An Introduction to Non-Destructive Testing (NDT) Methods
Ever wondered how we guarantee the safety and integrity of structures around us without damaging them?
Welcome to the world of Non-Destructive Testing (NDT), an essential quality control method within the construction industry.
NDT enables us to inspect materials and structures, find defects or irregularities, and do it all without causing any damage.
Now, isn’t that amazing?
In this article, we will explore the various NDT methods available – covering everything from Ultrasonic Testing and Magnetic Particle Testing to Non-Destructive Testing for concrete and bricks. We provide a detailed overview of each method’s working principle, common applications, advantages, and limitations.
So, are you ready to uncover the hidden intricacies of the material world without leaving a scratch?
Let’s jump right in!
Table of Contents
Methods of Non-Destructive Testing
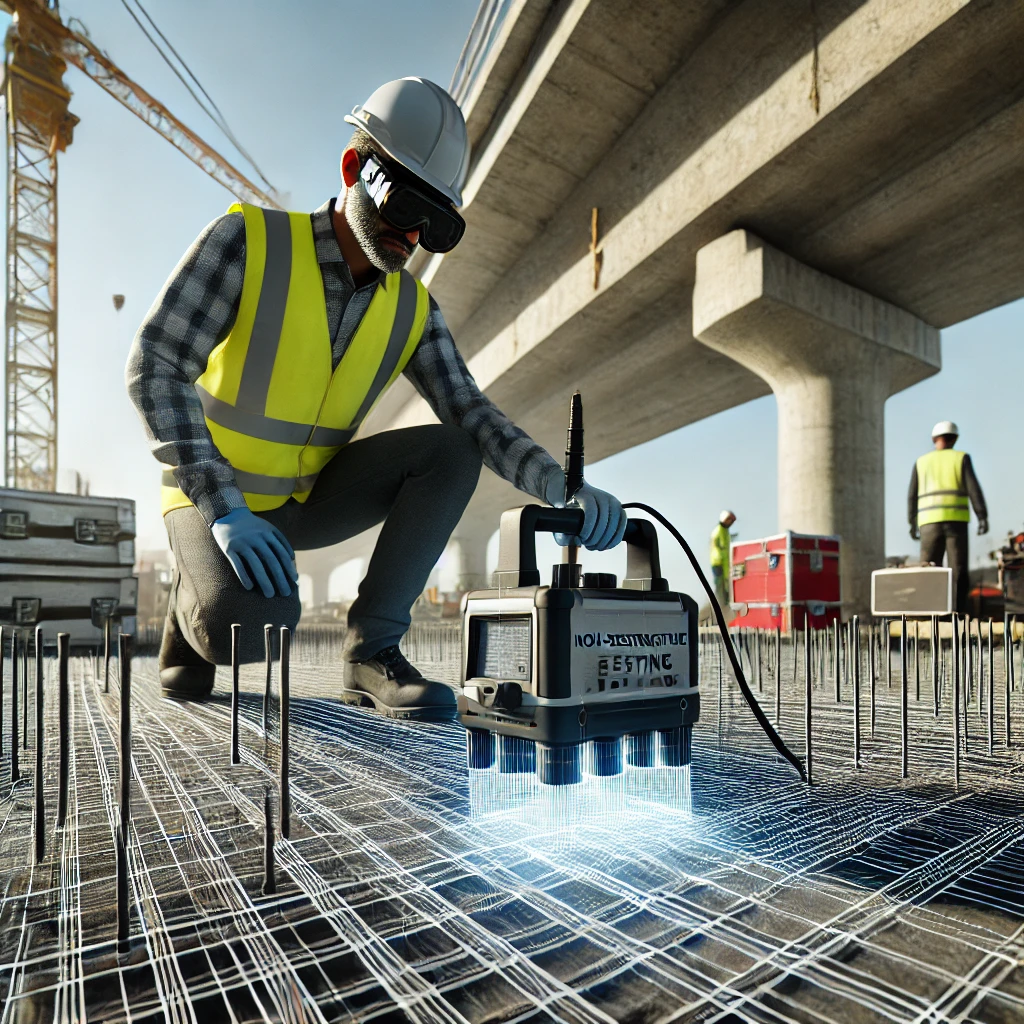
Overview of Non-Destructive Testing (NDT)
Non-Destructive Testing (NDT) is a key part of quality control in the construction industry. It allows for the inspection of materials and structures without causing any damage. Below, we’ll break down the primary methods of NDT.
