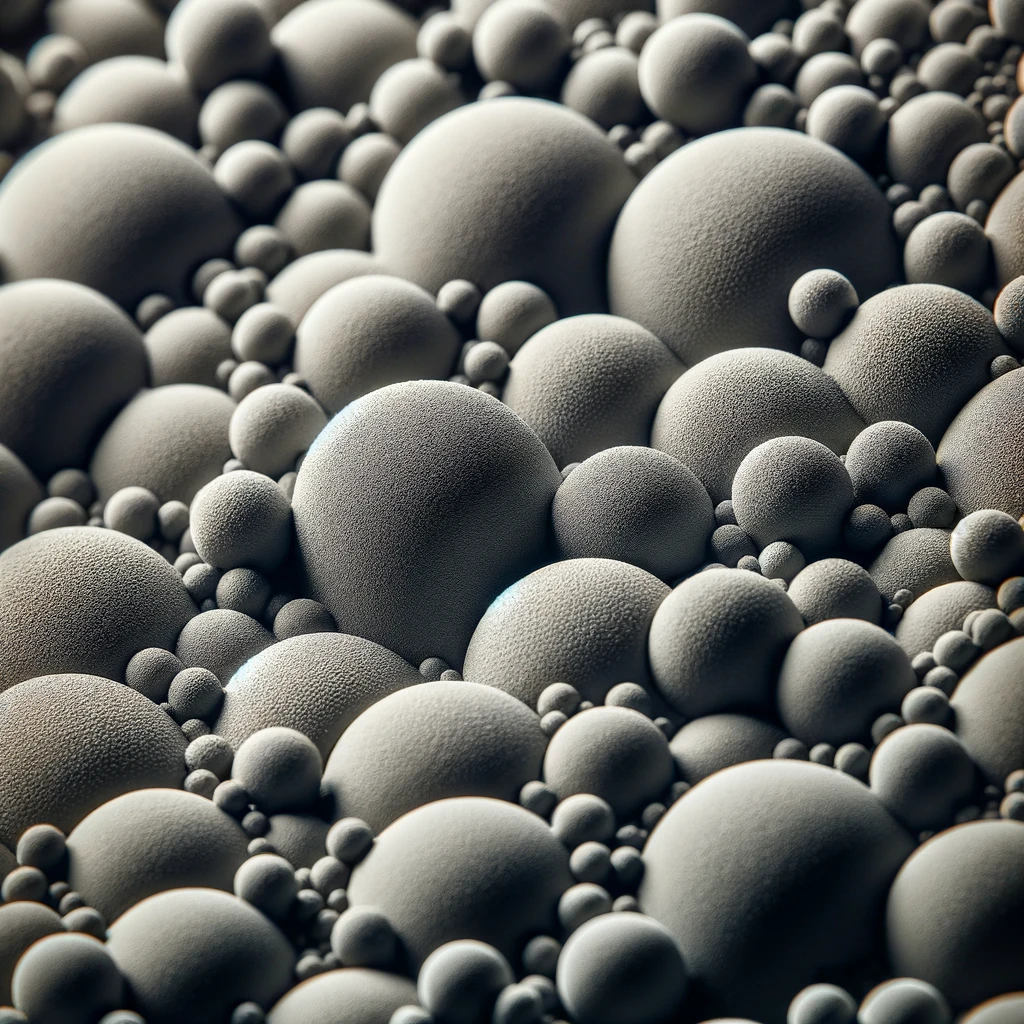
Polymer Concrete’s Role in Precast Concrete
Understanding Precast Concrete
Precast concrete refers to a construction product prepared, cast and cured off-site, usually in a factory that’s specifically designed for the production of precast elements.
Precast concrete typically uses standard cement as a binder rather than polymers, but polymer concrete can be used for precast purposes, too.
Key Features of Precast Concrete:
- Exceptional structural stability
- Greater affordability
- Resistance to weathering and heavy load
- Availability in a variety of shapes and sizes
- Reduced on-site labour
Applications of Precast Concrete:
Precast concrete carries a wide range of applications in the larger construction industry. They are often favoured for:
- Pipes and manholes
- Building walls and facades
- Bridge girders
- Staircases and flooring
- Other structural applications
With its ability for mass production and quick installation, precast concrete plays a fundamental role in large-scale projects and structures with repetitive designs.
