Are Transformers as Solid as They Seem?
Did you ever pause to consider the complexity of transformers?
They are key to delivering power safely to our homes and businesses, yet many of us are unaware of the roles insulation plays in their \ operation.
The ever-changing landscape of transformer insulation materials echoes Albert Einstein’s wise words – “The measure of intelligence is the ability to change.” Like the advent of the digital era, the field of insulation has also seen an era of advancement.
New materials, such as polymer films and aramid paper, are slowly finding their niche alongside traditional cellulose paper.
So, let’s turn the dial up on our curiosity and dig deeper into the world of transformer insulation.
- What exactly does it do?
- What materials are used?
- How does it affect performance?
The answers may surprise you.
Table of Contents
Transformer Insulation: An Essential Component Explained
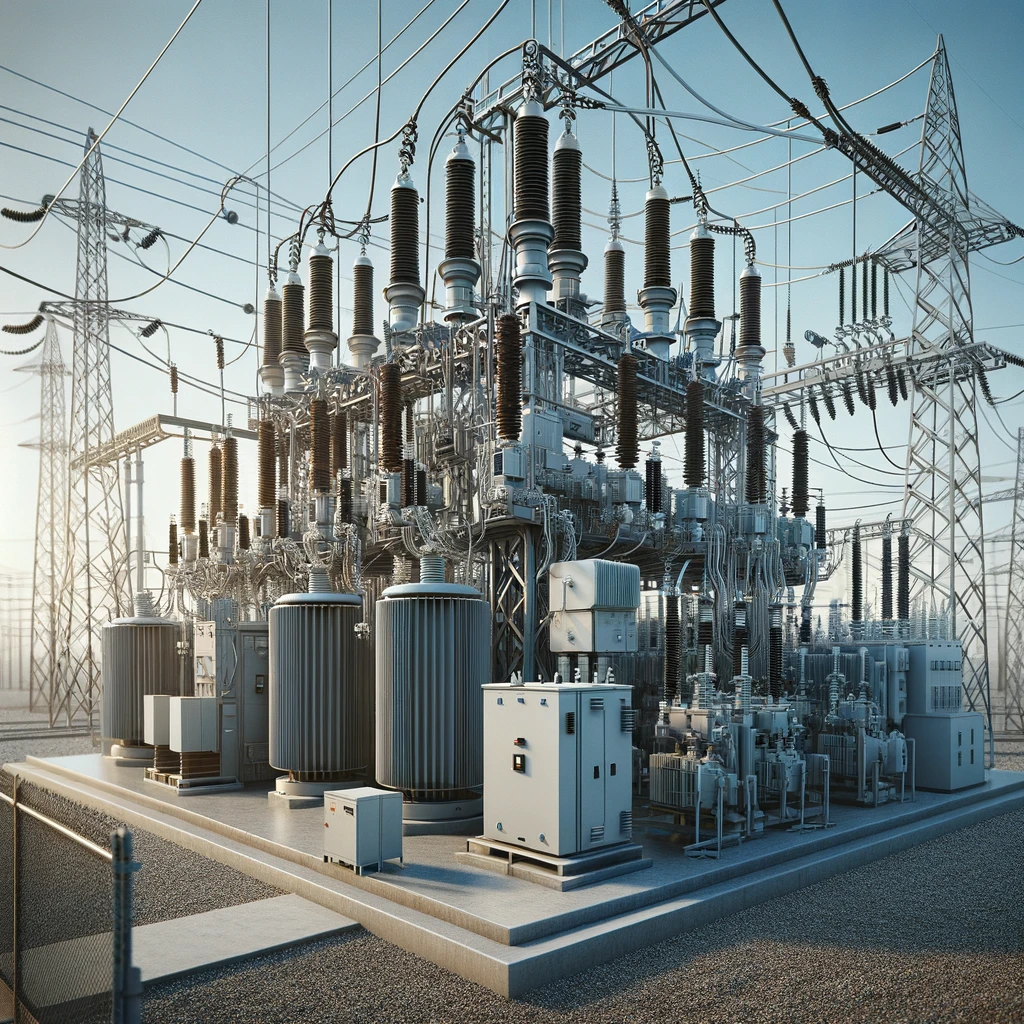
The Role of Insulation in Transformers
Insulation in transformers is an indispensable element that serves two primary roles: electrical insulation and mechanical support.
