Understanding Shotcrete Rebound
Shotcrete rebound is a term in the construction industry which deals with the quantity of shotcrete mix that bounces off the receiving surface when sprayed.
A fundamental part of the shotcrete process, it plays a pivotal role in both the safety and efficiency of the project.
Minimizing shotcrete rebound ensures the efficient use of resources while maintaining project timelines. However, managing this rebound can be a tough challenge, requiring specific methods and equipment.
From a practical standpoint, understanding shotcrete rebound can help avoid excess waste, minimize costs, and improve overall project efficiency.
Let’s mix up some concrete and dive into the complexities and applications of shotcrete rebound.
Table of Contents
Prefer to watch instead of read? Click the video below.
Understanding the Rebound Rate of Shotcrete in Construction
In the world of construction, the rebound rate of shotcrete can be a vital consideration in project planning and execution.
But what exactly does this term mean?
Let’s dive deeper into the concept and how it affects the construction process.
Defining Rebound Rate
In simple terms, the rebound rate of shotcrete refers to the amount or percentage of shotcrete that bounces back off the surface during application, failing to stick to its intended site.
This happens as a result of the high velocity at which shotcrete is sprayed. The rate of rebound shotcrete is crucial as it impacts cost, time, and material waste on construction sites.
Determining Factors
Several factors can influence the rebound rate of shotcrete, including:
- Type of surface the shotcrete is being applied to
- Angle at which the shotcrete is applied
- Type of shotcrete (wet mix or dry mix)
- How experienced the sprayer is
Calculating The Rebound Rate
Rebound rate is calculated as a percentage. The formula commonly used is:
Rebound Rate (%) = (Waste Material / Total Material) x 100%
The Impact on Construction Projects
Material Waste and Cost Implications
The higher the rebound rate of shotcrete, the more waste material is generated, which not only adds to the project’s environmental footprint but also raises costs due to wasted materials and the need for proper waste disposal.
Timeline Implications
Another key concern revolving around a high rebound rate involves project timelines. More rebound means more cleaning and preparation time, which can slow down the overall progress of the construction project.
Safety Concerns
Excessive rebound can also lead to safety issues. The small pieces of concrete that bounce back during application can potentially cause injury if necessary safety measures are not in place.
From material waste and cost overruns to safety concerns and timeline delays, the rebound rate of shotcrete clearly has a significant role in the overall success of construction projects. Therefore, understanding it and finding ways to reduce it can lead to better project outcomes.
Key Takeaways On Shotcrete Rebound Rate
A detailed understanding of terms like the rebound rate of shotcrete is essential for anyone involved in construction. It is a good measure of efficiency and effectiveness, and can greatly influence the outcome of a project in terms of cost, safety, and timeline. Therefore, it’s vital to control and minimize the rebound rate where possible.
For further reading on the topic, consider this comprehensive guide to shotcrete in construction.
