Introduction to Vitrification in Construction Materials
Have you ever wondered how bricks gain their strength or ceramics attain their glossy surface?
These wonders are a result of a fascinating process called vitrification.
In this article, we will explain the process, properties, uses, and comparative benefits of vitrified bricks and ceramics. From masonry to ceramics, from the burning of bricks to their usage, we explore the nuances of vitrification.
Finally, we address its purpose in brick strength, water and chemical resistance, heat conductivity, and aesthetic qualities.
By the end of this article, not only will you understand what vitrification is, but you’ll also gain insights into how it impacts our daily lives – in the homes we live in, the pavements we walk on, and even the bathrooms we use.
Fire up the kiln – let’s start baking these bricks!
Table of Contents
What is a Vitrified Brick?
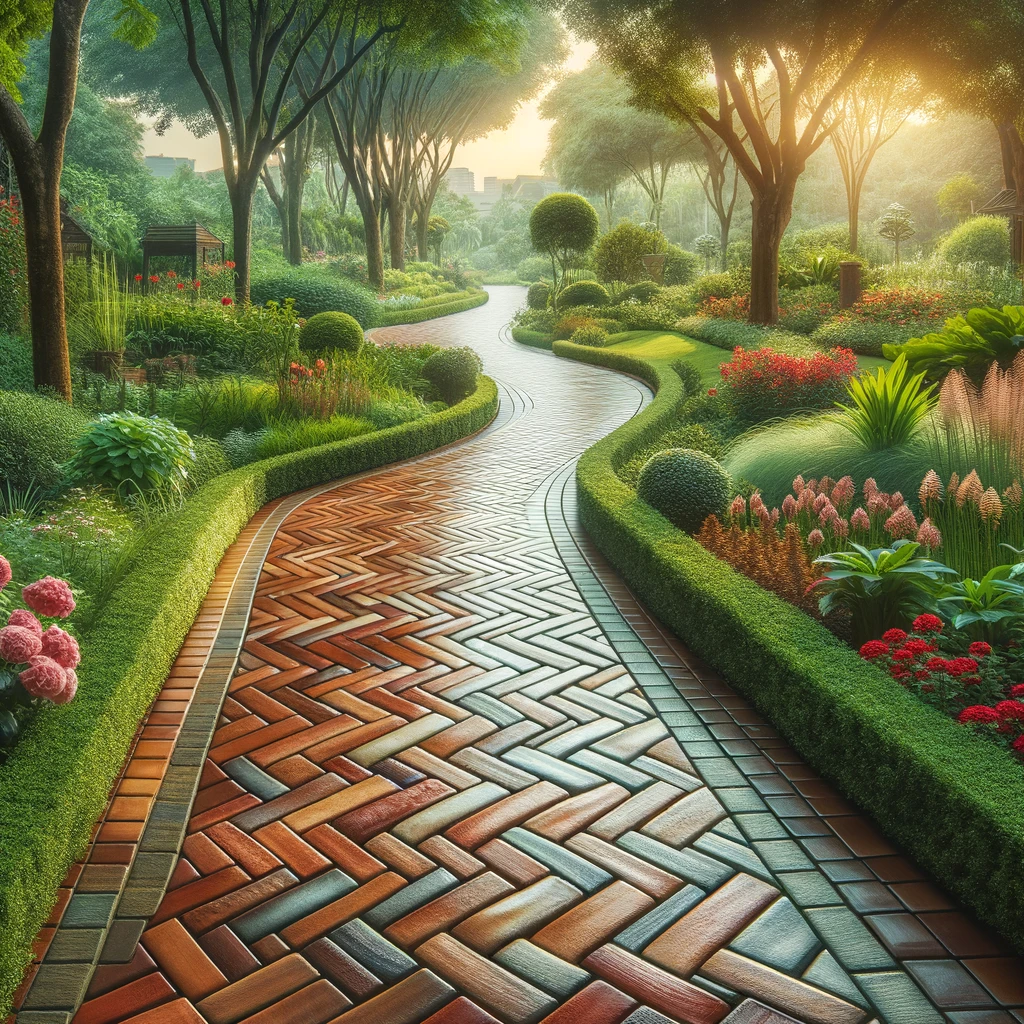
Definition of Vitrified Brick
Vitrified bricks are a type of brick that is fired at extremely high temperatures until they achieve a glass-like, non-porous surface. This process results in a brick that is exceptionally strong, durable, and water-resistant.
Characteristics of Vitrified Bricks
- Non-porous Surface: Due to the high firing temperature, vitrified bricks have a glassy finish that makes them impermeable to water.