Electrical Insulation
The first, and most common, role of insulation is to isolate the internal elements of the transformer from each other and from the transformer casing. By doing this, it safeguards the flow of electric currents by preventing electrical discharges, breakdowns, and leaks.
Mechanical Support
The secondary function of transformer insulation is providing mechanical reinforcement to the windings and preventing movement that could potentially lead to abrasion or mechanical failure.
The Transformer’s Major Insulation
The major insulation of a transformer designates the insulation between windings, and between windings and grounded parts. These insulations can be in the form of solid, liquid, or gas.
Solid Insulation
The predominant type of solid insulation is Cellulosic paper and pressboards which are impregnated with mineral oil. These are typically used for the insulated conductors, interlayer insulation, spacer rings, and so forth.
Liquid Insulation
Mineral Oil sets the standard for liquid insulation in a transformer. It suspends any solid insulation materials like the cellulosic paper and also cools down the transformer by dissipating heat away from the windings.
Gas Insulation
Sometimes, a gaseous type of insulating material, usually air, nitrogen, or sulfur hexafluoride, is used especially in high voltage transformers, offering the benefit of being explosion and fire proof.
Factors That Affect Insulation Performance
A multitude of factors affect the performance of a transformer’s insulation system:
- Transformer Design: With well-designed insulation, electrical stress will be evenly distributed, preventing premature breakdown.
- Quality of Insulation Material: Superior quality materials improve insulation longevity and robustness.
- Ambient Conditions: Mechanical and thermal stresses caused by temperature fluctuations, moisture, and contaminants can reduce the insulation’s strength.
- Maintenance: Routine maintenance and monitoring of oil and solid insulation health helps maintain the transformer’s performance and reliability.
the Details: Major Insulation
The major insulation in a transformer is a fundamental component that ensures a functional and safe operation.
Transformer insulation is more than just a protective barrier; it’s a finely balanced system engineered to withstand both electrical and mechanical stresses while ensuring the reliability and safety of the transformer itself.
The Ramifications of Insulation Failure
The Deadly Consequence: Electrical Failure
When insulation fails in a transformer, it serves as the starting point for a rather dangerous chain reaction.
Primarily, the ability to electrically insulate the internal components becomes compromised.
This insufficiency, in turn, can lead to conductivity where there shouldn’t be any, resulting in electrical discharge or even electrical overloads – situations that almost always indicate impending disaster.
An Unwanted Chain Reaction
This compromised insulation and the resulting electrical discharge have the potential to escalate into what electrical engineers fear most – an electrical arc. This is a substantial discharge of energy that can cause catastrophic failure in the transformer, leading to a shutdown of your system, potential injuries, and even a fire or explosion.
Commanding a Rigid Form: Mechanical Failure
The second most acute consequence of insulation failure in transformers is related to mechanical support. The insulation, besides preventing electrical leaks, also provides structural rigidity to the components of the transformer. A failure in the insulating material can weaken the structural integrity of the transformer components, leading to mechanical stress and imbalance.
Rattling Skeletons
Indeed, failure in the insulating material can allow movements that cause vibrational or mechanical stress, ultimately leading to abrasion within the transformer. If left unchecked, this wear and tear can cause major component failures, further escalating the domino effect of system shutdown and damage.
Be Proactive: Identifying Early Warning Signs
Detecting insulation failure early can save costs and prevent more significant issues down the line. Some common signs of deteriorating insulation include:
- Off-specification Transformer Oil Tests: Insulation failure can be invoked by abnormalities in transformer oil, detectable by oil tests. Some visible signs might be discoloration and the presence of precipitate.
