Introduction to the Art of 3-Coat Wall Plastering
A great place to start any day is by learning something new.
And in this article, I’m going to give you a behind-the-scenes look at a technique that has been used for centuries in building beautiful, durable structures.
It’s called the 3 coat method of masonry wall plastering.
So, ask yourself this: How often have you admired a smooth masonry wall and wondered about the process that went into its construction? Today, we are going to explore this traditional method and just how it produces such perfect results.
We’ll cover the three distinct layers of plaster application, namely the scratch, brown, and finish coats. Each is uniquely important in contributing to the integrity of the wall and its refined appearance. We will also touch on some of the key advantages of this method.
Further, we’re going to discuss its place in the broader world of construction practices, showing how its principles are applied in other methods such as stucco application, and what preparations are required for ensuring successful execution.
Finally, we’ll identify when it’s best to hand over the process to professionals for the sake of a flawless finish.
Ready to get started? Let’s plug into the world of masonry wall plastering.
Table of Contents
Understanding the 3 Coat Method of Masonry Wall Plastering
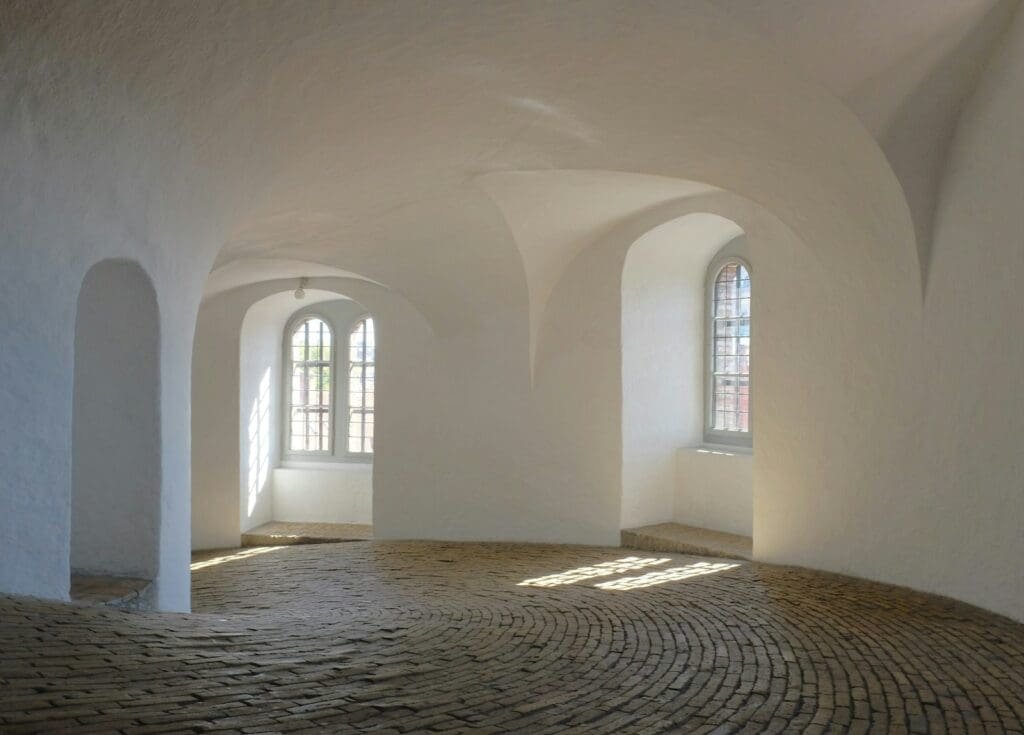
What is the 3 Coat Method?
The 3 coat method of masonry wall plastering is a traditional technique used in construction to create a smooth, durable wall surface. This process involves applying three distinct layers of plaster to enhance the wall’s finish and provide added strength.
The Three Layers Explained
1. The Scratch Coat
The first layer is known as the scratch coat. This base layer serves as the foundation for the subsequent coats and provides a rough surface for better adhesion.
- Composition: Usually made from a mixture of cement, lime, sand, and water.
- Application: Applied directly to the masonry surface in a thickness of about 3/8 inch.
- Texture: The surface is scored with horizontal or crisscross lines for better bonding with the next layer.
2. The Brown Coat
The second layer, called the brown coat, provides the main leveling layer for the wall and further strengthens the bond.
- Composition: Similar mix of cement, lime, sand, and water, but sometimes with a higher sand content.
- Application: Applied over the scratch coat in a thickness of about 3/8 inch to 1/2 inch.