- High Durability: These bricks are much stronger than ordinary bricks, making them ideal for heavy-duty applications.
- Aesthetic Appeal: The smooth, glossy surface of vitrified bricks adds a refined look to any construction.
- Low Maintenance: Their resistance to moisture and chemicals means they require less upkeep.
Uses of Vitrified Bricks
Vitrified bricks are commonly used in both residential and commercial construction projects due to their resilience and attractive appearance. Some typical applications include:
- Paving
- Exterior walls
- Interior walls (especially in areas exposed to moisture)
- Load-bearing structures
Comparison: Vitrified Bricks vs. Ordinary Bricks
Feature | Vitrified Bricks | Ordinary Bricks |
---|---|---|
Water Resistance | High | Low |
Strength | High | Moderate |
Maintenance | Low | High |
Aesthetic Quality | Glossy & Smooth | Rough & Porous |
How Vitrified Bricks are Made
The process of creating vitrified bricks involves several key steps:
- Material Selection: Fine clay and other materials are chosen to ensure the brick can withstand high temperatures.
- Firing: The bricks are fired in a kiln at temperatures typically exceeding 1,000 degrees Celsius.
- Vitrification: During firing, the materials melt and fuse, forming a glassy, non-porous surface.
Benefits of Using Vitrified Bricks
- Enhanced Durability: Ideal for structures that require long-lasting material.
- Improved Aesthetic Appeal: Offers a polished look for various applications.
- Reduced Maintenance Costs: The non-porous surface resists stains and water damage.
- Eco-Friendly: Less environmental degradation due to lower water absorption and reduced maintenance needs.
The Vitrification Process in Masonry
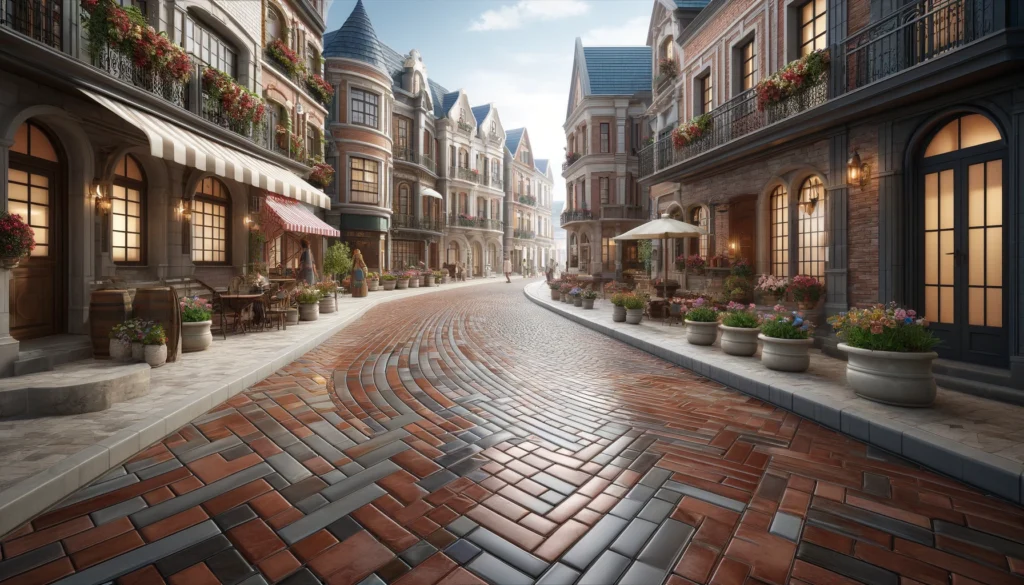
A Deeper Look Into Masonry Vitrification
Vitrification in masonry refers to the process where certain types of bricks, commonly known as vitrified bricks, are subjected to extremely high temperatures. This exposure to intense heat causes the clay and other materials in the bricks to melt and fuse together, creating a glossy, smooth, and non-porous surface that enhances the brick’s overall durability and aesthetic appeal.
Vitrification: A Temperature-Dependent Process
The vitrification process is essential in determining the end attributes of a brick and relies heavily on the temperature at which the brick is fired. Vitrification typically begins at about 800 degrees Celsius and could reach up to 1,200 degrees Celsius. The exact temperature required for vitrification can vary based on the type of clay used and its mineral composition.
Key Elements Influencing Vitrification
- Kiln Design: The design of the kiln has a significant impact on the rate of heat generation and cooling, both of which are crucial in the vitrification process.