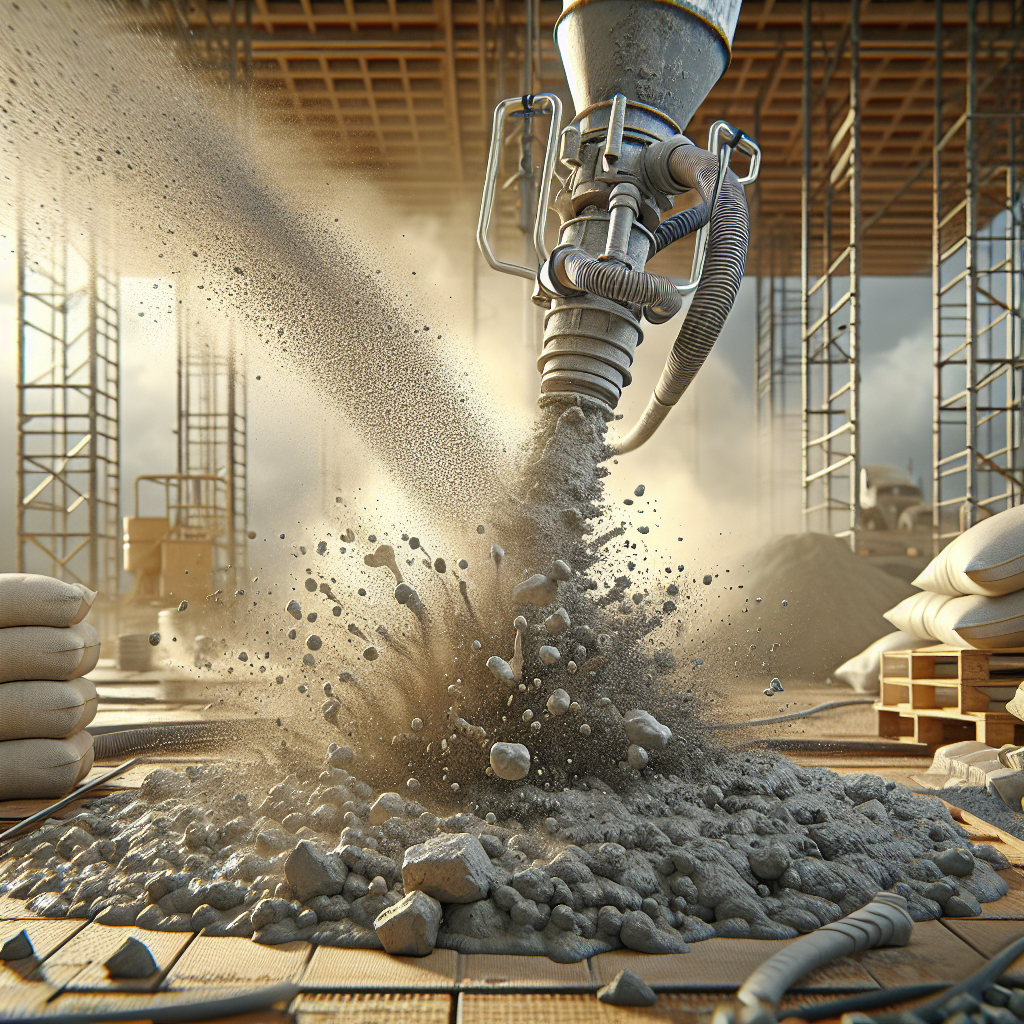
Reducing the Rebound Rate of Shotcrete
Effectively reducing the rebound rate in shotcrete involves a number of approaches and techniques. While the inherent properties of the material contribute to the rebound, the application method and conditions also play a crucial role.
Correct Application Technique
Ensuring an appropriate technique when applying the shotcrete can have a significant impact on the rebound rate. Crucially, the nozzle operator should aim to:
- Apply the shotcrete at a right angle to the surface
- Sustain a consistent distance from the nozzle to the application surface
- Maintain constant velocity and pressure during application
These steps can help to achieve a more consistent application, minimizing the amount of material that might otherwise rebound or fall away from the surface.
Choice of Shotcrete Mix
Selection of the right shotcrete mix can also influence the rebound rate. Wet mix shotcrete usually has a lower rebound rate compared to the dry mix, as the pre-mixed water helps the shotcrete to adhere better on application.
Size of Aggregate
The size of the aggregate used in the shotcrete mix plays a significant role in rebound rate. Smaller aggregates tend to reduce the rebound rate; however, it’s important to strike a balance since using extremely small aggregates can impact the strength and integrity of the shotcrete.
Using Additives
There are several additives available that can reduce the rebound rate of shotcrete. These materials interact with the cementitious components enhancing the adherence properties of the shotcrete, and reducing the rebound. It’s crucial to choose additives that are compatible with the particular mix design and that comply with safety standards.
Surface Preparation
Proper preparation of the surface where shotcrete is being applied can make a significant difference. Removing loose soil or debris and ensuring the surface is damp can help improve the adherence of shotcrete, hence reducing the rebound rate.
