An Introduction To Refractory Bricks: A Comprehensive Guide
Ever wondered about the type of bricks that can withstand scorching temperatures and harsh environments?
Regular bricks would simply crumble under such conditions. Yet, there are specially engineered bricks that don’t. Called “refractory bricks” or “fire bricks,” these are what our discussions will revolve around.
Curious about what refractory bricks are exactly? Want to know the different types that exist? Interested in their properties, or where they’re applied?
You’ve come to the right place!
We’ll explore these topics, unravel the purpose of fire bricks, and even understand their temperature tolerance. We’ll also take a closer look at the manufacturing process of these high-temperature bricks.
Let’s fire up the kiln.
Table of Contents
Bricks for High Temperatures: Understanding Refractory Bricks
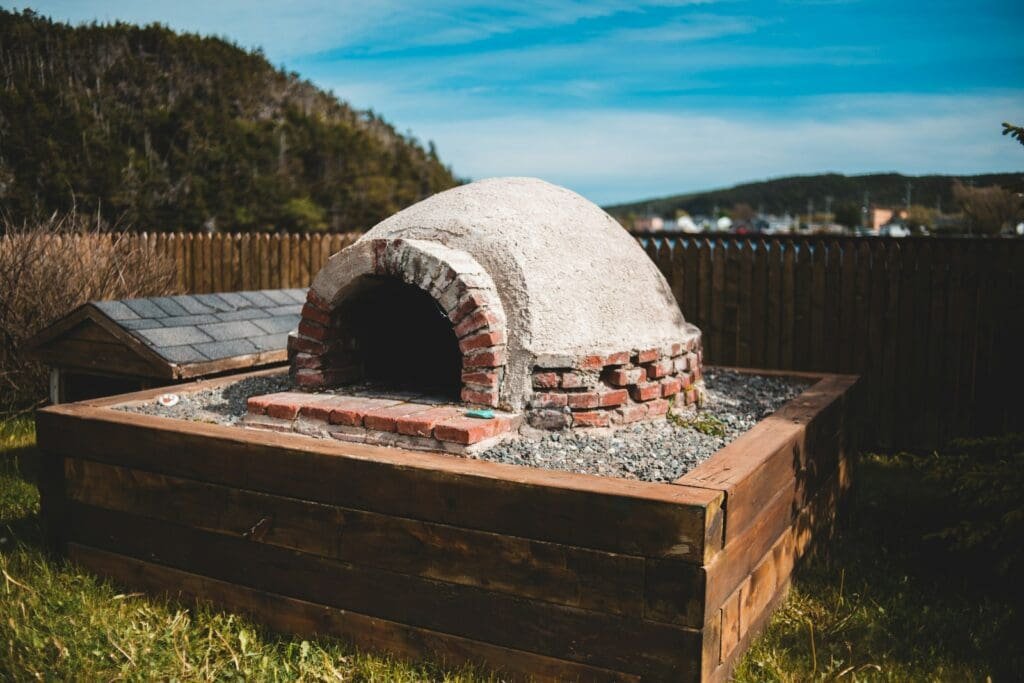
What Are Refractory Bricks?
Refractory bricks, also known as fire bricks, are specially designed to withstand high temperatures and harsh environments. These bricks are typically used in structures like furnaces, kilns, and fireplaces where standard bricks would fail due to the extreme heat.
Types of Refractory Bricks
- Alumina Bricks: Made with high alumina content, typically used in steel plants and foundries.
- Silica Bricks: Contain high silica content and are commonly used in glass and ceramic industries.
- Magnesia Bricks: Composed mainly of magnesium oxide, ideal for environments with basic slags.
Properties of Refractory Bricks
Property | Description |
---|---|
High Melting Point | Can withstand temperatures over 3000°F (1649°C) |
Chemical Resistance | Resistant to chemical reactions from hot gases and slags |
Thermal Conductivity | Low during hot conditions, which helps in insulation |
Mechanical Strength | Can endure physical stress without degradation |
Applications of Refractory Bricks
- Industrial Furnaces: Essential in metal extraction and processing.
- Pizza Ovens: Used to maintain high, consistent temperatures.
- Fireplaces and Wood Stoves: Necessary for proper insulation and safety.
Choosing the Right Refractory Brick
Consider the following factors when selecting refractory bricks:
– Temperature Requirements: Different environments require different types of refractory bricks.
– Chemical Stability: Match the brick’s chemical properties with the application’s environment.
– Mechanical Stress: Ensure the bricks can handle the physical load.
Remember, the right choice will ensure the longevity and efficiency of high-temperature installations.
Purpose of a Fire Brick: Essential Insights
Primary Functions of Fire Bricks
Fire bricks, also known as refractory bricks, serve several vital purposes in high-temperature environments:
- Heat Resistance: Engineered to withstand extreme temperatures without melting or breaking down.
- Structural Support: Provide the necessary infrastructure to maintain the integrity of furnaces, kilns, and other high-heat equipment.
- Insulation: Help retain heat within the system, ensuring energy efficiency and consistent temperatures.
