Introduction: Thriving in the Construction Business Amid Cost Escalations
Did you know construction costs have been on a steady rise over the past few years?
If you’re a contractor, developer, or builder, chances are, you’re grappling with this reality. Yet, you still have to deliver quality work while staying profitable.
The question is, how can you control and minimize these escalating costs?
In this blog post, we’ll explore practical and actionable strategies to help you optimize your operation and reduce expenditure in your construction business. We’ll discuss tools like efficient project management and digital technology that can streamline your processes. We’ll show how procurement practices, energy-efficient solutions, and training programs can make a difference to your bottom line.
Moreover, we’ll uncover the value of regular financial reviews, the use of local resources, and the implications of design changes on costs. All these points are designed to help you maximize returns and sustain steady growth in the construction industry.
Table of Contents
How to Reduce Costs in Construction Business
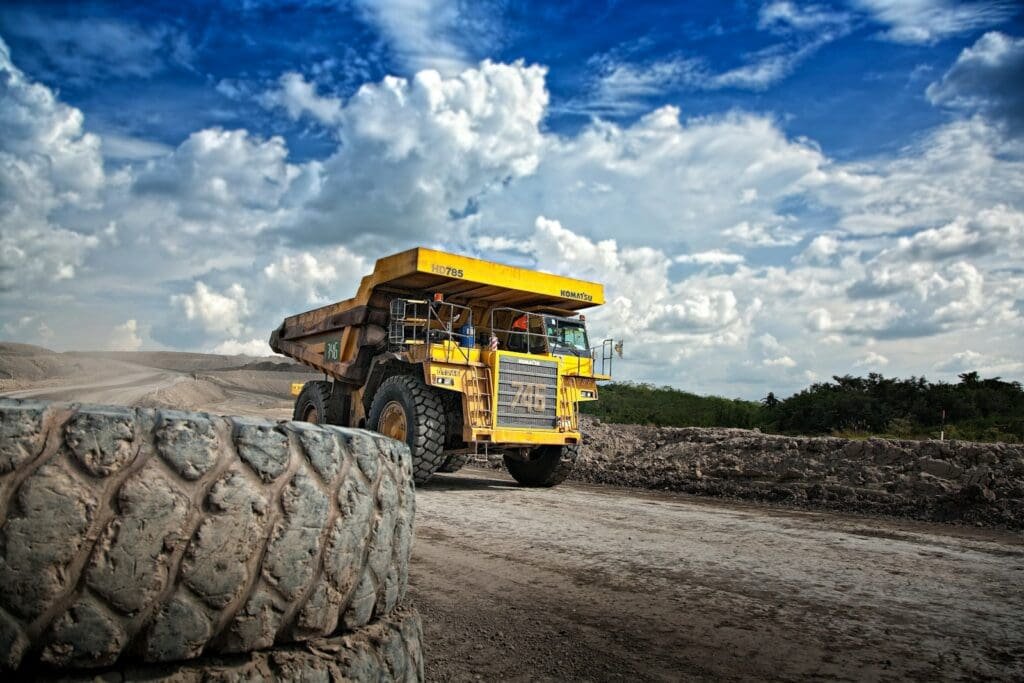
Implement Efficient Project Management
Maximizing efficiency in project management can significantly cut costs. Here are a few strategies:
- Use project management software to streamline operations.
- Regularly review project timelines to identify delays early.
- Ensure clear communication among team members.
Examples of project management tools include Asana, Trello, and Microsoft Project. These tools help track progress, assign tasks, and manage deadlines.
Pursue Bulk Purchasing Agreements
Buying materials in bulk can save a lot of money. Consider the following to make it more effective:
- Analyze project needs and estimate the materials required.
- Negotiate bulk purchasing discounts with suppliers.
- Store materials in a controlled environment to prevent waste.
Forming a good relationship with suppliers may result in better deals and discounts.
Invest in Training and Safety Programs
Investing in employee training ensures better work quality and avoids costly mistakes. Here’s what you can do:
- Conduct regular training sessions on new technologies and techniques.
- Implement safety programs to reduce workplace accidents.
- Encourage continual learning and development.
Proper training reduces the likelihood of errors and accidents, both of which can be costly.
Opt for Energy-Efficient Solutions
Energy-efficient solutions not only save money but also reduce environmental impact. Consider these:
- Use energy-efficient equipment on-site.
- Install solar panels to reduce electricity costs.
- Implement recycling programs to cut waste management costs.
For example, using LED lighting and energy-efficient machinery can save significant amounts in energy bills.
Adopt Technological Advancements
Staying updated with technological advancements can help in cutting costs. Some suggestions include:
- Utilize Building Information Modeling (BIM) to minimize errors in planning.
- Implement drones for site inspections to reduce manual labor cost.
- Use prefabrication techniques to reduce on-site construction time.
For instance, a report from Forbes highlights how technology like BIM can revolutionize the construction industry by reducing errors and improving efficiency.