- Excessive Heat: Overheating can be a symptom of insulation failure as well, since the heat generated might not be getting discharged properly due to failure in the insulating material.
- Increase in Acoustic and Electric Discharge: If you notice an increase in the acoustic and electric discharge in your transformers, it’s often a clear indication of insulation degradation.
The Maintenance Mantra: Insulation Tests and Repairs
The cornerstone to avoiding insulation failure lies in the systematic maintenance and regular testing of transformer components. Key preventive measures include:
- Dissolved Gas Analysis (DGA): This is a diagnostic method used to measure and assess the gases dissolved in transformer oil. It can be a practical preventive tool for insulation failure.
- Maintenance of Cooling Systems: Since overheating is both a cause and a symptom of insulation failure, ensuring the cooling systems are functioning properly can contribute to insulation health.
- Periodic Insulation Resistance Measurement: Regular testing of the insulation resistance can provide an early detection system for impending insulation failure, avoiding catastrophic consequences.
An informed proactive approach helps keep your transformers functioning smoothly, ensuring you can confidently continue to rely on the unseen hero: transformer insulation.
Thickness of Transformer Insulation
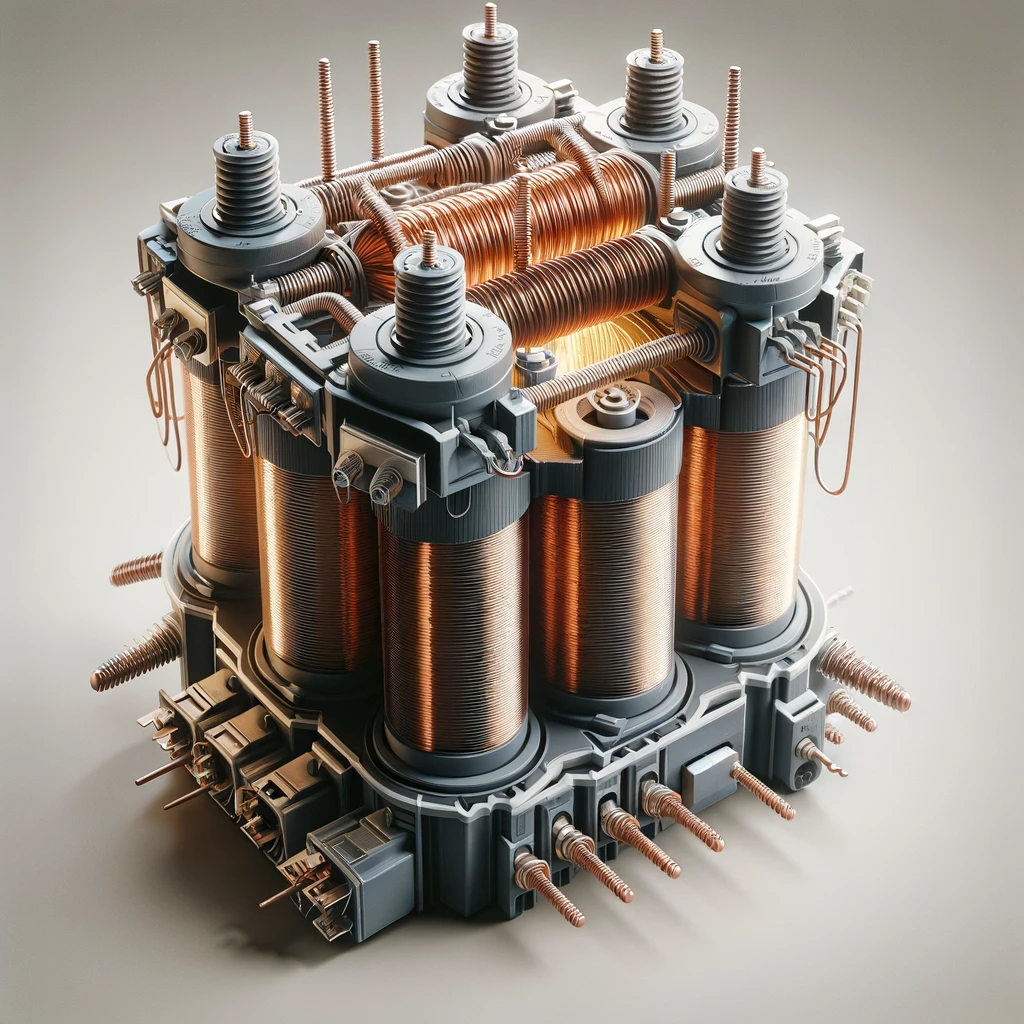
the Density: Understanding Insulation Thickness
The thickness of insulation in transformers is an often-overlooked aspect but plays a crucial role in its functioning. This thickness is not arbitrary and depends upon various factors, such as the application of the transformer, the system voltage, and the materials used for insulation.