- Heat Source: The kind of fuel used to generate heat can also influence the final product. Typical fuels include coal, gas, and wood.
- Clay Type: The degree of vitrification can be controlled by choosing different kinds of clay, such as kaolin, ball clay, or fire clay.
Stages of Vitrification
Vitrification happens in three stages:
- Dehydration: Water is removed from the clay. This normally occurs between 100 and 200 degrees Celsius.
- Oxidation: Between 800 degrees Celsius and 1,200 degrees Celsius, the clay undergoes chemical changes, leading to firmness.
- Fusion: The high point of vitrification. Here, the clay particles start to fuse together, forming a solid, glass-like structure.
The Drawbacks of Over-Vitrification
While the vitrification process gives our bricks a distinct set of advantageous properties, over-vitrification can cause problems. Bricks that are over-vitrified can become brittle and may be more susceptible to damage over time.
Vitrification and Environmental Impact
Vitrified bricks have a lower environmental impact compared to other types of bricks. Thanks to their high resistance to water and chemicals, less water and cleaning supplies are needed for their maintenance.
This means less water waste and lower amounts of chemical pollutants entering our waterways.
What Does Vitrified Mean in Ceramics?
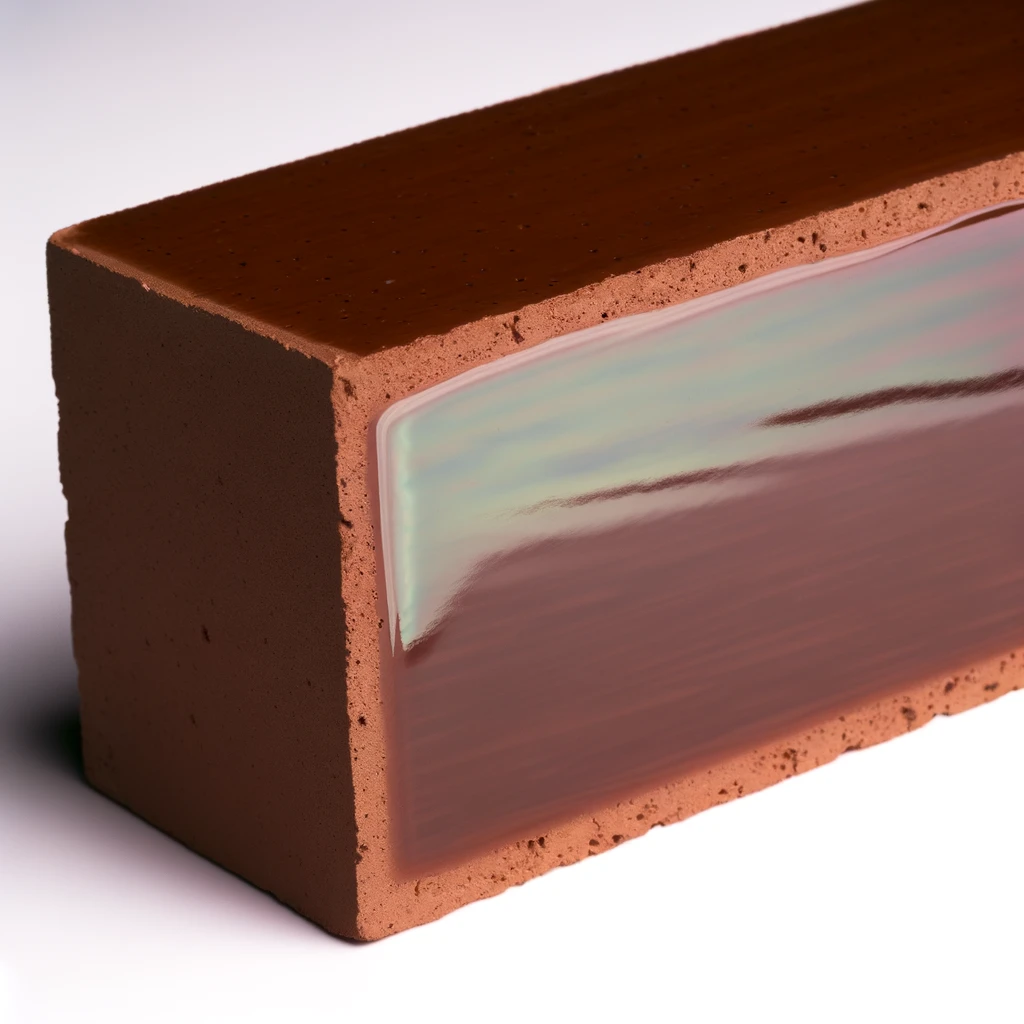
Defining Vitrification in Ceramics
In ceramics, vitrification is the process of transforming a material into a glass-like, non-crystalline state by heating it to high temperatures. This process makes the material dense, non-porous, and usually, very hard, similar to glass. Vitrification is essential for producing ceramics that are impervious to water and resistant to wear and tear.
