An Introduction to Understanding Voltage Withstand Tests
Ever wondered how electrical equipment is tested for safety and insulation strength?
They undergo an important process known as the Voltage Withstand Test.
This test ensures that electrical devices are safe to operate at their rated voltages and can stand up to potential overvoltage conditions without failing.
The Voltage Withstand Test, also known as a dielectric resistance test, is an industry-standard procedure. Its importance stems from its capability to prevent electrical failures that could cause severe accidents – including fires or electrocution.
How does this test work, you ask?
It applies high voltage to the electrical device and measures its ability to withstand this voltage without breaking down.
Sounds complicated? Don’t worry!
We’ll explore it step-by-step, discussing everything from the basics of the test, its importance, and the practical process steps, to understanding the relevant test voltage levels and factors affecting these levels.
Table of Contents
Understanding the Voltage Withstand Test Method in Construction
Basics of the Voltage Withstand Test
The voltage withstand test, also known as the dielectric resistance test, is an essential process in construction to validate the insulation strength of electrical components and systems. This test ensures that electrical devices can safely operate at their rated voltages and maintain their integrity under overvoltage conditions.
Why It’s Important
This test is essential for several reasons:
- Safety: Prevents electrical failures that can cause fires or electrocution.
- Quality Assurance: Ensures that equipment meets safety and performance standards.
- Compliance: Adheres to industry regulations and standards.
Testing Procedures
The process involves applying a high voltage to the electrical device and measuring its ability to withstand this voltage without breaking down.
Step-by-Step Process
1. Preparation: Make sure the equipment is turned off and isolated from the power source.
2. Application: Connect the voltage source to the device.
3. Voltage Application: Gradually apply the test voltage, often higher than the operational voltage, for a specific time period.
4. Monitoring: Observe the device for any signs of insulation breakdown.
Table: Common Voltage Withstand Test Levels
Type of Equipment | Typical Test Voltage (AC) | Test Duration |
---|---|---|
Low Voltage Cables | 1 kV – 5 kV | 1 minute |
Medium Voltage Transformers | 15 kV – 35 kV | 1 minute |
High Voltage Switchgear | 70 kV – 150 kV | 1 minute |
Best Practices
- Calibration: Ensure the testing equipment is calibrated accurately.
- Documentation: Record all test results meticulously for future reference.
- Safety Gear: Wear appropriate PPE (Personal Protective Equipment) during testing.
For more detailed standards and guidelines on voltage withstand testing, you can refer to the OSHA website.
Deciding the Appropriate Voltage Level in Withstand Testing
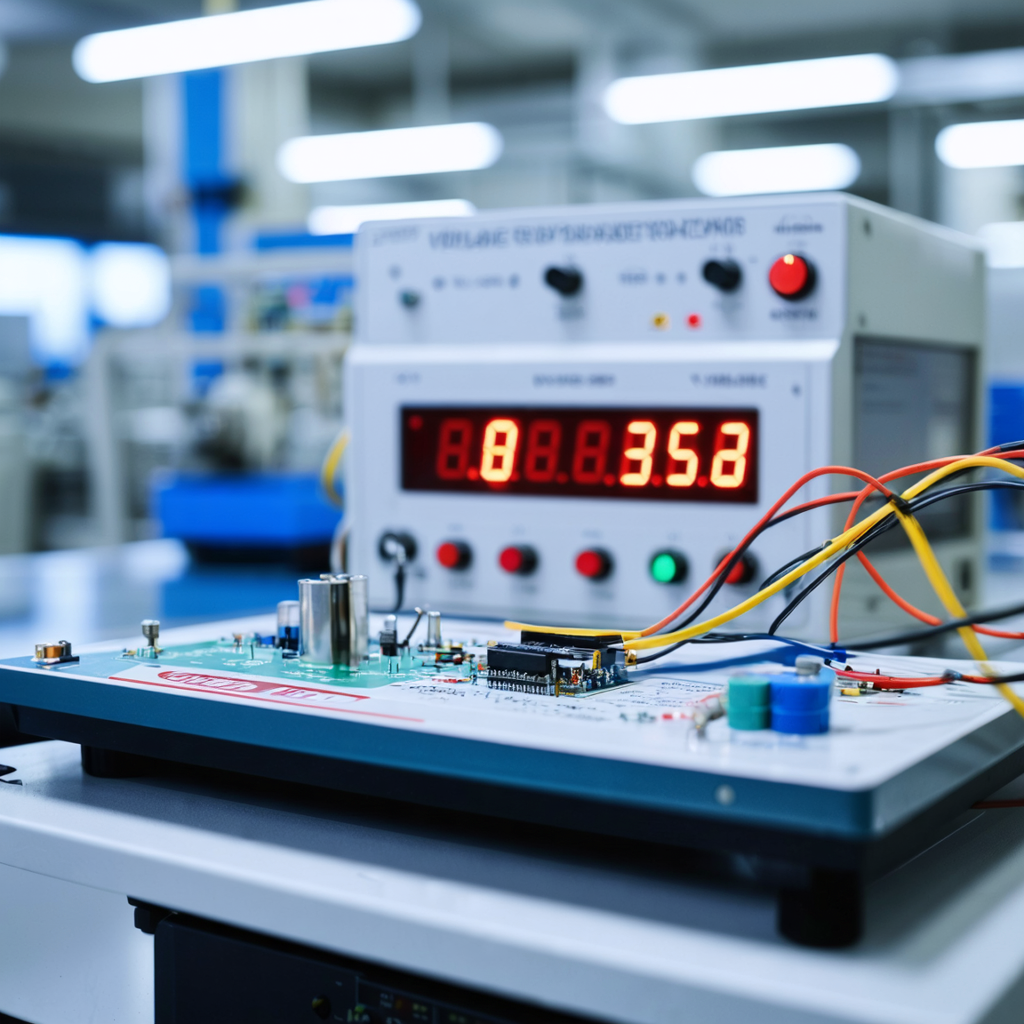
Understanding the ‘Withstand Voltage’
In the context of electric circuits and devices, the term ‘withstand voltage’ broadly means the maximum voltage that a device can withstand without undergoing breakdown. As the name suggests, this voltage is an indication of the level of stress or voltage a device can endure before its insulating properties succumb to the voltage applied.