Skilled Personnel
Investing in skilled and experienced nozzle operators can contribute to lower rebound rates. A knowledgeable operator will be able to control the application pressure and spray angle effectively, resulting in greater efficiency and less wasted material.
To Put It In Plain Terms
Reducing the rebound rate in shotcrete application essentially comes down to the right combination of materials, surface preparation, skilled application, and the use of appropriate additives.
Lower rebound rates result in increased project efficiency, cost savings, less waste, and safer construction sites, underscoring the importance of minimizing the rebound rate in any shotcrete-based project.
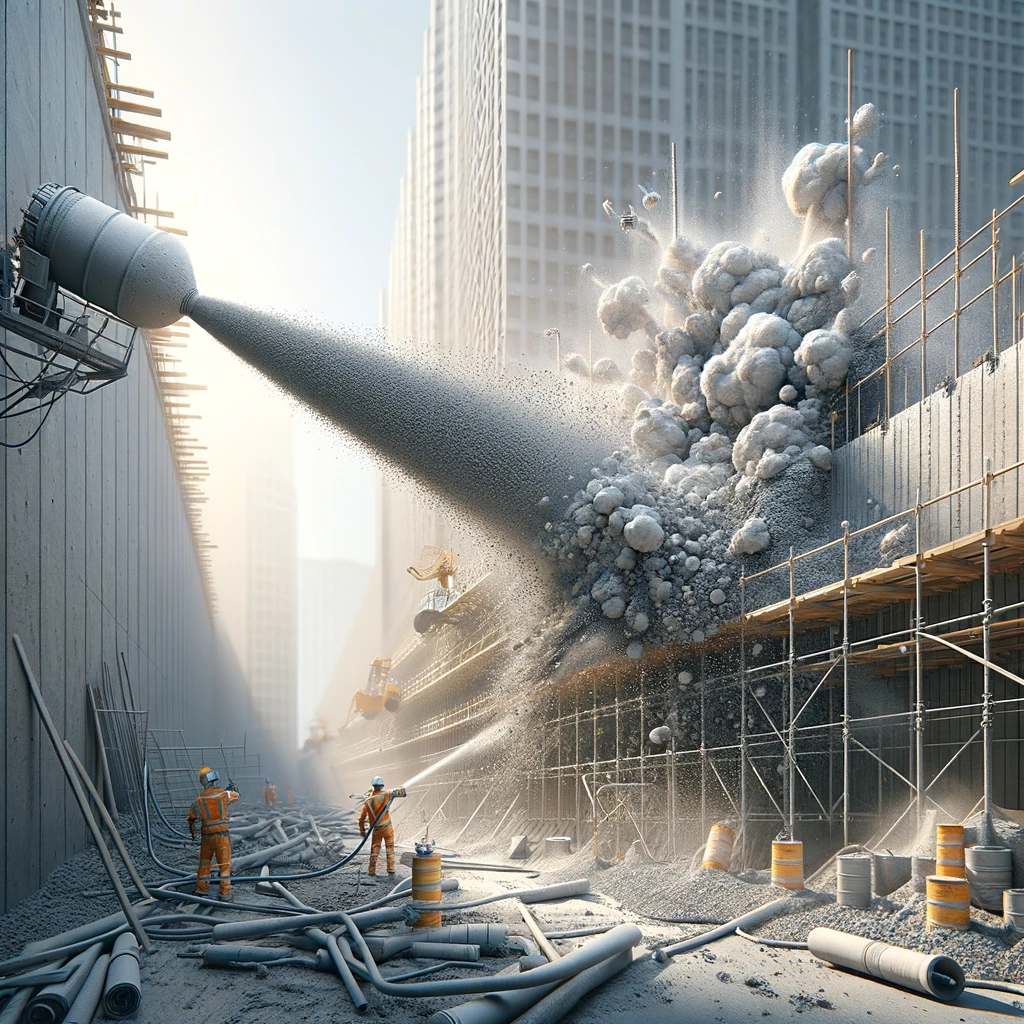
Predicting The Percentage of Shotcrete Waste
While it’s crucial to understand the concept of the rebound rate in shotcrete application, accurately predicting the percentage of shotcrete waste is equally important. This contributes to better project management, cost-efficiency and sustainability in the construction process.