Applications of Vitrified Ceramics
Vitrified ceramics are used in a variety of applications due to their robust properties. Common uses include:
- Tableware: Plates, bowls, and mugs made from vitrified ceramics are durable and safe for food use.
- Sanitaryware: Bathroom fixtures like sinks, toilets, and bathtubs are often made from vitrified ceramics.
- Tiles: Floor and wall tiles are commonly vitrified to ensure they are water-resistant and easy to clean.
- Lab Equipment: Laboratory crucibles and other high-temperature resistant items are often made from vitrified materials.
Vitrification Process in Ceramics
The vitrification process is an essential step in ceramic manufacturing and involves several stages:
- Preparation of Raw Materials: The selected clay and other raw materials are mixed and prepared for shaping.
- Shaping: The material is shaped into the desired form, whether it’s a tile, bowl, or sanitaryware piece.
- Drying: The shaped material is dried to remove most of the water content.
- Firing: The material is fired in a kiln at temperatures often exceeding 1,000 degrees Celsius, causing the materials to undergo chemical changes and the vitrification process begins.
- Cooling: Controlled cooling solidifies the material into a dense, glass-like finish.
Advantages of Vitrified Ceramics
Vitrified ceramics offer several benefits which make them highly sought after in various industries:
- Water Resistance: The non-porous nature makes them ideal for locations exposed to water and moisture.
- Durability: High strength and resistance to wear extend the lifespan of the ceramic products.
- Ease of Cleaning: The glass-like surface makes cleaning easy, saving time and maintenance costs.
- High Aesthetic Value: Vitrified ceramics come in a variety of finishes, enhancing the visual appeal of any installation.
Industrial Relevance of Vitrified Ceramics
Vitrified ceramics have a significant role in industrial applications due to their superior performance in high-stress environments. Industries such as automotive, aerospace, and manufacturing extensively use vitrified ceramics for components that require high mechanical strength and stability at elevated temperatures.
What is the Purpose of Vitrification during the Burning of Bricks?
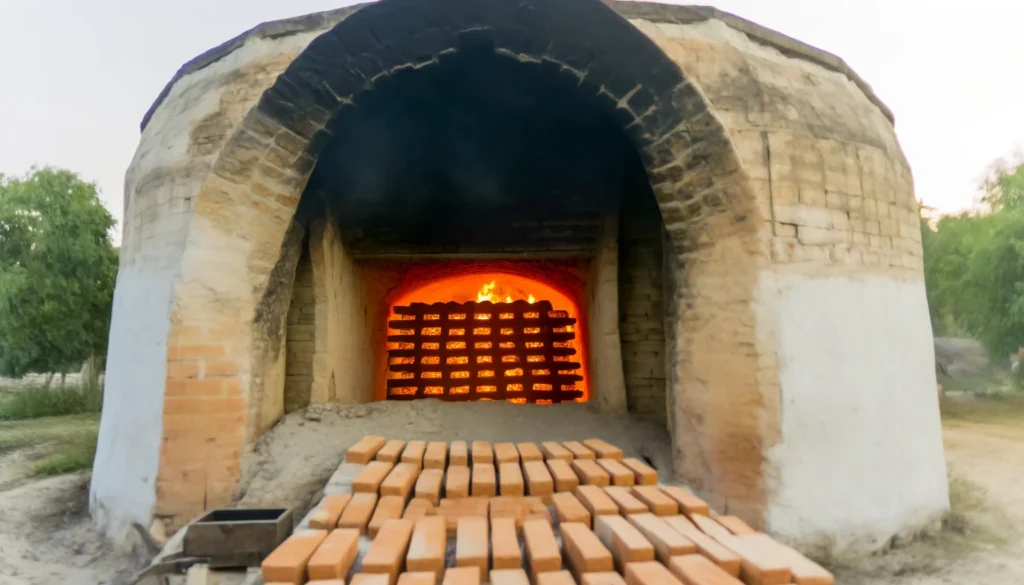
The Role of Vitrification in Brick Strength
Vitrification serves an essential function in enhancing the physical properties of bricks. When bricks undergo vitrification, the transformation of the clay and other materials at high temperatures leads to the formation of a fusion-bonded structure. This structure vastly improves the brick’s mechanical strength, making it capable of withstanding substantial loads and stresses. As a result, vitrified bricks are ideal for applications that require both durability and robustness.