Ultrasonic Testing (UT)
Ultrasonic Testing uses high-frequency sound waves to detect imperfections in materials.
- How it Works: Sound waves are sent through the material. The waves’ reflection patterns can identify flaws.
- Applications: Commonly used for weld inspections, metal thickness measurements, and flaw detection in metals and composites.
- Advantages: Highly accurate and capable of detecting very small defects.
- Limitations: Requires specialized equipment and training.
Magnetic Particle Testing (MT)
Magnetic Particle Testing identifies surface and slightly subsurface defects in ferromagnetic materials.
- How it Works: The material is magnetized. After applying magnetic particles, any discontinuities in the material will gather these particles, highlighting defects.
- Applications: Effective on welds, castings, and forgings.
- Advantages: Simple and cost-effective for detecting surface and near-surface flaws.
- Limitations: Only applicable to ferromagnetic materials.
Radiographic Testing (RT)
Radiographic Testing uses X-rays or gamma rays to view the internal structure of a component.
- How it Works: Radiation passes through the material onto a detector or film. Variations in material density appear as contrasting areas.
- Applications: Widely used in inspecting welds and castings.
- Advantages: Able to detect internal defects and provide a permanent record.
- Limitations: Potential health hazards due to radiation, requires strict safety protocols.
Liquid Penetrant Testing (PT)
Liquid Penetrant Testing is used to find surface-breaking defects in non-porous materials.
- How it Works: A liquid penetrant is applied to the surface. Excess liquid is removed, and a developer is used to draw out the penetrant from flaws, making them visible under UV or visible light.
- Applications: Suitable for metals, plastics, and ceramics.
- Advantages: Simple process and relatively inexpensive.
- Limitations: Only effective for surface defects.
Visual Testing (VT)
Visual Testing is the simplest form of NDT, relying on the human eye.
- How it Works: Inspectors visually examine materials and structures for defects.
- Applications: Universal application across various materials and structures.
- Advantages: Low cost, easy to perform, and immediate results.
- Limitations: Limited by the inspector’s ability and the requirement for good lighting and accessibility.
Comparative Table of NDT Methods
Method | Applications | Advantages | Limitations |
---|---|---|---|
Ultrasonic Testing (UT) | Metals, composites, weld inspections | Highly accurate, detects small defects | Requires specialized equipment |
Magnetic Particle Testing (MT) | Welds, castings, forgings | Simple, cost-effective | Only for ferromagnetic materials |
Radiographic Testing (RT) | Welds, castings | Detects internal defects, provides records | Health hazards, safety protocols needed |
Liquid Penetrant Testing (PT) | Metals, plastics, ceramics | Simple, inexpensive | Effective for surface defects only |
Visual Testing (VT) | Various materials and structures | Low cost, easy to perform | Limited by human ability |
For more information on Non-Destructive Testing methods, visit this ASNT (American Society for Nondestructive Testing) page.
Non-Destructive Testing of Bricks
Importance of NDT in Brick Testing
Like other construction materials, bricks require testing to ensure their quality and durability. Non-Destructive Testing (NDT) for brick analysis enables us to assess their condition without damaging the material or the structures containing it. This becomes especially significant in the context of historical or architectural sites where conservation is paramount.
NDT Techniques Used For Brick Testing
While the general NDT techniques remain the same, their application may vary when used for brick testing. Let’s explore more about the brick-focused uses of these methods.