- Texture: This layer is smoothed with trowels to even out the surface, ensuring it’s level and plumb.
3. The Finish Coat
The final layer is the finish coat, which provides the exterior appearance of the wall and often includes a fine texture for aesthetic purposes.
- Composition: Typically a finer mix of cement, lime, and sand.
- Application: Applied in a thin layer of about 1/8 inch.
- Texture: Finished to the desired smoothness or pattern, sometimes using special tools or techniques.
Advantages of the 3 Coat Method
- Durability: The multiple layers create a stronger and more resilient wall surface.
- Improved Bond: Each layer enhances the bonding of the plaster to the masonry.
- Flexibility: Allows for corrections in each layer, leading to a more perfect finish.
- Moisture Resistance: Helps in protecting the wall from environmental elements.
Summary
The 3 coat method of masonry wall plastering is a robust system involving the scratch, brown, and finish coats to create a high-quality wall surface. Each layer plays an essential role in the overall functionality and appearance of the wall. For more detailed technical specifications, you can refer to this Family Handyman guide.
Examining the 3 Coat Stucco Process
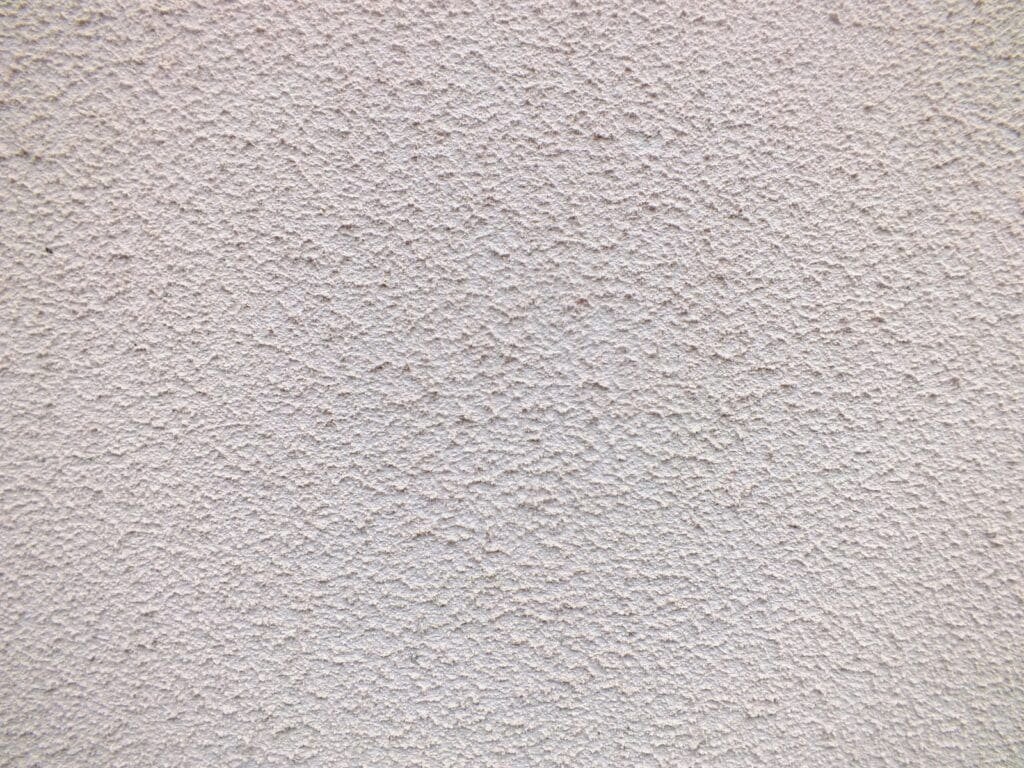
The Detailed Process
Each of the three layers in the 3 coat stucco process requires careful application and timing. The critically coordinated sequence ensures optimum result.
Setting up for Stucco
Before beginning the 3 coat stucco process, the wall surface helps to set up a wire mesh, commonly known as lath. The lath serves as a mechanical key for the stucco to stick to, especially if the wall is smooth, painted or nonabsorbent.
- Composition: It’s typically a metal wire, plastic or paper-backed lath.
- Application: Affixed to the wall with nails or screws.
Weather Factors
With each layer application, weather plays an important role. Too hot, cold, or wet conditions can affect the drying time and the quality of the bond between layers.
- Monitor the temperature: Ideally, the weather should be mild, with temperatures between 40 and 80 degrees Fahrenheit.
- Consider humidity and wind: High humidity or wind can either slow down or speed up the curing process, affecting the strength of the stucco.