From Thin to Thick: The Range
The insulation thickness can range from thin layers of less than a millimeter to several millimeters thick. Thicker layers of insulation may be necessary for high voltage applications or where increased mechanical strength is required.
Relation of Thickness with Voltage Levels
One of the primary factors affecting the thickness of insulation is the voltage level. Higher voltage levels require thicker insulation to prevent electrical discharges and breakdowns effectively.
Striking the Balance: Thickness vs Breakdown Voltage
Transformer engineers must strike a balance between insulation thickness and the breakdown voltage. If the insulation is too thin, the risk of electrical breakdown increases. On the other hand, if the insulation is too thick, it could increase the transformer’s size and cost without providing any additional benefits.
Thickness and Transformer Types
Different types of transformers require different insulation thicknesses. For instance, high-frequency transformers in electronic devices like televisions and laptops tend to have thinner insulation layers to accommodate their compact size.
Building Block of Size: Dry Type and Oil-Immersed Transformers
Dry type transformers typically use solid insulation, mainly polymer-based materials. These offer a good balance between insulation properties and thickness, making them ideal for smaller, low-voltage applications such as in electronic devices.
Meanwhile, oil-immersed transformers, often used in substations and power distribution systems, typically have thicker insulation. This insulation involves layers of cellulose paper, pressboard, and insulating oils which serve dual purposes of insulation and cooling.
Impact of Insulation Thickness on Transformer Performance
The thickness of transformer insulation affects its overall performance. Proper insulation thickness ensures optimum electrical insulation, mechanical strength, efficient cooling, and overall reliability.
- Electrical Insulation: Proper insulation thickness provides effective separation between the conductive parts and prevents destructive electrical discharges.
- Mechanical Strength: Insulation also adds structural rigidity to the transformer’s windings, contributing to mechanical support. Adequate thickness is crucial to achieving this.
- Cooling: Thicker insulation tends to hold more cooling oil, which aids in heat dissipation. Ensuring the right thickness provides efficient cooling without occupying unnecessary extra space.
- Reliability: Adequately thick insulation adds to the overall robustness and reliability of the transformer, thereby enabling it to operate with high efficiency over a longer lifespan.
Engineering the Ideal Thickness: The Expert’s Role
The task of determining the adequate thickness of a transformer’s insulation is up to the transformer’s engineer, who must account for all influencing factors and strike a balance between electrical insulation, mechanical support, cooling efficiency, and overall size and cost.
The design team needs to perform rigorous tests – ranging from electrical stresses to dielectric strength tests – to ensure that the selected insulation and its thickness meet the transformer’s operational requirements.
Hence, the transformer insulation thickness is tailored to the specifics of each transformer, making it a critical element in the overall transformer design process.