Factors Affecting Shotcrete Waste
Shotcrete waste is heavily influenced by several factors that coincide with those affecting the rebound rate, with additional considerations:
- Quality of shotcrete mix
- Aggregate and water ratio in the mix
- Weather conditions during application
Estimating Shotcrete Waste
Estimating the volume of shotcrete waste is often done based on historical data and experience. Contractors often account for a certain percentage of waste (e.g., 10%-20%) in their quantity calculations. However, this “guesstimate” is highly influenced by the factors listed above.
Measuring Shotcrete Waste
The most accurate method for calculating shotcrete waste is to weigh the rebounded material and subtract it from the total shotcrete applied. This should be done under carefully controlled conditions to ensure accuracy.
Reducing Shotcrete Waste
Strategies to minimize shotcrete waste are mostly similar to those for reducing the rebound rate, including proper application techniques and skilled operators. Other measures include:
- Meticulous planning and accurate estimation of material volume
- Thorough testing of the shotcrete mix for workability and adherence
- Use of additives to enhance the adhesion properties of shotcrete
Predicting the percentage of shotcrete waste is a critical aspect of project planning and execution. A thorough understanding of associated factors coupled with strategic measures can significantly reduce shotcrete waste, improving cost-effectiveness and boosting sustainability.
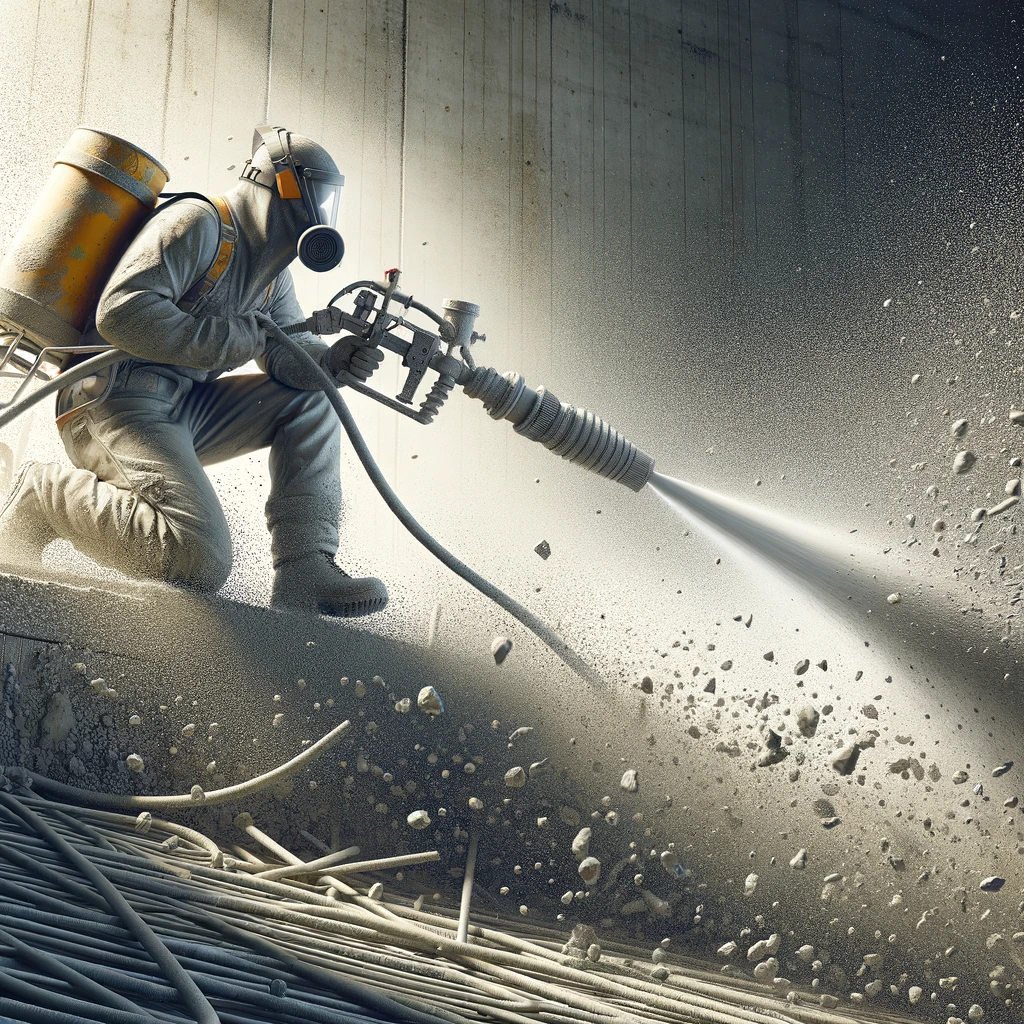
Exploring the Versatility of Concrete: Beyond Shotcrete
Had enough of shotcrete rebound?