Why Does Precast Concrete Hold Such a Significant Place in Construction?
Economical and Efficient:
One significant advantage of precast concrete is its cost-effectiveness. Its mass production in a factory-controlled environment allows for economies of scale and lessens the risk of project overruns. Plus, precast concrete elements are made and cured in advance, significantly reducing the construction timeline.
Quality Control:
The off-site production of precast concrete allows for stringent quality control measures than on-site cast concrete. Factory conditions can be controlled and monitored more closely, leading to a higher-quality product with fewer defects and less wastage.
Environmental Friendliness:
Precast concrete is an environmentally friendly solution as it utilises locally sourced materials, reduces wastage, and minimises noise and air pollution at the construction site.
Furthermore, the durability of precast concrete means that its negative impacts on the environment are spread over an extended lifespan, making it an eco-friendly option in the long run.
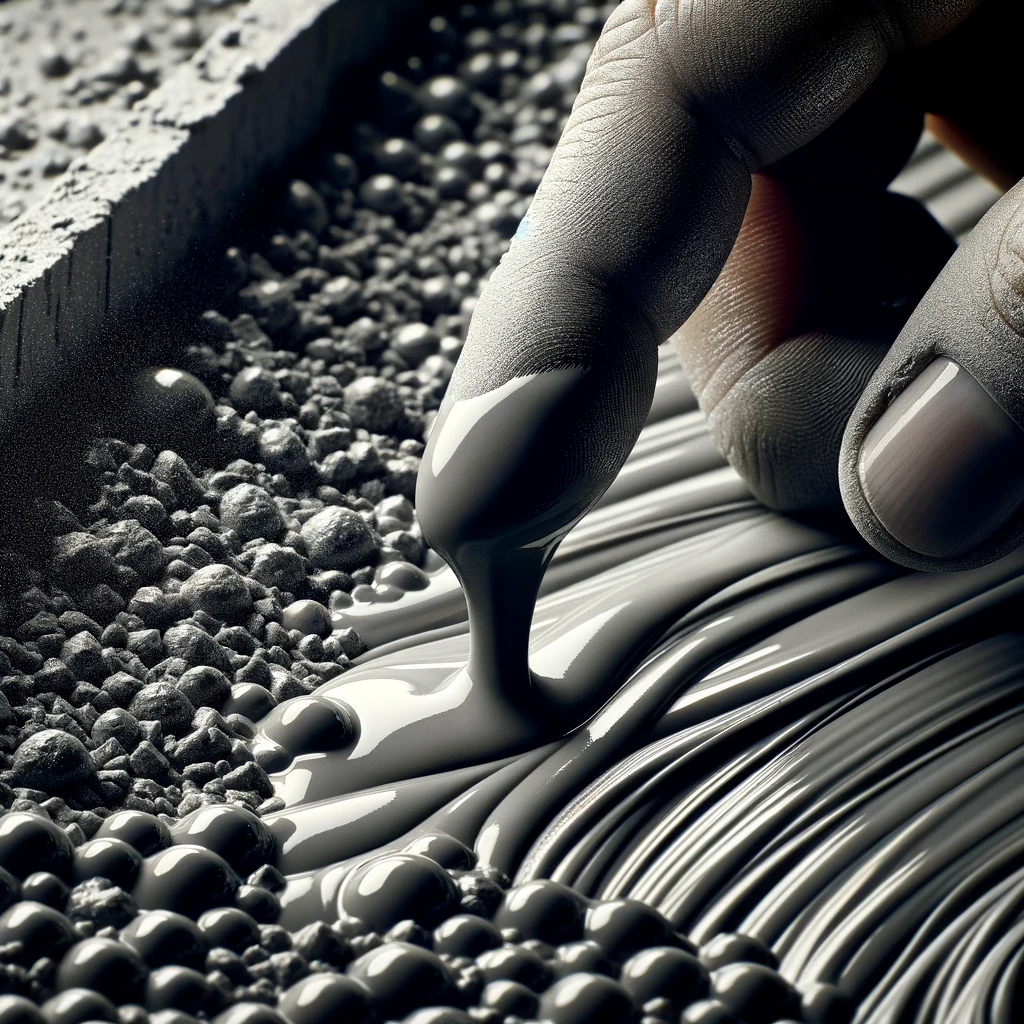
When Should I Use Polymer Concrete or Cement Concrete In Precast?
