Introduction to Refractory Masonry
Have you ever wondered about the science behind withstanding high temperatures in industries like steel production or glass manufacturing?
The answer lies in the hands of a refractory mason and their masterful use of heat-resistant materials.
In this article, we’ll discuss the vital role refractory masons play in various industries, the specific skills they hone, and the responsibilities they undertake. We’ll also explore the different types of refractory materials they use, from bricks to cements, and why these materials are essential to industrial applications.
Let’s fire up this article and get started.
Table of Contents
Refractory Masons in Construction
Understanding a Refractory Mason
A refractory mason specializes in installing and maintaining refractory materials. These materials are highly resistant to heat and are essential in industries that involve high-temperature processes.
Key Roles and Responsibilities
Installation of Refractory Materials
- Bricks
- Castables
- Mortars
- Plastic Refractories
Maintenance and Repairs
Refractory materials wear out over time and require regular maintenance:
- Inspecting wear and damage
- Replacing damaged materials
- Applying patches to extend the lifespan
- Cleaning and resurfacing surfaces
Importance in Various Industries
Refractory masons are essential in sectors where high temperatures are common:
Industry | Application |
---|---|
Steel | Lining furnaces, ladles, and converters |
Glass | Constructing tank furnaces and regenerators |
Cement | Lining kilns and coolers |
Chemical | Reactor and boiler linings |
Skills and Qualifications
Becoming a refractory mason requires specific skills and training:
- Knowledge of refractory materials and their properties
- Welding and cutting torch skills
- Physical stamina and manual dexterity
- Experience in construction or masonry work
Refractory masons play a vital role in maintaining the integrity and efficiency of high-temperature industrial processes. Their expertise ensures safe and effective operation in environments where regular masonry materials would fail.
The Role of Refractory Bricks in Industrial Applications
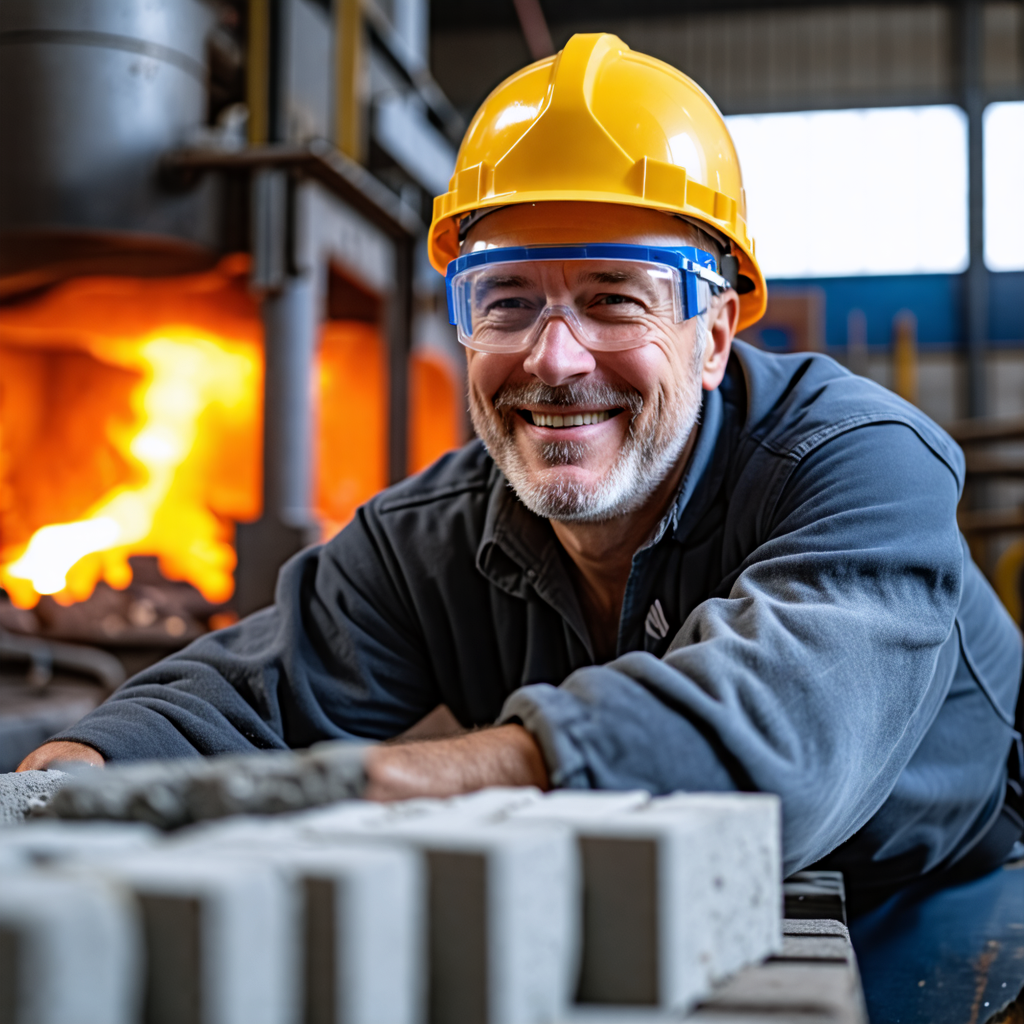
What is a Refractory Brick?