Post-application Care
The 3 coat stucco process does not finish with the application of the third layer. Proper care post-application ensures the stucco is cured correctly.
Curing the Stucco
Proper curing of stucco involves maintaining a certain level of moisture and temperature. This reduces shrinkage crack development and enhances the color uniformity in the case of colored stucco.
- Method: It can be accomplished by misting the surface of the hardened stucco with water for a few days. Some professionals use curing agents.
- Duration: The time can vary, but it typically takes about two days for the scratch coat and a day for the brown coat. The finish coat cures in just a matter of a few hours.
Need for a Professional Touch
The 3 coat stucco method might sound like a job for a do-it-yourself enthusiast, but it demands a professional touch for a smooth finish. The application process is labor-intensive and time-consuming.
- Ensure uniformity: Each layer needs to be evenly spread, which might be challenging for novices.
- Avoid cracks: Professionals know how to prevent cracks that can occur if the layers do not correctly bond.
- Quality finish: Skilled craftsmen can achieve a flawless finish, which contributes significantly to the aesthetics of the structure.
For more information on hiring a professional stucco contractor, you may refer to this guide on the This Old House website.
Are there similarities between the 3 coat process of stucco and masonry wall plastering?
Commonalities in Preparation
Before exploring the nuances of each process, it’s crucial to highlight the prep work that both stucco and masonry wall plastering necessitate. Preparation is the backbone of these methods, ensuring the final result is both durable and aesthetically pleasing.
Surface Preparation
Both stucco and masonry wall plastering require meticulous surface preparation to ensure better adhesion of the plaster or stucco.
- Cleaning: Any dirt, oil, or loose particles must be removed from the wall surface.
- Moistening: Dampen the wall to prevent it from absorbing too much moisture from the plaster or stucco mix.
- Base Materials: In plastering, the surface might be pre-treated with a bonding agent, while stucco often uses a metal lath for adherence.
Detailed Layering Process
Both the 3 coat method of stucco and masonry wall plastering involve applying three distinct layers, each serving unique purposes to achieve a robust, smooth finish.
1. The Base Layer
Starting with the initial application, both processes incorporate a base layer that sets the groundwork for subsequent coats.
- Scratch Coat (Plastering): Roughly 3/8 inch thick, providing a key for the next layer with its scored texture.
- Scratch Coat (Stucco): Applied over the lath, usually a similar thickness, and scored similarly to enhance bonding.
2. The Levelling Layer
The second coat, known as the brown coat in both methods, is important for leveling the surface and fortifying the bond.
- Brown Coat (Plastering): About 3/8 to 1/2 inch thick, smoothed evenly to ensure the surface is level and plumb.
- Brown Coat (Stucco): Also around 3/8 to 1/2 inch thick, its primary purpose is to even out the wall, much like in plastering.
3. The Finish Layer
The final layer in both methods is key to achieving the desired aesthetic and protective finish.
- Finish Coat (Plastering): A thinner layer, about 1/8 inch, finely mixed to provide a smooth exterior with potential texture for visual appeal.
- Finish Coat (Stucco): Also about 1/8 inch thick, often finished with a specific texture or pattern for aesthetic purposes.
Factors Influencing Both Methods
There are several factors beyond the raw materials and process that contribute to the success of both the 3 coat stucco and masonry wall plastering methods.
Environmental Impact
Weather conditions can significantly affect curing times and overall finish quality for both stucco and plastered walls.
- Temperature: Both methods benefit from moderate temperatures ranging from 40 to 80 degrees Fahrenheit.
- Humidity and Wind: High humidity can retain moisture, while strong winds can dry the layers too quickly, affecting adhesion and durability.
Post-application Care
Proper post-application care ensures that both stucco and plastered walls reach their maximum strength and durability.
- Curing: Maintaining enough moisture is critical to prevent cracks and ensure a strong bond. Techniques include misting and using curing agents.
- Time Frame: Each layer needs appropriate curing time – two days for the scratch coat, a day for the brown coat, and a few hours for the finish coat.
Professional Installation
Although some DIY enthusiasts might attempt the 3 coat process of stucco or masonry wall plastering, the complexity and detailed attention required often justify hiring professionals.
- Uniform Application: Professionals ensure even layer application, critical for the structural integrity and aesthetic quality.
- Crack Prevention: Skilled workers understand how to apply each coat to prevent common issues like cracks due to improper bonding.
- Flawless Finish: The expertise of a professional ensures a polished final appearance, adding to the value of the structure.