- Acoustic Impact Technique: An adapted form of ultrasonic testing. It uses impact-echo generated by small hammer strikes. The resulting signals help identify discontinuities in the brick or masonry.
- Radar or Ground Penetrating Radar (GPR): An enhancement of the radiographic tests. GPR identifies subsurface defects using electromagnetic radiation. The radar detects changes in the returned signals due to variance in brick density or moisture content.
- Thermal Imaging: This non-invasive technique involves the use of infrared thermography. Variations in thermal properties across the brick or masonry surface can highlight potential defects.
- Visual Inspection: Like other materials, visual inspection remains the most straightforward NDT method for bricks. Natural or artificial light reveals surface cracks, chips, and wear and tear.
Considerations for Non-Destructive Brick Testing
While NDT offers significant advantages, there are several factors to keep in mind when applying these methods to bricks.
- Environmental Conditions: Weather conditions can affect the readings of some NDT methods, such as thermal imaging.
- Surface Moisture: The presence of moisture in brick can also affect certain NDT methods, especially those relying on electrical or thermal properties.
- Experience Required: As with other NDT applications, the results’ accuracy often hinges on the operator’s experience and understanding of the testing equipment and techniques.
Comparative Table of NDT Methods for Bricks
Method | Applications | Advantages | Limitations |
---|---|---|---|
Acoustic Impact Technique | Brick and Masonry Inspection | Accurate internal defect detection | Requires special equipment; Defects can be missed without sufficient strikes |
Radar / GPR | Brick Inspection, especially for Historical Sites | Accurate subsurface defect detection | Can misinterpret readings without proper calibration |
Thermal Imaging | Brick and Masonry Inspection | Non-invasive; Identifies sub-surface anomalies | Affected by environmental conditions |
Visual Inspection | General Brick Inspection | Simple, Low Cost | Can only identify visible defects |
Research into more methods of NDT for brick testing keeps advancing. To stay current, consider bookmarking the ResearchGate page. It offers the latest publications and studies about NDT and its specialized applications.
Advanced Methods of Non-Destructive Testing for Concrete
Importance of Non-Destructive Testing in Concrete Structures
Concrete is fundamental in building infrastructure, making its integrity critical. Non-Destructive Testing (NDT) methods help identify potential weaknesses without damaging the material, ensuring safety and longevity of structures.
Common NDT Techniques for Concrete
Several advanced NDT techniques go beyond traditional methods and are specifically designed for concrete structures. Here are some of the key methods used:
- Rebound Hammer Testing: This method is commonly known as Schmidt Hammer Test.
- How it Works: A hammer impacts the concrete surface, and the rebound distance is measured to determine surface hardness, which correlates to compressive strength.
- Applications: Primarily used for surface hardness testing of concrete.
- Advantages: Simple, quick, and relatively inexpensive.
- Limitations: Only assesses surface hardness; not reliable for identifying deep flaws.
- Ground Penetrating Radar (GPR): Utilizes radar pulses to image the subsurface.
- How it Works: Radiowaves are sent into the concrete, and reflected signals indicate the presence of anomalies based on variations in material density.
- Applications: Locating rebar, voids, and cracks within the concrete structure.
- Advantages: Provides detailed data on subsurface conditions.
- Limitations: Results may be misinterpreted without proper calibration and expertise.
- Infrared Thermography: Identifies heat patterns to reveal structural inconsistencies.
- How it Works: Infrared cameras capture thermal images of the concrete surface, identifying hot and cold spots that indicate flaws or moisture intrusion.
- Applications: Used to detect delaminations, voids, and water ingress.
- Advantages: Non-contact, quick, and can cover large areas.
- Limitations: Effectiveness can be influenced by environmental conditions.
- Impact-Echo Testing: Detects internal flaws using stress waves.
- How it Works: A transducer generates a mechanical impact, and sensors capture the echo of stress waves reflected from internal defects.
- Applications: Effective in locating voids, delaminations, and cracks.