Regular Financial Reviews
Regular reviews of financial statements help identify areas where costs can be cut. Key points to consider:
- Conduct monthly audits of expenses and revenues.
- Analyze project budgets and identify unnecessary expenditures.
- Adjust financial plans based on audit outcomes.
Tracking finances closely ensures you can pinpoint where money is being wasted or used ineffectively.
Utilize Local Resources and Labor
Using local resources and labor can reduce logistics and material costs. Tips for effective use include:
- Hire local subcontractors to minimize travel expenses.
- Source materials from nearby suppliers to reduce transportation costs.
- Encourage community involvement for support and goodwill.
Local sources often provide faster delivery times, reducing project delays and associated costs.
Strategies to Curb Construction Costs
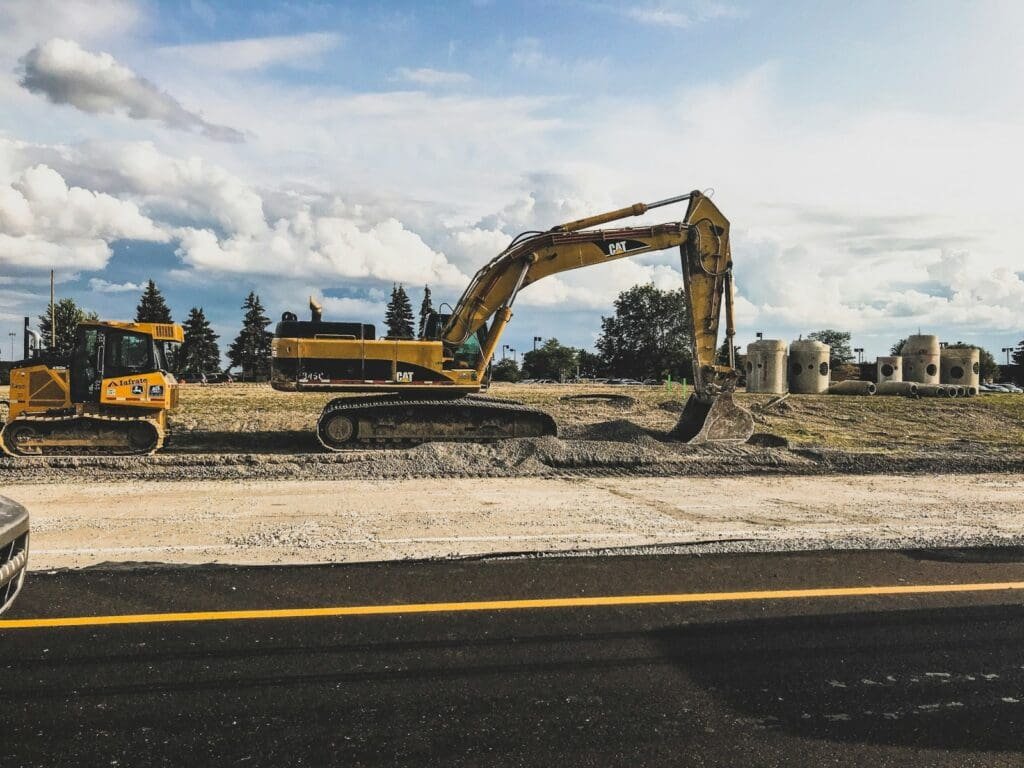
Revise Design Plans
In the early stages of planning, consider making thoughtful revisions to your design plans:
- Find cost-effective alternatives for expensive materials without sacrificing quality.
- Select a design that maximizes space usage efficiently.
- Avoid complexity in design which can result in higher labor cost.
Simpler and well-planned design can save significant costs on building materials and construction labor.
Collaborate with Experienced Teams
Working with experienced construction teams can promote cost-saving:
- Experienced workers can provide valuable insights on avoiding common pitfall.
- Hiring professionals can negate the need for rework, thus minimizing waste of resources.
- They come equipped with knowledge of more efficient techniques and processes.
These teams have a stronghold on construction aspects that can prevent resource wastage, rework and promote efficiency.
Choose Right Construction Method
Different types of construction methods can influence project cost:
- Consider modular or prefabricated construction to reduce worker hours on site.
- Choose a lean construction method for minimizing waste and improving productivity.
- Use green building practices for long-term energy and resource savings.
Choosing an efficient construction method according to the project can yield substantial cost reduction.
Use Quality Materials
Investing in quality materials initially can save costs in the long run:
- Quality materials are more durable and require less maintenance.
- They can increase the property value.
- Avoid future repair and replacement costs.
Though they may be more costly initially, quality materials can provide a better return on investment over time, thereby reducing the overall project costs.
Optimize Equipment Use
Optimizing the use of construction equipment can also save costs:
- Rent equipment rather than buying if it’s not regularly used.
- Keep equipment well-maintained to prevent costly repairs or replacements.
- Invest in multi-function equipment that can perform various tasks.