An Overview on Paper Insulation in Transformers
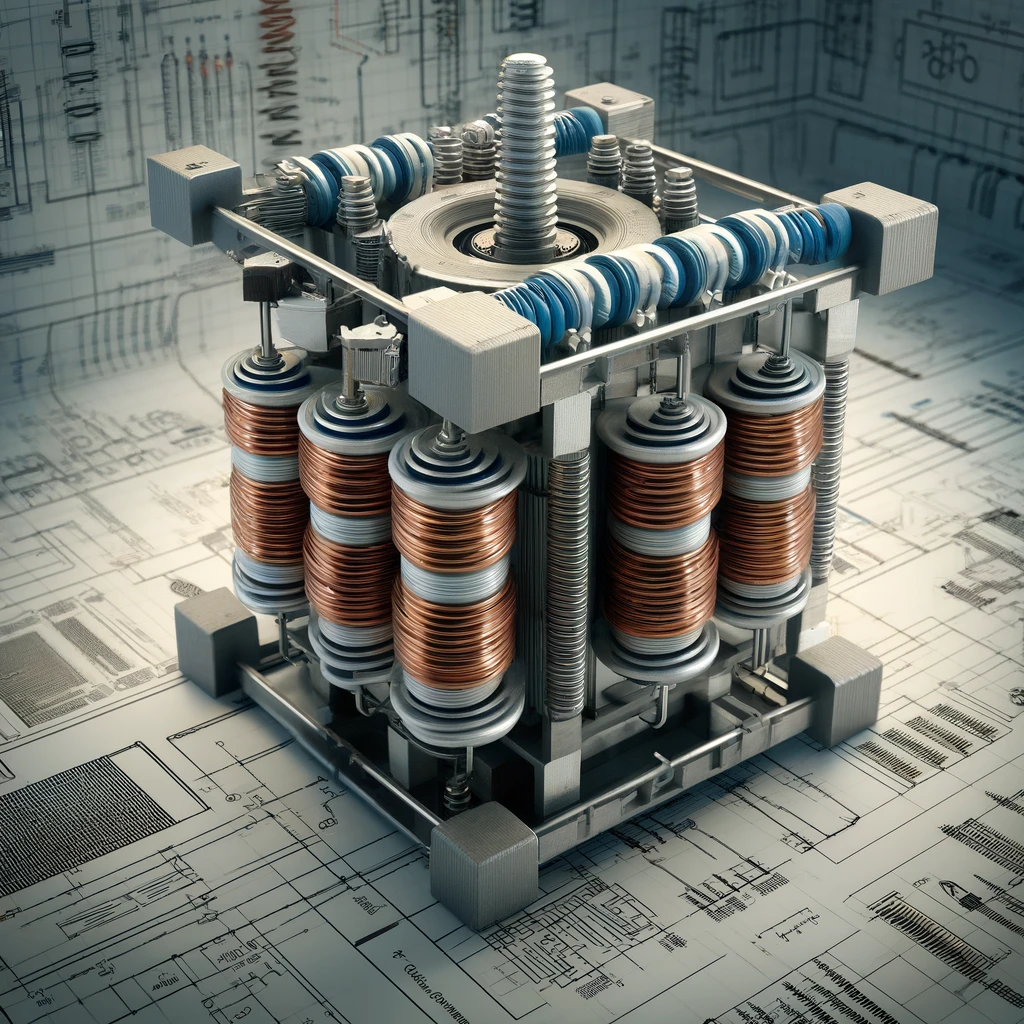
Unfolding the Tale: Insulation Paper in Transformers
Pushing back the curtain reveals an unsung hero of the transformer world—the humble insulating paper.
Predominantly crafted from pure cellulose, it stands as a crucial bulwark between the vital parts of a transformer, such as windings and core, preventing any inadvertent electrical connections or discharges.
Pulp to Paper: The Making
Transformers require insulation of high purity and mechanical strength. The process begins with extracting cellulose fibers either from the softwood or hardwood trees. The obtained wood pulp is then purified and beaten into a pulp slurry to release the thin, elongated cellulose fibers.
