Understanding Antiquing Concrete
Antiquing concrete is a popular technique in creating unique aesthetic finishes on otherwise bland surfaces.
In essence, ‘antiquing’ refers to the process of adding a layer of color to simulate the graceful ageing effect that time has on materials.
In construction, this method empowers builders and homeowners to design textured, vintage-style concrete surfaces for patios, walkways, and driveways, providing depth, character, and visual interest.
Table of Contents
Antiquing Concrete: Costs And Strategies To Reduce Expenses
Navigating the world of concrete finishes can be a bit perplexing. But don’t oxidize your knuckles just yet. This guide will explain what is meant by ‘antiquing concrete’, how much it might set you back, and ways to minimize those costs without sacrificing on the quality or appearance of your project.
Understanding Antiquing Concrete
First, let’s take a brief detour to ensure we’re all on the same slab. Antiquing concrete, or acid staining, is a process that imparts an aged, textured appearance to a concrete surface, mimicking the natural patina time wears into traditional materials.
How Does it Work?
In this process, a thin, water-based solution is applied to fresh or cured concrete. The acid and metallic salts in the solution react with the concrete’s natural lime content, leaving behind unique, mottled color patterns.
Cost of Antiquing Concrete
Much like building a skyscraper, the cost of antiquing concrete is dependent on a variety of factors such as material costs, labor fees, and the area to be covered.
The Breakdown
Here’s a rudimentary breakdown:
Factors | Estimated Cost |
---|---|
Material Costs | $0.50 – $2.50 per sq. ft. |
Labor Fees | $10 – $20 per sq. ft. |
Total | $10.50 – $22.50 per sq. ft. |
Please note that these are only rough estimates. The actual cost can vary depending on the complexity of the job, local pricing, and the specific products used.
Minimizing the Costs of Antiquing Concrete
If the cost of antiquing concrete has got you feeling like your pockets are full of cement, fear not. Here are a few practical ways to lower the costs:
- Do-It-Yourself: If you feel confident in your abilities, you can buy the materials and do the job yourself. How-to guides and videos can be found online. Make sure to be safe!
- Get quotes: Don’t settle with the first contractor you find. Get multiple quotes and compare them to judge what’s fair and what’s too high.
- Go local: Sometimes, local suppliers and contractors will be cheaper due to low transportation and project costs.
- Consider the size: Remember, smaller projects will naturally cost less than larger jobs. Consider doing this in stages if it’s a large project.
By staying informed, and carefully considering your budget and the scope of the project, you can add a touch of rustic charm to your concrete surfaces without breaking the bank.
Additional Factors Influencing Cost of Antiquing Concrete
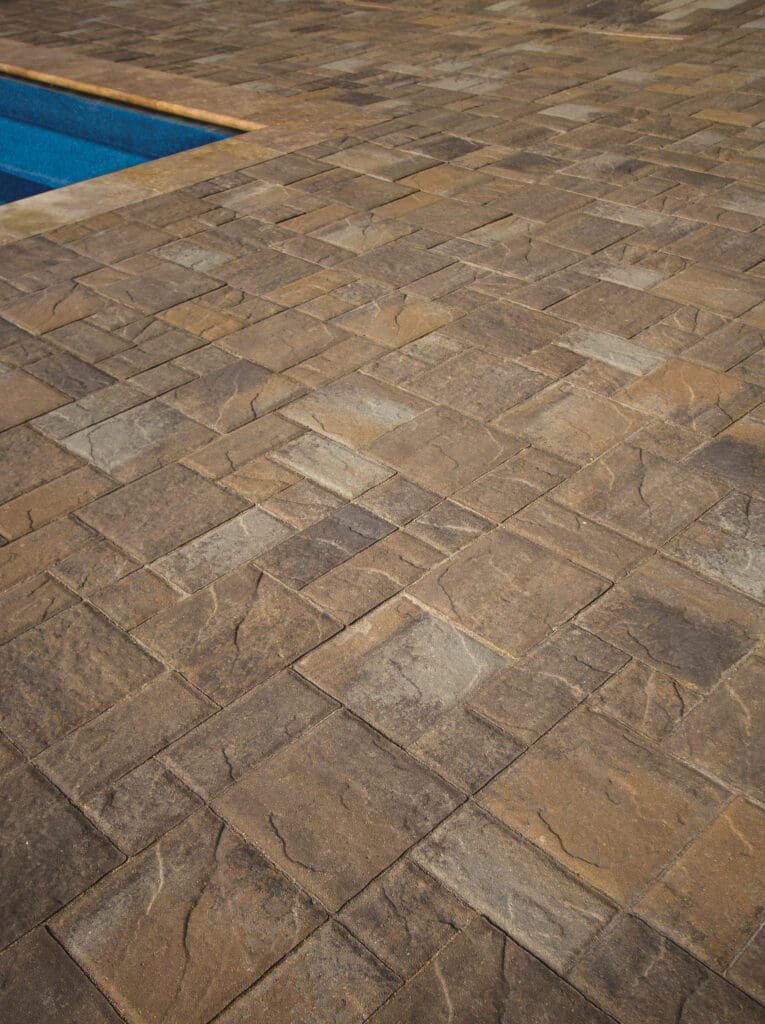
While the cost breakdown provided offers a comprehensive picture of the core antiquing costs, there are additional factors that you should consider when planning your antiquing concrete project.