We’ve got good news:
While shotcrete, a method of applying concrete pneumatically through a hose, is a popular technique, it’s just the tip of the iceberg when it comes to concrete application methods.
Some alternative methods that showcase the versatility and adaptability of concrete (while also helping you avoid any shotcrete rebound) can be used in various construction scenarios.
1. Cast-in-Place Concrete
Cast-in-place concrete is the traditional and most common method of concrete construction.
This technique involves pouring concrete into removable forms or molds on-site where the structure is being built. It allows for a wide range of shapes and sizes, making it ideal for constructing foundations, walls, floors, and even intricate architectural features.
The adaptability and fluidity of this method make it a go-to choice for many construction projects, from residential homes to towering skyscrapers.
2. Precast Concrete
Precast concrete takes a different approach by manufacturing concrete elements in a factory setting before transporting them to the construction site for assembly.
This method offers several advantages, such as enhanced quality control, reduced construction time, and less waste.
Precast concrete is used in a variety of applications, including bridges, parking garages, and modular buildings, showcasing its flexibility and efficiency.
3. Stamped Concrete
Stamped concrete introduces an aesthetic dimension to concrete application, offering a decorative touch that mimics the appearance of brick, slate, stone, or even wood.
This technique involves pouring slab concrete and then impressing patterns and textures onto the surface while it’s still soft.
Stamped concrete is a popular choice for patios, sidewalks, driveways, and pool decks, blending functionality with aesthetic appeal.
4. Concrete Masonry Units (CMUs)
Concrete masonry units, or CMUs, are precast concrete blocks that are stacked and bound together with mortar to form walls and other structures.
This method is valued for its structural integrity, fire resistance, and thermal insulation properties.
CMUs are commonly used in both residential and commercial construction, particularly for load-bearing walls.
5. Roller-Compacted Concrete (RCC)
Roller-compacted concrete is a dry mix that is mechanically compacted using rollers, similar to the way asphalt is compacted.
This method is typically used for constructing roads, dams, and large pavements that require a durable and low-maintenance surface.
RCC combines the strength and durability of concrete with the ease of construction of asphalt, offering a practical solution for large-scale infrastructure projects.
6. Fiber-Reinforced Concrete
Fiber-reinforced concrete incorporates fibrous materials to enhance its structural integrity and reduce the risk of cracking.
These fibers, which can be made from steel, glass, synthetic materials, or natural fibers, are mixed into the concrete, providing reinforcement that distributes stress and improves impact resistance.
This method is particularly useful for industrial floors, overlays, and other applications where durability is a critical concern.