This slurry is then passed over a papermaking machine which, through a series of dewatering, pressing, and drying steps, forms long sheets of yet unfinished paper. Lastly, these unfinished sheets are loaded onto a supercalendering machine to achieve the desired thickness and smoothness.
The Paper’s Core Competency: Insulating Properties
Cellulose paper boasts high dielectric strength, making it an outstanding electrical insulator. It manages to create a physical barrier that obstructs the electrical connection between different windings or between the windings and the transformer’s metal body. Moreover, cellulose paper is quite flexible, allowing it to be cut or shaped conveniently to fit into intricate designs
Heat Transfer: An Auxiliary Benefit
Thanks to its porosity, cellulose paper also plays an auxiliary role in heat transfer. It has the ability to absorb transformer oils that aid in cooling the windings by absorbing the heat generated and moving it towards the radiator where the heat is shed.
The Wide Spectrum: Role Across Transformer Types
Insulating paper finds itself at the heart of a broad variety of transformers—right from the household transformers, like those in computer power supplies and audio equipment, to larger transformers used in power stations and industrial applications.
Distribution Transformers: A Common Denominator
In oil-immersed distribution transformers—those frequently seen in suburban neighborhoods—thin sheets of insulating paper separate the layers of windings and also isolate the windings from the iron core. This paper is often immersed in oil, which not only adds to the dielectric strength but also aids in cooling.
High Voltage Transformers: Insulation Intensified
High-voltage transformers, such as those in power plants, use thicker layers of insulating paper for increased dielectric strength. This helps endure the high electric fields inside these transformers while facilitating effective cooling.
Lifespan: Factors Affecting Durability
The life expectancy of paper insulation in a transformer is tightly intertwined with various factors, notably:
- Mechanical Strain: Mechanical vibrations and shocks can lead to wear and tear or even tearing of the insulation paper, thereby impacting its effectiveness.
- Thermal Stress: High operating temperatures accelerate the aging process, thereby reducing the insulation life. The temperature depends not just on loading conditions but also on the efficiency of the cooling system.
- Humidity: Moisture tends to lower the dielectric strength of the cellulose insulation.
- Oil Quality: The condition of the insulating oil in which the paper is immersed also influences the life of the paper insulation. Contaminated or poor-quality oil can speed up the paper’s degradation.
Insulation Material Evolution: Towards Modern Alternatives
While traditional cellulose paper continues to be the backbone of insulation in many transformers, new materials are making their foray into this domain. Synthetic materials, such as polymer films and aramid paper, have begun to find their niche in certain applications due to their unique advantages such as improved mechanical strength and chemical stability.
The Innovations:
Aramid paper, for instance, has high heat resistance and is largely impervious to aging, which extends its life as compared to cellulose. On the flip side, its high cost can be a deterrent.
Polymer films, such as polyester or polyimide, offer excellent tensile strength and dielectric properties, making them suitable for specific applications.
While these alternatives may not replace cellulose paper in every transformer, they add another dimension to the ever-evolving landscape of transformer insulation materials.
This echoes the key takeaway that understanding insulation materials, old and new, is central to understanding the intricacies of transformer functionality, lifespan, and safety.
Ending Our Talk On Transformer Insulation
With insulation playing such an integral role within transformers, acknowledging its two core functions – electrical separation and mechanical support – is paramount. In the variety of its forms, be it solid, liquid or gaseous, it commands our attention.
Solids, typically in the form of cellulosic paper and pressboards, are predominant while liquids such as mineral oil facilitate heat dissipation and gaseous alternatives like nitrogen offer extra safety precautions.
A well-rounded understanding of contributing factors such as transformer design, insulation material quality, ambient conditions, and maintenance can significantly enhance insulation performance and system longevity.
In essence, the ‘nitty-gritty’ of major insulation is this: it is fundamental to a transformer’s functionality, safety, and reliability, safeguarding it from both electrical and mechanical stresses. This integral component, though often overlooked, truly is the silent hero in efficient transformer operation.