Water and Chemical Resistance Through Vitrification
Another vital purpose of vitrification is to increase the brick’s resistance to water and chemicals. The high-temperature firing process melts the minerals in the clay, which then cool to form a glass-like coating over the brick. This coating prevents water absorption and chemical infiltration, making vitrified bricks suitable for environments that are prone to moisture, such as bathrooms or exterior walls.
Heat Conductivity and Insulation Properties
Vitrification influences the thermal properties of bricks as well. The dense, fused structure resulting from vitrification reduces the brick’s ability to conduct heat. This makes vitrified bricks somewhat more effective as insulating materials compared to ordinary bricks. Structures built with vitrified bricks can help maintain indoor temperatures more efficiently, thereby conserving energy.
Impact on Aesthetic Qualities
The vitrification process not only improves the brick’s functional properties but also enhances its aesthetic appeal. The glass-like surface layer formed during vitrification provides a glossy and smooth finish that is visually appealing. This can be particularly beneficial for architectural projects where both durability and aesthetics are of paramount importance. The sleek surface also supports various decorative finishes, offering designers a versatile building material.
A Look at Kiln Technologies in Vitrification
The type of kiln used in the vitrification process has a significant impact on the final quality of the bricks. Modern kilns provide better control over temperature, airflow, and atmosphere within the firing chamber. These advancements in kiln technology ensure a more uniform and consistent vitrification process. Notably, electric and gas kilns allow for precise temperature management crucial for high-quality vitrification, whereas traditional coal-fired kilns might yield more variable results.
Economic Benefits of Vitrified Bricks
While vitrified bricks may have a higher upfront cost compared to ordinary bricks, their long-term economic benefits can be substantial. The increased durability and low maintenance requirements mean fewer repairs and replacements over the brick’s lifespan. Additionally, their improved thermal insulation properties can contribute to energy savings in heating and cooling costs for buildings, offering further economic advantages.
Sustainability Considerations
From an environmental standpoint, vitrified bricks offer several sustainability benefits. The improved durability means longer-lasting structures, which reduces the frequency of rebuilding and associated environmental impacts.
Additionally, the reduced water absorption and better maintenance qualities decrease the need for cleaning agents and maintenance materials, further lessening the environmental footprint. According to a study published on ScienceDirect, these properties contribute significantly to the bricks’ eco-friendly credentials.
Wrapping it Up: The Unmatched Qualities of Vitrified Bricks and Ceramics
The world of vitrified bricks and ceramics is both fascinating and extensive.
They offer durability, resistance to water and chemicals, and an aesthetic appeal unmatched by other materials. Not only do they play a significant role in construction and various industries due to their strength and attractiveness, but their production process is also quite captivating.
A product of extreme temperatures, vitrified materials are non-porous and resilient. Understanding their creation process makes it clear why they possess such durability, especially when compared to their non-vitrified counterparts. Their glass-like finish also contributes to their visually pleasing appearance, making them suitable for both aesthetic and functional applications in construction.
The sustainability of vitrified bricks and vitrified ceramics is another key feature to highlight, as they produce fewer pollutants and require less water and maintenance materials, promoting eco-friendliness. Thus, choosing vitrified materials is a sound decision for both practical and environmental reasons.
Frequently Asked Questions – FAQs
What is the main advantage of vitrified bricks over ordinary ones?
The main advantage lies in their superior durability, water resistance, and aesthetic appeal, thanks to the vitrification process that gives these bricks a smooth and glassy finish.
Why are vitrified ceramics commonly used in construction?
Vitrified ceramics are used extensively in construction because of their strength, water resistance, and easy-to-clean surfaces. Their glassy finish also enhances the aesthetics of any building project.
Are vitrified bricks environmentally friendly?
Yes, vitrified bricks are considered more eco-friendly than their non-vitrified counterparts. They absorb less water, need fewer cleaning agents, and last longer, reducing their environmental impact over the long term.
What is the process of vitrification in masonry and ceramics?
Vitrification is a process where bricks or ceramics are heated to exceptionally high temperatures, causing the materials to fuse together, forming a dense, non-porous, and glass-like substance. This process enhances the physical properties of the resulting product.
Does the kind of kiln used affect the quality of vitrified bricks?
Absolutely, the type of kiln can significantly impact the final product’s quality. Modern kilns provide better control over temperature and airflow, essential elements in the vitrification process.