Drawing from the broader role of refractory materials, the refractory brick is a subcategory that merits its own description. A refractory brick, also known as a firebrick, is a block of refractory ceramic material used in lining kilns, furnaces, fireplaces, and other high-heat environments. Its primary purpose is to withstand high temperature and simultaneously sustain mechanical load.
Distinct Properties of Refractory Bricks
To perform these roles effectively, refractory bricks exhibit several defining properties.
Heat Resistance
A defining characteristic of refractory bricks is their ability to resist high temperatures. These bricks can withstand intense heat up to 1700 degrees Celsius, making them suitable for various high-temperature industrial applications.
Low Thermal Conductivity
Refractory bricks also have low thermal conductivity, meaning they can resist the transfer of heat. Due to this, they exemplify the ideal construction material for maintaining temperature boundaries within furnaces and kilns.
Density and Structural Strength
Apart from heat resistance, refractory bricks need to bear substantial loads, especially in industrial kilns and furnaces. Therefore, these bricks ought to possess a high density and mechanical strength to resist the physical stresses of these environments.
Classification of Refractory Bricks
Refractory bricks can be categorized into several types based on their composition and performance.
Fireclay Bricks
Constructed with the mineral kaolinite, fireclay bricks offer excellent resistance to heat and chemical attack. They’re commonly used in blast furnaces, hot stoves, glass kilns, and steel-making furnaces.
High Alumina Bricks
Containing a high percentage of alumina, these bricks are appreciably resistant to corrosion and can endure extremely high temperatures. They are often used in melting tanks of glass furnaces, cement rotary kilns, and electric arc furnaces.
Carbon Bricks
Carbon bricks possess high temperature bearing capacity and good resistance to acid and alkali. They’re typically used for linings in high-temperature equipment in the metallurgical industry.
For a detailed breakdown of the different types of refractory bricks, the Refractories Handbook can be an excellent resource.
Refractory Brick Manufacturing
Brick making is a complex process, involving several stages, from the gathering of raw material to the final product. This process includes steps like material preparation, forming, drying, and firing. All these stages require specialized skill, underlining the centrality of refractory masons in this industry.
Refractory Cement vs. Regular Cement
What is Refractory Cement?
Refractory cement, also known as heat-resistant cement, is a specialized type of cement used in high-temperature applications. Composed of materials like calcium aluminate, its unique formulation makes it suitable for environments with extreme heat.
Properties of Refractory Cement
- Heat Resistance: Designed to withstand high temperatures, typically up to 1600 degrees Celsius (2912 degrees Fahrenheit).
- Thermal Stability: Maintains its structural integrity under temperature fluctuations.
- Chemical Resistance: Resists attack from acids, alkalis, and slags, making it ideal for use in industrial and metallurgical processes.
- Durability: Provides long-lasting performance in high-temperature environments.
What is Regular Cement?
Regular cement, often referred to as Portland cement, is the most common type of cement used for general construction purposes. It serves as the basic component of concrete, mortar, stucco, and non-specialty grout.
Properties of Regular Cement
- Compressive Strength: Provides high compressive strength, making it ideal for structural applications.
- Setting Time: Quick setting time suitable for construction purposes but can vary depending on the mix and additives.
- Versatility: Can be mixed with various aggregates and materials to fit many construction needs.
- Cost-Effectiveness: Generally less expensive than refractory cement due to its widespread availability and use.
Key Differences Between Refractory Cement and Regular Cement
Understanding the differences between these two types of cement is essential for selecting the right material for your project.
Feature | Refractory Cement | Regular Cement |
---|---|---|
Temperature Resistance | Up to 1600°C (2912°F) | Around 200°C (392°F) |
Chemical Composition | High in calcium aluminate | Mostly calcium silicates |
Applications | Furnaces, fireplaces, kilns | Buildings, bridges, roads |
Cost | Higher | Lower |
Durability in High Temp | High | Low |
For more comprehensive information on the differences and uses of these cements, you can check out [this article on The Constructor](https://theconstructor.org/).