Factors Influencing the Withstand Voltage Level
In the case of electrical devices, the withstand voltage level is an inherent property that depends on several factors like:
- Material Insulation: The type, thickness, and quality of the insulation material substantially influence the withstand voltage.
- Manufacturing Techniques: The construction and manufacturing techniques impact the insulation’s ability to resist high voltage.
- Environmental Conditions: Factors such as temperature, humidity, and altitude can also affect the withstand voltage.
Setting the Test Voltage Level in Withstand Testing
Establishing the appropriate voltage to be used in a withstand test involves understanding the device’s nominal operating voltage and adding a certain percentage to create a safety margin. The additional percentage is determined by several factors such as the application environment, safety regulations, and industry-specific standards.
According to IEEE and other standards, for most equipment, the test voltage should generally be around one and a half to two times the device’s nominal voltage. However, as the equipment voltage rating increases, the test voltage multiplier may decrease to ensure equipment safety during testing.
Table: Estimated Test Voltage for Different Voltage Ratings
Equipment Voltage Rating | Estimated Test Voltage |
---|---|
Less than 1 kV | 1.5 to 2 times the voltage rating |
Between 1 kV and 35 kV | 1.25 to 1.5 times the voltage rating |
More than 35 kV | 1.1 to 1.25 times the voltage rating |
Failing and Passing a Withstand Test
For a device to accurately pass a withstand test, it must not show any signs of insulation failure during the specified test period. This could potentially manifest as visible discharges, excessive leakage current, or in the worst-case scenario, a catastrophic breakdown.
Moreover, any noticeable deterioration, such as deformation, discoloration, or unusual smells, can also be considered signs of a potential failure, even if the device continues to operate under normal conditions. It is recommended to refer to the guidelines and best practices mentioned by IEEE for precise device-specific testing protocols.
Voltage Withstand Rating in Electrical Equipment
Understanding Voltage Withstand Rating
Voltage withstand rating refers to the maximum voltage level that an electrical device or component can endure without experiencing an insulation breakdown. It is a key parameter when designing and testing electrical equipment to ensure reliability and safety. Simply put, if a device has a high voltage withstand rating, it can handle higher voltages without failing.
Importance of Voltage Withstand Rating
The voltage withstand rating is vital for several reasons:
- Safety: Protects against electrical hazards, reducing the risk of fires, shocks, and other electrical failures.
- Equipment Longevity: Ensures that components can operate safely under transient overvoltage conditions, thereby increasing their lifespan.
- Regulatory Compliance: Adheres to industry and governmental standards, ensuring legal compliance and insurance requirements.
Affecting Factors in Determining the Voltage Withstand Rating
Several factors influence the voltage withstand rating of electrical devices:
- Insulation Material Quality: Different materials have varying inherent dielectric strengths. High-quality insulation materials typically offer better withstand capabilities.
- Operational Environment: Conditions such as temperature, humidity, and atmospheric pressure can affect the insulating properties of materials.
- Design and Construction: The structural design, including thickness and layering of insulating materials, play a crucial role in determining the rating.
Standards for Voltage Withstand Rating
Globally, various standards have been set to define acceptable voltage withstand ratings for different types of electrical equipment. These standards are essential for ensuring consistency and safety across the industry.
Standard | Purpose | Governing Body |
---|---|---|
IEC 61180 | High-voltage test techniques for low voltage equipment | International Electrotechnical Commission (IEC) |
IEEE 43 | Recommended practice for testing insulation resistance | Institute of Electrical and Electronics Engineers (IEEE) |
UL 1446 | Systems of insulating materials – General | Underwriters Laboratories (UL) |
Practical Testing Considerations
When conducting voltage withstand tests, several practical considerations should be kept in mind to ensure the test’s accuracy and effectiveness:
- Test Environment: Conduct tests in controlled environments to mitigate external factors like humidity and temperature that can affect results.
- Test Equipment Calibration: Regularly calibrate the test equipment to ensure precise voltage application and measurement.