Polymer Concrete in Precast Applications
Polymer concrete, due to its unique properties, is particularly suited for certain precast applications:
1. When High Chemical Resistance is Required:
If your project is exposed to aggressive chemicals, acids, or corrosive environments, polymer concrete is a superior choice due to its exceptional chemical resistance.
2. In Need of Rapid Curing and Fast Turnaround:
Polymer concrete cures significantly faster than cement concrete. For projects with tight deadlines or where early strength is crucial, polymer concrete allows for quicker demolding and installation.
3. For Precision and High Detail Applications:
Due to its low viscosity before curing, polymer concrete can fill intricate molds and achieve precise details and shapes, making it ideal for specialized precast elements and decorative components.
4. Where Durability and Low Maintenance are Paramount:
Polymer concrete’s low permeability and absence of micro-cracks contribute to its durability and resistance to freeze-thaw cycles, making it a suitable choice for harsh environments.
5. For Lightweight Construction Needs:
Depending on the aggregate and resin used, polymer concrete can be lighter than traditional concrete, which may be beneficial for reducing transport and installation costs, especially in applications where weight is a concern.
Cement Concrete in Precast Applications
Cement concrete, on the other hand, is often preferred for a variety of reasons:
1. Cost-Effective Solutions:
For projects where budget constraints are a significant factor, cement concrete is generally more economical than polymer concrete, both in terms of raw materials and the production process.
2. Large Scale and Structural Applications:
Due to its cost-effectiveness and comprehensive strength, cement concrete is more suitable for large-scale structural components, including beams, columns, and slabs in buildings and infrastructure.
3. When Thermal Mass is Desired:
Cement concrete’s mass helps stabilize temperature fluctuations within buildings, making it a good choice for applications where thermal mass can contribute to energy efficiency.
4. Availability of Materials:
In regions where the procurement of polymer resins is challenging or expensive, traditional cement concrete might be the more practical option due to the readily available nature of its constituents.
5. Sustainability Considerations:
While both materials have environmental impacts, the cement industry is actively working on reducing its carbon footprint through the use of supplementary cementitious materials (SCMs) and other innovations. If sustainability is a high priority, consider the latest advancements in eco-friendly cement concrete options.
Comparing the Two: Cement Vs. Polymer Concrete
While both traditional cement precast concrete and polymer concrete serve different purposes and hold their unique advantages, it’s their underlying differences that determine their applications. But is one inherently better than the other?
Cement Concrete | Polymer Concrete | |
---|---|---|
Cost | Lower initial cost | Higher initial cost but long-term savings |
Durability | Subject to weathering | Highly resistant to harsh environments |
Flexibility | Lower | Higher |
Potential Applications | Large-scale, repetitive designs | Demanding construction applications |
In conclusion, selecting between cement and polymer concrete depends essentially on the project’s needs. From cost considerations to design flexibility and durability, it’s crucial to weigh all factors before making an informed decision.