- Advantages: Provides comprehensive internal structural analysis.
- Limitations: Requires specialized equipment and interpretation; sensitive to signal interference.
- Ultrasonic Pulse Velocity (UPV): Measures travel time of ultrasonic pulses.
- How it Works: Transducers send ultrasonic pulses through the concrete; the travel time between transmitting and receiving transducers indicates material density and integrity.
- Applications: Used for detecting cracks, voids, and uniformity within the concrete.
- Advantages: Provides detailed internal condition data.
- Limitations: Requires good contact between transducers and the concrete surface; affected by moisture content and aggregate type.
Other Considerations in NDT for Concrete
When applying NDT methods to concrete, several factors should be considered to ensure accurate and reliable results:
- Material Properties: The composition and aggregate type in concrete can influence the effectiveness of certain NDT methods.
- Surface Preparation: Proper surface preparation is crucial for techniques requiring direct contact, such as UPV.
- Calibration: Regular calibration of equipment is necessary to avoid misinterpretation of data.
- Environmental Factors: Conditions such as temperature, humidity, and surface moisture can affect readings, particularly in methods like infrared thermography or GPR.
Comparative Table of Advanced NDT Methods for Concrete
Method | Applications | Advantages | Limitations |
---|---|---|---|
Rebound Hammer | Surface hardness | Simple, quick, inexpensive | Only surface-level, not for deep defects |
Ground Penetrating Radar | Subsurface defect detection | Detailed subsurface data | Calibration needed; expertise required |
Infrared Thermography | Thermal property variances | Non-contact, covers large areas | Affected by environmental conditions |
Impact-Echo | Internal defect detection | Comprehensive internal analysis | Signal interference; expertise needed |
Ultrasonic Pulse Velocity | Detecting cracks, voids | Detailed internal condition | Good contact required; affected by material properties |
To further explore these methods, you can learn more by visiting the National Center for Biotechnology Information (NCBI) for research papers and detailed studies on advanced NDT techniques for concrete.
Non-Destructive Testing for Mortar
What is the NDT Test for Mortar?
Non-Destructive Testing (NDT) for mortar is a process to examine the quality, condition, and integrity of mortar without causing damage to the structure. Mortar, which cements blocks or bricks together, is crucial for the longevity and stability of masonry structures. Proper testing ensures that the mortar can adequately support the load and resist environmental factors.
Key NDT Techniques for Testing Mortar
Several specialized NDT techniques are particularly effective for testing mortar:
- Ultrasonic Pulse Velocity (UPV):
- How it Works: Ultrasound waves are transmitted through the mortar, and the pulse velocity is measured. Variations in velocity indicate different properties like density and integrity.
- Applications: Ideal for assessing the homogeneity and strength of mortar joints.
- Advantages: Non-invasive and provides detailed insights into the internal condition of mortar.
- Limitations: Requires good surface interaction and can be influenced by moisture and aggregate types in the mortar.
- Rebound Hammer Testing:
- How it Works: Similar to concrete testing, a hammer strikes the mortar surface, and the rebound is measured to determine hardness.
- Applications: Used for surface hardness assessment, which correlates with the mortar’s compressive strength.
- Advantages: Simple, quick, and cost-effective.
- Limitations: Primarily surface-level analysis, not useful for assessing deeper properties or defects.
- Infrared Thermography:
- How it Works: Thermal cameras capture heat distribution on the mortar surface, identifying imperfections based on thermal variances.
- Applications: Effective in identifying voids, moisture ingress
Conclusion
Non-Destructive Testing (NDT) methods are indispensable tools in the construction industry, allowing us to maintain and ensure the safety, durability, and quality of structures without compromising their integrity.
From ultrasonic testing to infrared thermography, each method offers unique insights into materials like concrete, bricks, and mortar, enabling precise detection of defects and weaknesses.
As technology evolves, so too do these methods, continually improving our ability to assess and maintain infrastructure with minimal disruption.