- Interpretation of Results: Understand the acceptable levels of leakage current or other minor irregularities that do not necessarily indicate insulation failure.
For more information on guidelines and recommendations, refer to the detailed standards provided by NIST (National Institute of Standards and Technology).
Main Purpose of High Voltage Withstand Test (Hipot Test)
Fundamentals of Hipot Testing
The high voltage withstand test, commonly known as the hipot (high potential) test, is used to ensure the insulation quality of electrical devices by applying a high voltage to check for any breakdowns. This test is paramount in validating that electrical devices can safely operate without insulation failure under normal and overvoltage conditions.
Significance of Hipot Testing
Hipot testing is essential for multiple reasons beyond just safety and quality:
- Detection of Manufacturing Defects: Helps identify insulation flaws resulting from production processes.
- Predictive Maintenance: Provides insights into the aging and wear of insulation, allowing for preventative actions.
- Peace of Mind: Assures manufacturers and consumers that the product has been rigorously tested for electrical safety.
Types of Hipot Tests
Three primary types of hipot tests are generally conducted, each serving a different purpose:
- Dielectric Breakdown Test: Determines the failure voltage of a device by increasing the voltage until the insulation fails. This test typically destroys the sample.
- Dielectric Withstand Test: Applies a high voltage below the breakdown level to ensure the device can operate under this stress for a specified duration. This test is nondestructive and more common in quality control.
- Insulation Resistance Test: Measures the resistance of the insulation by applying a steady voltage. Lower resistance indicates potential insulation problems.
Performing a Hipot Test
To conduct a hipot test effectively, follow these detailed steps:
1. Preparation:
– Confirm that the device is disconnected from all power sources and other components.
– Gather necessary testing equipment, ensuring it is calibrated and functional.
2. Connection:
– Attach the high voltage lead from the test equipment to the conductor being tested.
– Ground the other side of the device to prevent floating potentials.
3. Voltage Application:
– Initiate the Voltage increase to the pre-determined test level carefully.
– Maintain the voltage level for the required test duration, monitoring for leakage current or other abnormalities.
4. Conclusion:
– Gradually reduce the voltage to zero.
– Disconnect the testing leads safely and observe the test results, focusing on any leakage current readings or breakdown signs.
Table: Voltage Withstand Test Levels for Different Equipment
Equipment Type | Test Voltage (AC) | Test Duration |
---|---|---|
Consumer Electronics | 0.5 kV – 2 kV | 1 minute |
Industrial Motors | 1 kV – 30 kV | 1 minute |
Power Inverters | 2 kV – 10 kV | 1 minute |
Practical Considerations in Hipot Testing
Here are several best practices to ensure the effectiveness and safety of hipot testing:
- Prepare the Test Area: Conduct tests in areas free from unnecessary personnel and distractions to centralize focus on safety and accuracy.
- Proper Grounding: Ensure that all test equipment is adequately grounded to prevent inaccurate results or potentially hazardous situations.
- Leakage Current Levels: Define acceptable leakage current levels based on device specifications and industry standards to interpret the results correctly.
- Consistent Documentation: Keep detailed records of every test, noting any anomalies or failures to track issues systematically.
Comprehensive guidelines for these practices can be found on the OSHA website, which offers critical safety and testing standards for electrical equipment.
Concluding Thoughts on Voltage Withstand Testing
In conclusion, the voltage withstand test is a fundamental part of assuring the safety and reliability of electrical equipment.
It employs a process of applying high voltage to determine the maximum voltage that devices can endure before an insulation breakdown occurs. This evaluation is vital in preventing electrical hazards and ensuring compliance with industrial and regulatory standards.
Multiple factors influence the permissible withstand voltage, such as the quality of insulation materials, environmental conditions, and manufacturing techniques.
By understanding these influencing factors and effectively conducting the voltage withstand test, we ensure the best quality of our electrical devices and the safety of everyone who interacts with them.
Frequently Asked Questions – FAQs
What is the voltage withstand test?
A voltage withstand test, also known as a dielectric resistance test, testifies to the insulating strength of electrical components and systems. It is designed to ensure that these devices can operate safely at their rated voltages and maintain their integrity under overvoltage conditions.
Why is voltage withstand testing important?
This testing method is necessary for ensuring safety by preventing electrical failures including fires and electrocution. Furthermore, it provides quality assurance, confirming that equipment complies with safety and performance standards, and verifies compliance with industry regulations and standards.
How is a voltage withstand test performed?
The process involves applying a high voltage to the electrical device and then measuring its ability to withstand this voltage without breaking down. The device is prepared, the voltage is applied and gradually increased, and then observation is carried out for any signs of insulation breakdown.
What factors influence the withstand voltage level?
The withstand voltage level is influenced by several factors including the quality and thickness of the insulation material, manufacturing techniques utilized, and environmental conditions like temperature, humidity, and altitude.
What are the standards for voltage withstand rating?
Standards such as the IEC 61180, IEEE 43, UL 1446, among others, have been set globally to define acceptable voltage withstand ratings for various types of electrical equipment. These standards are instrumental in ensuring consistency and safety across the industry.