By strategically managing equipment usage, you can significantly reduce both immediate expenses and long-term operating costs.
Implement Waste Reduction Strategies
Minimizing waste generation can be a significant cost-saver:
- Re-use materials whenever possible.
- Recycle non-hazardous material waste.
- Sell or donate excess materials rather than discarding them.
Minimizing waste generation not only helps in cost reduction but also promotes sustainable construction practices.
With your financial strategies in place, the next step is execution. Implementing these cost-saving techniques can drastically reduce your overall expenditure and increase the profitability of your construction projects. The key lies in careful planning, consistently reviewing your progress, and making necessary adjustments as the project evolves.
Enhance Construction Efficiency to Lower Costs
Opt for Just-In-Time Inventory Management
Efficient management of materials can play an essential role in keeping costs low. Just-In-Time (JIT) inventory management can minimize inventory holding costs:
- Order materials to arrive as they are needed on-site, preventing overstock.
- Reduce storage costs by keeping inventory levels low.
- Enhance cash flow by avoiding large upfront purchases.
By adopting JIT, construction companies can decrease waste and increase efficiency, reducing overall project costs.
Utilize Cost-Efficient Labor Scheduling
Managing project labor effectively can help in reducing costs significantly:
- Schedule labor efficiently to match peak productivity times.
- Incorporate shift work to maximize machine and labor utilization.
- Use temporary labor strategically for specific project phases.
Efficient labor management can reduce idle time and increase productivity, helping to keep costs low.
Engage in Value Engineering Practices
Value engineering focuses on improving the value of building projects by analyzing functions and minimizing costs while maintaining quality:
- Conduct workshops with stakeholders to identify cost-saving opportunities.
- Analyze alternative materials and methods to find value-based solutions.
- Ensure design and construction meet essential performance requirements.
Through value engineering, significant savings can be achieved without compromising on project quality.
Leverage Sustainable Building Practices
Sustainability in construction can lead to long-term savings:
- Incorporate renewable energy sources, such as geothermal heating systems.
- Use sustainable building materials like reclaimed wood and recycled steel.
- Implement water-saving technologies to reduce utility costs.
Sustainable practices not only help in saving costs but also improve your brand’s reputation among eco-conscious clients.
Deploy Construction Management Software
Utilizing specialized construction management software can streamline operations and reduce administrative costs:
- Centralize project documentation and communication.
- Track expenses and manage budgets more effectively.
- Automate reporting and data entry to save labor hours.
These software tools enhance overall project efficiency and provide clear insights into financials, aiding in cost control.
Incorporate Preventative Maintenance Plans
Preventative maintenance of equipment can dodge unexpected costs:
- Schedule regular maintenance checks for machinery and equipment.
- Keep an inventory of essential spare parts to avoid downtime.
- Train operators on proper equipment usage to extend lifespan.
By maintaining equipment proactively, you can avoid costly breakdowns and extend the useful life of machinery.
For detailed methods on keeping construction costs low, consider these additional strategies to ensure project success and financial efficiency.
Conclusion: Vital Steps to Slash Construction Costs
In a nutshell, reducing construction costs boils down to savvy management and innovation. From employing efficient project management tools, leveraging bulk purchasing, and investing in workforce training and safety programs, to embracing energy-efficient solutions, technological advancements, and regular financial reviews – every strategy plays a pivotal role. Locally sourced materials and labor, well-thought-out design plans, collaboration with experienced teams, and picking the right construction methods also contribute to cost savings.
Strategic use of high-quality materials, optimization of equipment, waste reduction, JIT inventory management, cost-efficient labor scheduling, value engineering practices, sustainable building practices, and adopting construction management software, along with preventive maintenance plans, can further enhance cost efficiency. By implementing these measures, one can noticeably trim down construction costs, augment profitability and boost project success.
Frequently Asked Questions – FAQs
What is one of the most effective ways to cut costs in construction?
One of the most effective ways to cut costs is through efficient project management. This can be achieved by using project management software tools which help streamline operations, track progress, assign tasks, and manage deadlines.
How can technology help in reducing construction costs?
Technological advancements like Building Information Modelling (BIM) can help minimize errors in planning, reducing costly reworks. Also, implementation of drones for site inspection can help bring down manual labor cost.
How does investing in quality materials save construction costs in the long run?
Investing in quality materials may seem expensive initially, but they are more durable, require less maintenance, boost property value, and help avoid future repair and replacement costs, saving money in the long term.
What role does efficient labor scheduling play in cutting construction costs?
Efficient scheduling of labor, matching peak productivity times, and incorporating shift work can enhance machine and labor utilization. Strategic use of temporary labor can also lower costs.
Why are sustainable building practices beneficial?
Sustainability in construction leads to long-term savings. Incorporating renewable energy sources and using sustainable building materials can decrease reliance on traditional, often more expensive sources and methods, and also improve the company’s reputation among eco-conscious clients.