Concrete Quality
The quality of your concrete can be a significant determinant of the cost of antiquing. This is in large part due to the fact that higher quality concrete absorbs the staining solution better, creating an aesthetically pleasing finish.
Advantages of High-Quality Concrete
- Ease of Stain Applications: High-quality concrete allows for smoother, more even application of the staining solution.
- Better Visual Effects: Greater the quality of the concrete, more intricate and stunning are the effects that can be achieved.
- Increased Durability: High-quality concrete resists cracking and erosion better, extending the life and look of your antiqued surface.
Complexity of the Design
The desired effect or design you want can also impact the cost. A more complex design requires more time and potentially unique materials, thus increasing the overall cost.
Opting for Simplicity
Instead of elaborate designs and patterns, consider a simple, organic-looking finish. This can save you money while still providing an elegant and unique appearance to your concrete surface.
Ongoing Maintenance Costs
While not immediately visible, the cost of maintaining your antiqued concrete should also be factored into your project budget. This maintenance can range from general cleaning to re-application of sealant to prolong the life of the stain.
Maintenance Tips
- Regular Cleaning: Use a gentle cleaner and avoid harsh chemicals to keep your stained concrete surface looking fresh.
- Sealant Application: Depending on wear and tear and exposure to weather, reapply a concrete sealant every few years to maintain the finish and prolong the stain.
- Professional Inspection: Schedule an annual inspection with a concrete professional to catch any potential issues early.
By understanding these extra factors, you can plan, and budget for your antiquing concrete project more effectively, while being able to control the costs and maintain the aesthetics and durability of your project in the long run.
The Role of Surrounding Environment in Antiquing Concrete Costs
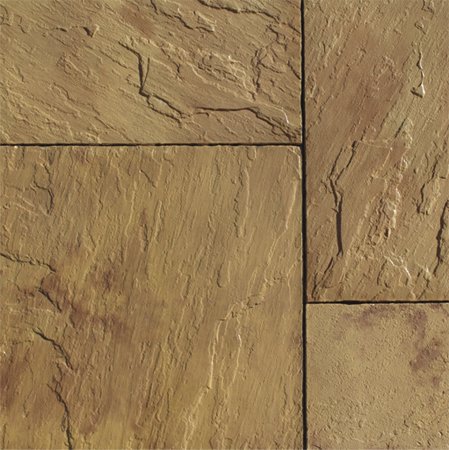
After understanding the primary and additional factors that influence the cost of antiquing concrete, it’s also essential to consider the impact of your project’s surrounding environment.
Environmental Factors
Whether it be your home, commercial space or public area, the environmental elements surrounding your concrete project can have a significant influence on the long-term durability and upkeep costs.
Weather Conditions
How your antiqued concrete stands up to local weather conditions plays a role in your project’s longevity and maintenance costs. Extreme heat, cold, or humidity can affect the staining process and the durability of your concrete surface.
- Heat: High temperatures may cause the stain to dry too quickly, leading to uneven coloring.
- Cold: Cold temperatures can slow down the stain reaction, which might impact the desired effect.
- Humidity: In high-humidity areas, moisture can affect the stain’s adherence to the concrete surface, potentially causing a less vibrant color result.
Exposure to Elements
Exposure to sun, rain, snow, and heavy footfall or vehicular traffic can affect the long-term durability of your antiqued concrete, potentially increasing maintenance costs.
Strategies to Mitigate Environmental Impacts
Although you cannot change your environment, understanding these factors can help you prepare and plan strategic measures to ensure the longevity and vibrancy of your stained concrete.
- Choose the Right Sealant: Your local concrete professional can guide you towards sealants that are best suited for your area’s weather conditions and typical outdoor environmental factors. A good sealant will help protect your concrete from moisture, UV rays, and other potential damage.
- Professional Application: A professional applicator can adjust their techniques to suit the local environment, ensuring your antiqued concrete has a uniform finish, regardless of heat, humidity, or cold.
- Regular Maintenance: Following a strict maintenance schedule – necessary in harsh weather conditions – will help prolong your stained concrete’s lifespan.
Environmental factors are an often overlooked yet important part of planning your antiquing concrete project. By being aware of these issues, you can accurately budget your project, ensuring you achieve a visually stunning, long-lasting result.
Sources
For a comprehensive discussion on environmental factors on concrete staining, visit Concrete Network’s guide on Weather and Concrete Stains.
Conclusion on Concrete Antiquing
In wrapping up, we’ve discovered that ‘antiquing concrete’ is a process that can give an appealing rustic look to your concrete surfaces. However, the cost can be a concern, with prices largely depending on material costs, labor fees, and the size of the area to be worked upon.
From our perspective, reducing the expense associated with antiquing concrete is feasible. DIY approaches, comparative shopping amongst contractors, sourcing locally, or breaking a large job up into smaller tasks could help keep those costs down. We believe that by remaining informed and taking the time to consider different strategies, you can achieve your desired concrete finish, even with budget constraints.
Remember, the charm and durability added by antiquing concrete can increase the value of your property, making it a sound investment in the long run.