Why Choose Refractory Cement?
- Industrial Applications: Essential for industries like steel, ceramics, and glass where extreme heat is a factor.
- Safety: Prevents structural failure due to heat degradation, ensuring safety in high-temperature environments.
- Longevity: Reduces the frequency of repairs and maintenance in high-temperature setups, providing long-term benefits.
What is the difference between bricks and refractory bricks?
Understanding Standard Bricks
Standard bricks, typically made from clay, are widely used in construction due to their durability and strength. They are primarily designed for building walls, houses, and other structures that require a strong, long-lasting material.
Properties of Standard Bricks
- Composition: Made from clay or shale, often mixed with sand and other minerals.
- Heat Resistance: Standard bricks can withstand moderate temperatures, usually up to 1000 degrees Celsius.
- Density and Strength: Good compressive strength suitable for structural applications, but not specifically designed for thermal resistance.
- Applications: Commonly used in residential and commercial construction, landscaping, and decorative projects.
Refractory Bricks
Refractory bricks, also known as firebricks, are designed to withstand extreme heat. They are essential in industries that involve high-temperature processes, such as metallurgy, glassmaking, and ceramics.
Properties of Refractory Bricks
- Composition: Made from materials like alumina, silica, and other refractory minerals.
- Heat Resistance: Capable of withstanding temperatures up to 1700 degrees Celsius or higher, depending on the type.
- Low Thermal Conductivity: Helps in maintaining temperature boundaries within furnaces and kilns.
- Density and Structural Strength: High density and mechanical strength to resist physical stresses in industrial settings.
Key Differences Between Standard Bricks and Refractory Bricks
Here is a comparison table that highlights the key differences between standard bricks and refractory bricks:
Feature | Standard Bricks | Refractory Bricks |
---|---|---|
Material Composition | Clay or shale, mixed with sand and minerals | Alumina, silica, and other refractory materials |
Heat Resistance | Up to 1000°C (1832°F) | Up to 1700°C (3092°F) or higher |
Thermal Conductivity | Moderate | Low |
Applications | Construction of buildings, walls, landscaping | Lining furnaces, kilns, fireplaces, high-heat industrial applications |
Cost | Lower, due to widespread use and availability | Higher, due to specialized materials and manufacturing process |
Why Use Refractory Bricks?
Understanding the specific needs of your project is essential for selecting the right type of brick. Refractory bricks are indispensable for applications involving high temperatures, such as:
- Industrial Furnaces: Used to line the interiors to withstand and contain extreme heat.
- Kilns: Essential for pottery, ceramics, and metalwork where high temperatures are involved.
- Fireplaces and Wood-Burning Stoves: Ensures structural integrity and safety by containing the heat.
For detailed descriptions of refractory materials and their uses, you might find the Refractories Worldforum useful.
Conclusion
The roles and responsibilities of the refractory mason in various industries, the properties of refractory bricks, refractory cement, firebricks, and their differentiation from regular bricks and cement, form the crux of this article.
A refractory mason aids the installation and maintenance of refractory materials, that are mainly heat-resistant. These materials involve bricks, castables, mortars, etc. Their maintenance includes resurfacing, inspecting wear and damage, and various others.
The refractory mason further comes into use in several industries where high temperatures are involved, such as steel, cement, chemical etc.
Frequently Asked Questions – FAQs
What is the role of a refractory mason?
A refractory mason specializes in the installation and maintenance of heat-resistant materials, known as refractory materials. These are essential in industries that involve high-temperature processes.
What is refractory cement and how is it different from regular cement?
Refractory cement, or heat-resistant cement, is designed for high-temperature applications. It’s made from calcium aluminate and can withstand temperatures up to 1600°C. Regular cement, however, is primarily composed of calcium silicates and can only resist up to around 200°C.
What is a refractory brick?
Refractory bricks, or firebricks, are designed to withstand extreme heat. They’re made from materials like alumina and silica, and are used in industries like metallurgy, glassmaking, and ceramics, where high-temperature tolerance is essential.
What is the difference between standard bricks and refractory bricks?
Standards bricks, made from clay or shale, are designed for general construction purposes and can resist up to 1000°C. Refractory bricks, on the other hand, are made from specialized materials and can resist heat up to 1700°C or higher. They’re primarily used in high-temperature industrial applications.