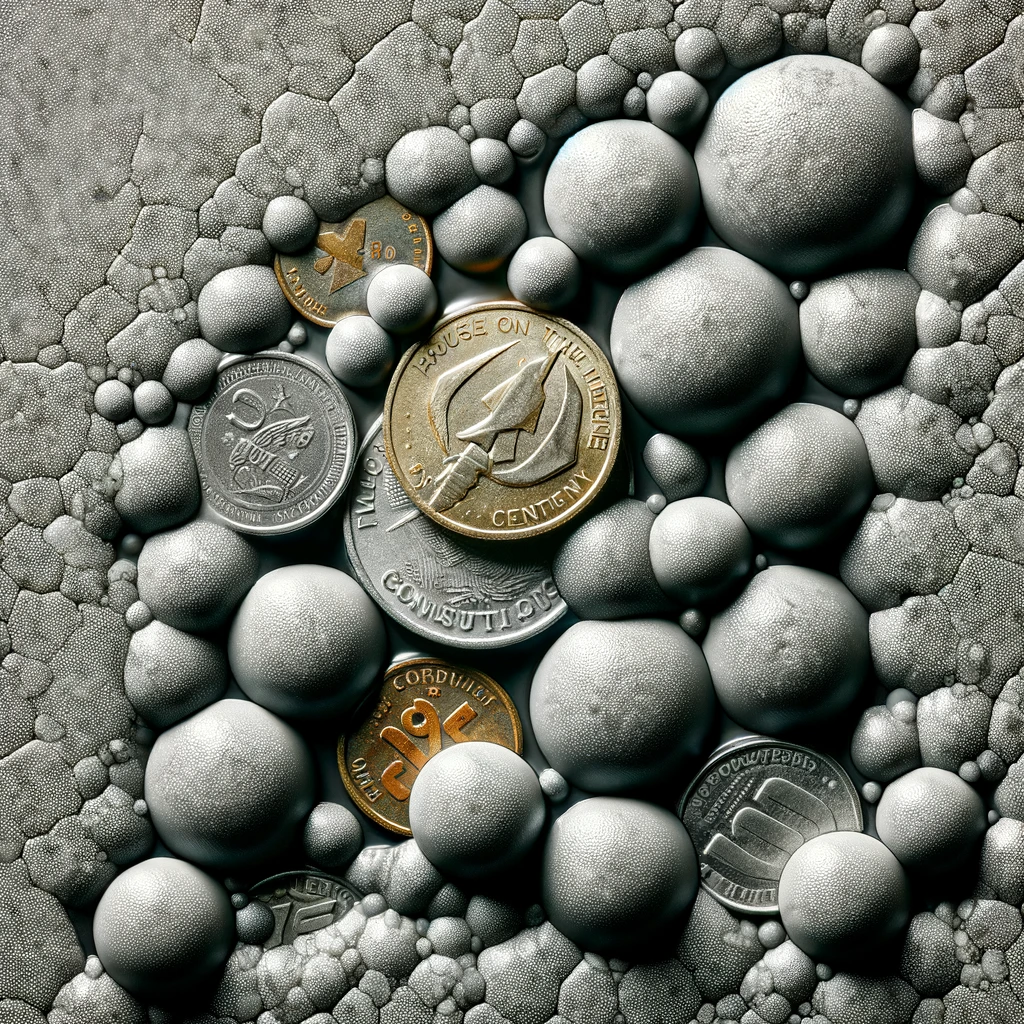
Untangling the Price Tag: Is Polymer Concrete Expensive?
Delving into the Cost of Polymer Concrete
The monetary value associated with polymer concrete lies not so much in the upfront cost, but in its long-term value and return on investment. Let’s ponder on this, shall we?
Upfront Costs:
True, the initial investment in polymer concrete jams its price higher than conventional concrete. This bump in cost can be attributed to the use of polymers, which are pricier than the standard cement used as a binder in traditional concrete.
Maintenance and Repair Costs:
However, when it comes to maintenance and repair costs, polymer concrete shines. Its superior durability, high resistance to chemicals and environmental conditions mean fewer repairs are needed over the course of its life. These features translate to added savings in the long run.
Longevity and Durability:
Moreover, the enhanced lifespan of polymer concrete delivers cost efficiency over time. With a longer lifespan than traditional concrete, replacement costs are deferred, offering extra value for your buck.
Making the Decision: Is the Investment Worth It?
While the upfront cost of polymer concrete is undoubtedly higher, the long-term benefits culminate in cost savings that can outweigh initial investments.
Its longevity, minimal maintenance requirements, and superior performance characteristics result in an overall higher return on investment.
The question is, can you handle the upfront cost for long-term gain?
Solidifying Our Knowledge Of Polymer Concrete
Polymer concrete offers a groundbreaking solution to construction needs, taking the performance of traditional concrete one step further.
By incorporating polymers as a binding agent, this material presents a range of advantages that elevate its strength, durability, and resilience.
From its higher tensile strength to enhanced flexibility, polymer concrete showcases a set of key characteristics that make it a sought-after choice for a variety of construction projects.
Its increased resistance to chemicals and reduced permeability further contribute to its suitability for demanding applications.
With widespread use in projects like bridge decks, industrial flooring, and wastewater treatment plants, polymer concrete continues to prove its value in the construction industry.
Choosing polymer over traditional concrete is not just about innovation but also about ensuring long-lasting results that withstand the test of time and environmental challenges.