For additional insights on professional stucco application, you may find this resource from This Old House helpful.
Final Considerations for Masonry Finish Coat Techniques
Understanding Various Finish Techniques
The finish coat in masonry wall plastering isn’t a one-size-fits-all approach; there are several techniques to consider depending on the desired aesthetic and functional outcome.
Common Finish Techniques
Several distinct finish styles can be achieved with the final coat, each offering unique visual and textural elements.
- Smooth Finish: Achieved by troweling the plaster to a smooth, polished surface. This type is ideal for modern aesthetics.
- Textured Finish: Various tools such as combs, brushes, or specialized trowels can create patterns like swirls, waves, or stipples.
- Dash Finish: Created using a brush to fling plaster onto the surface, resulting in a rough, bumpy texture.
- Sand Finish: Involves mixing sand into the finish coat plaster, yielding a gritty surface that’s both visually appealing and highly durable.
Material Selection for Finish Coat
The materials chosen for the finish coat can significantly impact the appearance and longevity of the plaster.
Material Considerations
The composition and quality of materials used in the finish coat are essential for achieving the desired results.
- Cement: Typically, Portland cement is used for its durability and strength.
- Lime: Added for workability and to help prevent cracking by allowing the plaster to breathe.
- Sand: The grain size and texture of sand can change the finish’s appearance and texture.
- Admixtures: Additives like retarders, accelerators, or pigments can modify the plaster’s setting time, workability, or color.
Weather Factors and Timing
The timing of applying the finish coat is influenced by environmental conditions, which can affect curing and bonding.
Optimal Conditions
Weather conditions play a critical role in influencing the timing and quality of the finish coat application.
- Temperature: Ideal range is between 50°F and 80°F for best results.
- Moisture Control: Humidity levels should be moderate; too much moisture can weaken the plaster, while too little can cause rapid drying and cracking.
- Wind: High winds can lead to uneven drying, which might cause cracking or poor bonding.
Post-Application Care for Longevity
Proper maintenance after applying the finish coat ensures the longevity and durability of the plaster.
Curing Practices
Correct curing techniques are essential to prevent defects and ensure the finish coat’s robustness.
- Misting: Regular misting with water can help maintain moisture levels, preventing rapid drying and cracking.
- Protection from Elements: Using tarps or protective sheeting to shield the curing plaster from rain, wind, and excessive sun exposure.
- Inspection: Regularly inspecting the curing plaster for early signs of defects such as cracks or uneven textures allows for timely adjustments.
For additional information on mason wall finishes, refer to the detailed guide available on Family Handyman.
Need for Professional Skill
Given the intricacies involved in applying the finish coat, professional expertise often guarantees a higher quality outcome.
Benefits of Hiring Professionals
A skilled professional can address the challenges and nuances of finish coat application, ensuring durability and aesthetic appeal.
- Precision: Achieving the desired texture and smoothness requires experienced hands.
- Consistent Quality: Professionals follow best practices to ensure uniform application and finish.
- Problem Solving: Experts can quickly address unexpected issues such as rapid drying, cracks, or uneven bonding.
For more insights on hiring skilled professionals for masonry work, refer to the comprehensive guide on This Old House.
In Conclusion
The 3 coat method for both stucco and masonry wall plastering is an intricate process that requires precise application and timing for optimal results.
Both methods involve a three-step layering process, including the scratch coat, brown coat, and finish coat, each playing an essential role in the functionality and aesthetics of the wall. Weather conditions and post-application care are also significant factors impacting the finish.
While passionate DIY enthusiasts might be tempted to try their hand at this, the skill and experience of a professional can ensure an immaculate finish and longevity.
Frequently Asked Questions – FAQs
What are the three layers in both plastering and stucco methods?
They both involve a three-layer process: the scratch coat, the brown coat, and the finish coat. The scratch coat serves as the base, the brown coat for leveling and strength, and the finish coat adds the aesthetic touch to the surface.
Why is professional help recommended?
Both procedures are labor-intensive, time-consuming, and demand precise application for high-quality results. A professional can achieve an even spread of layers, prevent cracks, and ensure an aesthetically pleasing finish.
How does weather impact the process?
All steps of the 3 coat process are influenced by weather conditions. Ideal weather conditions are mild with temperatures between 40 and 80 degrees Fahrenheit. High humidity or wind can affect the curing process and the bond’s strength.
Why is post-application care important?
Post-application care ensures the plastering cures correctly. Curing involves maintaining a certain level of moisture and temperature over a certain period, which can reduce shrinkage crack development and provide a uniform color in case of colored plastering.