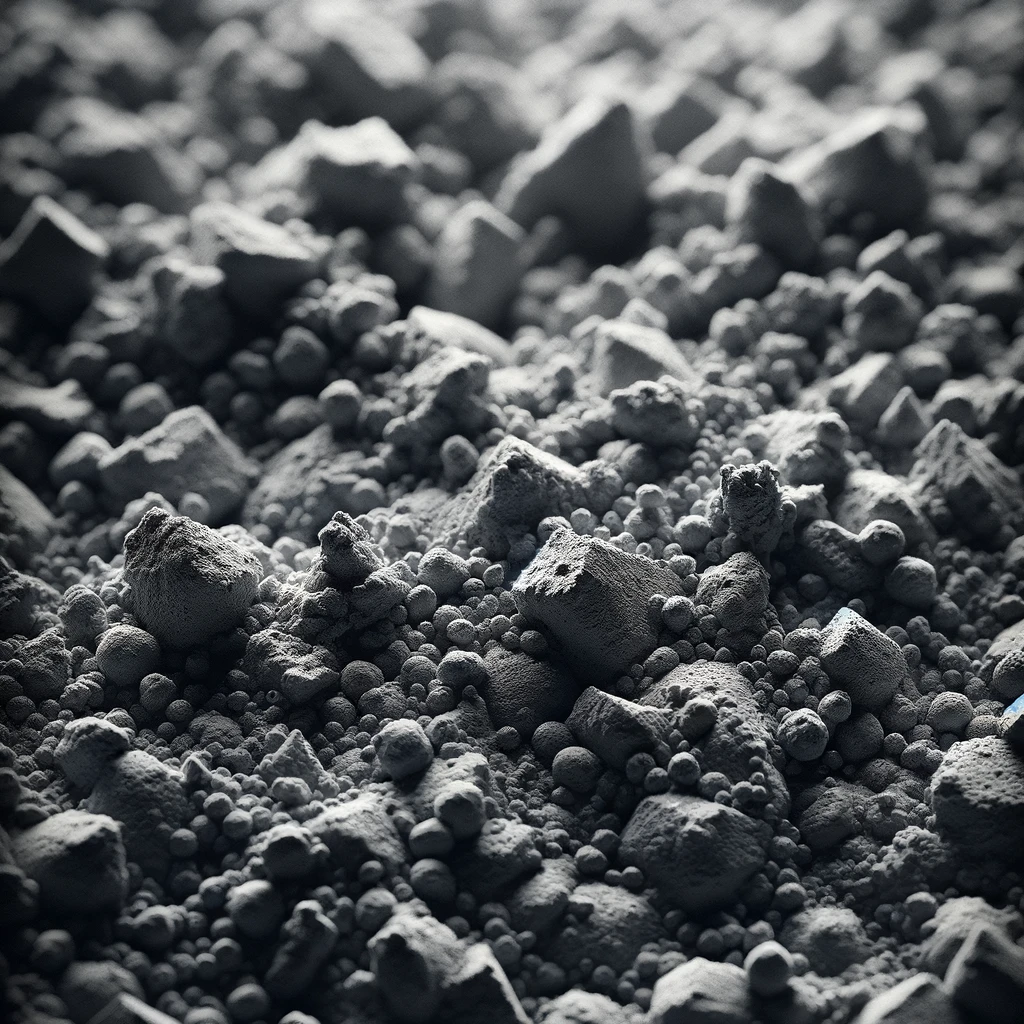
Summing It All Up
In the end, the rebound rate of shotcrete is not a metric to overlook in construction projects. Understanding this phenomenon is crucial as it directly impacts the efficiency, cost-effectiveness, and safety of operations. From our perspective, a high rebound rate corresponds not only to material and financial waste, but also to potential safety hazards and project delays.
We’ve found that controlling factors, like the type of surface, the angle of application, shotcrete type, and the operator’s experience level, can significantly lower the rebound rate and enhance the overall project execution. Based on this, it’s evident that minimizing the rebound rate should be a primary consideration for professionals involved in construction work using shotcrete.
It is our hope that thorough understanding and thoughtful management of rebound rates will pave the way for safer, more efficient, and cost-effective construction projects.