- Safety: Prevent the heat from escaping and protect surrounding structures from potential heat damage.
Advanced Features of Fire Bricks
Fire bricks are not just about withstanding heat; they come with advanced properties tailored to specific industrial needs:
- Thermal Shock Resistance: Ability to endure rapid temperature changes without cracking.
- Dimensional Stability: Maintain shape and size despite exposure to high temperatures.
- Density: Varies depending on application needs, with high-density bricks offering greater strength and low-density bricks providing better insulation.
- Porosity: Controlled porosity to manage the absorption and release of heat.
Specialized Applications of Fire Bricks
Fire bricks are indispensable in various specialized applications beyond just furnaces and kilns:
- Glass Production: Used in glass melting tanks to withstand high temperatures and corrosive glass interaction.
- Chemical Plants: Serve in reactors and gasifiers under highly corrosive and high-temperature conditions.
- Cement Rotary Kilns: Essential in the lining of rotary kilns for producing cement, ensuring durability and efficiency.
- Incinerators: Provide safe and efficient incineration of waste materials at high temperatures.
Material Composition and Their Influence
The specific material composition of fire bricks significantly influences their performance in different applications:
Material | Expected Benefits |
---|---|
High Alumina | Improved heat tolerance, greater structural integrity, and superior resistance to acidic slag. |
Silica | Highly resistant to acidic environments and suitable for glass-making applications. |
Magnesia | Best suited for environments with basic slags, such as steelmaking. |
Chromite | Increased resistance to chemical attack and thermal shock. |
Temperature Tolerance of Fire Bricks
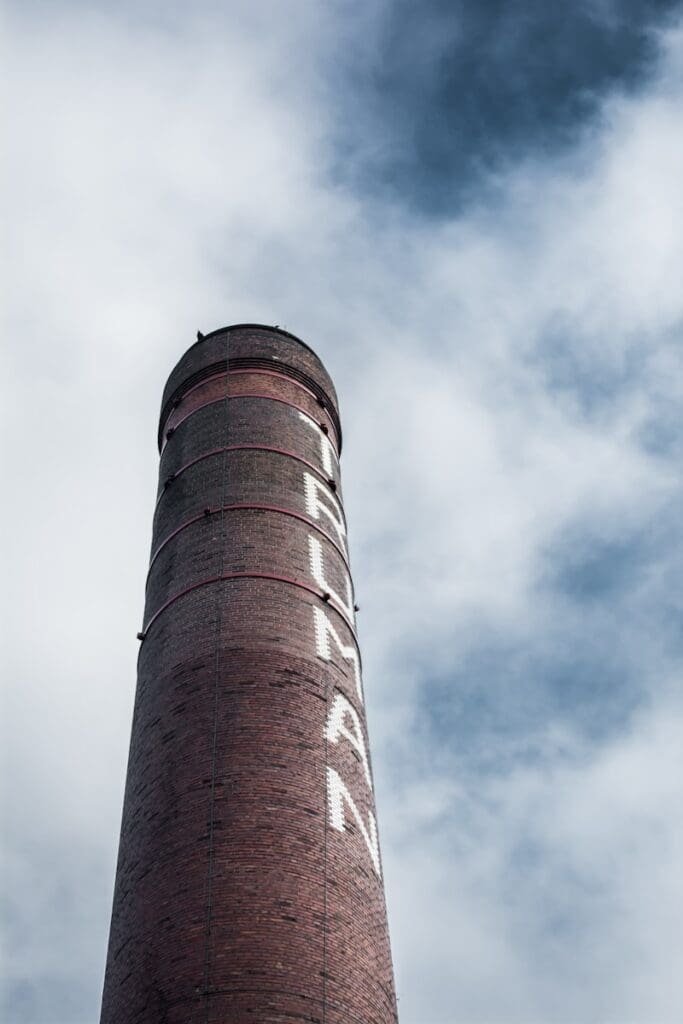
Defining Temperature Limits for Fire Bricks
Fire bricks, also known as refractory bricks, can tolerate an impressive range of temperatures, making them essential in high-heat environments. Their exact temperature tolerance depends on their material composition and type, allowing them to serve in various specialized industrial applications.
Temperature Tolerance by Type
The type of fire brick significantly determines how much heat it can withstand. Here’s a detailed look at the temperature limits for different types of fire bricks:
Type | Temperature Range |
---|---|
Alumina Bricks | Up to 3,600°F (1,982°C) |
Silica Bricks | Up to 3,100°F (1,704°C) |
Magnesia Bricks | Up to 3,300°F (1,815°C) |
Chromite Bricks | Around 3,200°F (1,760°C) |
Impact of Material Composition on Temperature Tolerance
The temperature tolerance of fire bricks is largely influenced by their material components:
- Alumina Content: Higher alumina levels improve thermal resistance, making these bricks ideal for steel manufacturing and other metal industries.
- Silica Content: High silica content contributes to strong thermal stability, perfect for glass-making and ceramics industries.
- Magnesium Oxide: The presence of magnesium oxide allows bricks to resist high temperatures and basic slags, useful in the steel and cement industries.
- Chromite Inclusions: Bricks with chromite offer additional thermal shock resistance and are often used in high-temperature kilns and furnaces.
Practical Applications by Temperature Limits
Knowing the temperature tolerance of fire bricks helps in selecting the right type for the specific application:
- Steel Manufacturing: Alumina and magnesia bricks are commonly used due to their high thermal resistance.
- Glass Production: Silica bricks are preferred for their ability to withstand high temperatures without degrading.
- Cement Kilns: Magnesia bricks are ideal for these applications where basic slags are prevalent.
- Rotary Kilns: Chromite bricks offer the necessary thermal shock resistance for these high-temperature installations.
Consider the specific temperature requirements for your application to ensure you choose the right type of fire brick. For more details, see this in-depth guide from Thermopedia.
Manufacturing High Temperature Fire Bricks: Essential Steps and Considerations
Raw Material Selection
One of the first steps in making high-temperature fire bricks is selecting the appropriate raw materials. The quality and composition of these materials significantly impact the performance and durability of the fire bricks.
- Alumina: A primary ingredient, high-purity alumina ensures bricks withstand high temperatures and provide structural integrity.
- Silica: Often used in combination with alumina, silica enhances the thermal stability of the bricks.
- Magnesium Oxide: Adds chemical resistance and is essential for bricks used in environments with basic slags.
- Binding Agents: Such as clay or synthetic binders, are selected to ensure the materials stick together during the forming process.
Forming the Bricks
The next step is forming the bricks, which involves several processes to ensure the materials are uniformly mixed and shaped correctly.
- Mixing: Raw materials are finely ground and mixed to ensure even distribution of components.
- Shaping: The mixed materials are shaped using molds or by extrusion, often under high pressure to remove air pockets.
- Drying: Shaped bricks are then dried at low temperatures to remove excess moisture, which would otherwise cause cracking during firing.
Firing Process
Firing is a crucial step that solidifies the bricks and imparts their final properties.
- Initial Heating: Bricks are gradually heated to remove remaining moisture without causing thermal shock.
- High-Temperature Firing: Bricks are fired in kilns at temperatures ranging from 2,200°F to 3,000°F (1,204°C to 1,649°C) depending on their composition. This process enhances their mechanical strength and temperature resistance.
- Controlled Cooling: After reaching peak temperatures, the bricks are slowly cooled to prevent cracking and ensure dimensional stability.
Quality Control and Testing
To ensure the bricks meet required standards, they undergo rigorous quality control and testing.
- Thermal Shock Resistance: Tests to certify that bricks can withstand rapid temperature changes without cracking.
- Compression Strength: Ensures bricks can endure the mechanical loads expected in their applications.
- Chemical Resistance: Verifies that the bricks can resist degradation in harsh chemical environments.
- Dimensional Accuracy: Ensures bricks meet precise size requirements for uniformity in construction.
Wrapping Up the Understanding of Refractory Bricks
Refractory bricks are specifically engineered to withstand high temperatures, offering structural support and insulation in various industrial environments from steel plants and foundries to glass and ceramics industries.
These specialized fire bricks come in different types, such as alumina, silica, and magnesia bricks, each with its unique properties and uses. Their characteristic traits include high melting point, chemical resistance, thermal conductivity, and mechanical strength, all contributing to their vital role in high-temperature applications – from industrial furnaces to pizza ovens. Choosing the right refractory brick is essential, based on considerations like temperature requirements, chemical stability, and mechanical stress for maximum efficiency.
Fire bricks’ capacity to tolerate extreme temperatures makes them indispensable across industries. The kind of fire brick and its material composition largely influence the temperature limit it can handle.
Understanding their respective temperature tolerances helps to determine the most appropriate type for a particular application – alumina and magnesia for steel manufacturing, silica for glass production, and chromite for high-temperature kilns and furnaces. Furthermore, manufacturing high-quality fire bricks revolves around steps like correct raw material selection, forming process, high-temperature firing, and meticulous quality control and testing.
Frequently Asked Questions – FAQs
What is a refractory brick?
A refractory brick or fire brick is a type of brick specifically designed to withstand high temperatures and harsh environments. Its uses are common in structures like furnaces, kilns, and fireplaces where standard bricks would fail under extreme heat.
What factors should you consider when selecting refractory bricks?
Key considerations should include the brick’s temperature requirements, chemical properties, physical load capacity, applications, and mechanical strengths. The right choice ensures the longevity and efficiency of high-temperature installations.
How does the material composition of a fire brick influence its performance?
The specific material composition significantly influences a fire brick’s performance. High alumina levels improve thermal resistance, making the brick ideal for steel manufacturing. High silica content contributes to strong thermal stability, making the brick perfect for glass-making and ceramics industries, among other influences.
What’s the process of manufacturing high-temperature fire bricks?
The process involves selecting appropriate raw materials, forming the bricks, firing them in kilns at high temperatures, and dependable quality control and testing procedures to ensure top-quality, durable bricks.