An Introduction to High Strength Masonry
Ever gazed in awe at soaring skyscrapers, marveling at the invisible force holding it all together? That, my friends, is the power of high strength masonry.
But what exactly does that entail, you ask?
As your unofficial masonry guide, allow me to walk you through the labyrinth of constructing taller structures, withstanding significant loads and forces, and the elements that make up this high strength masonry world.
In this article, we’ll discuss what high strength masonry is, its key components, the benefits it offers, and the different types of masonry and concrete cement. We’ll then explore what separates normal concrete from high-strength concrete, and finally, we’ll examine the world of very high strength cement and where it comes into play.
So let’s kick off this architectural adventure, shall we?
Table of Contents
What Is High Strength Masonry?
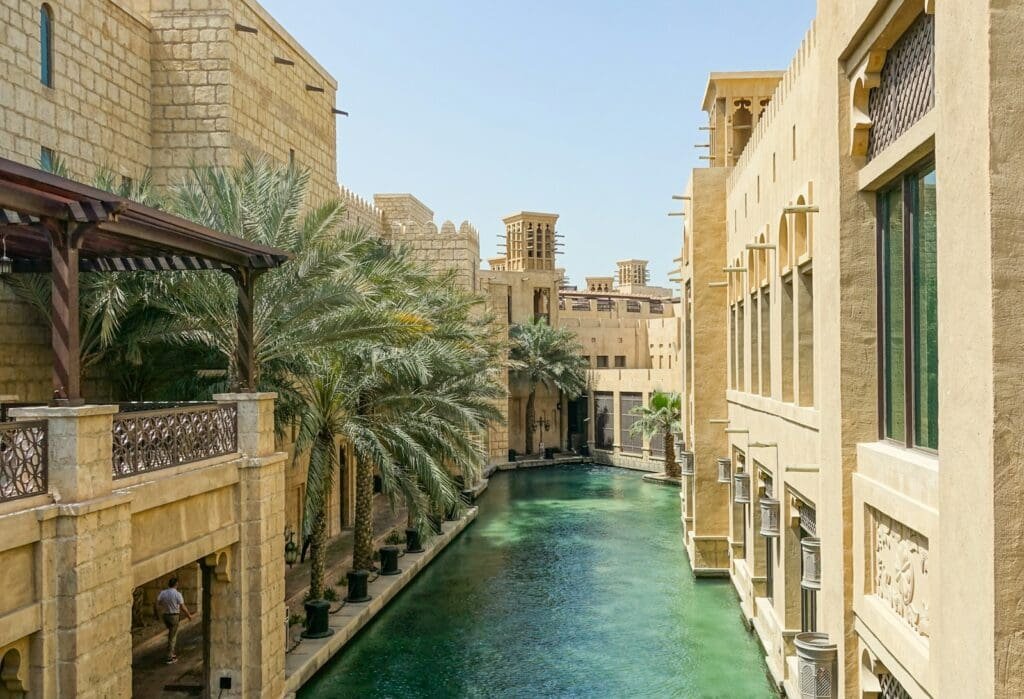
Introduction to High Strength Masonry
High strength masonry is a masonry system that utilizes units and mortar of higher compressive strength than those used in standard masonry construction. This type of construction is designed to provide enhanced structural integrity and support for taller structures or buildings subjected to more significant loads or forces.
Key Components of High Strength Masonry
1. Masonry Units
Masonry units are the building blocks for constructing walls and other structures. In high strength masonry, these units generally have an increased compressive strength.
- Concrete Masonry Units (CMUs): Blocks made from concrete with higher compressive strength.
- Clay Bricks: Fired bricks that can withstand higher pressures.
2. Mortar
Mortar is the binding material used to hold the masonry units together. For high strength masonry:
- Type M Mortar: With a compressive strength of 2,500 psi, Type M is commonly used in high strength applications.
3. Reinforcement
Steel reinforcement is often added within the masonry units to provide additional tensile strength.
- Reinforcing Bars (Rebars): Placed in the hollow cores of concrete masonry units or within the mortar joints.
The Benefits of High Strength Masonry
- Durability: Greater resistance to environmental factors such as wind and seismic activity.
- Taller Structures: Enables the construction of taller buildings with fewer structural limitations.
- Increased Load Capacity: Supports larger loads, making it ideal for commercial and industrial buildings.
Standard Specifications
To ensure quality and consistency, high strength masonry follows specific standards. According to the ASTM standards:
Masonry Unit | Compressive Strength |
---|---|
Concrete Masonry Unit (CMU) | Minimum 1,900 psi (13.1 MPa) |
Clay Brick | Minimum 3,000 psi (20.7 MPa) |
What is the Strongest Masonry Cement?
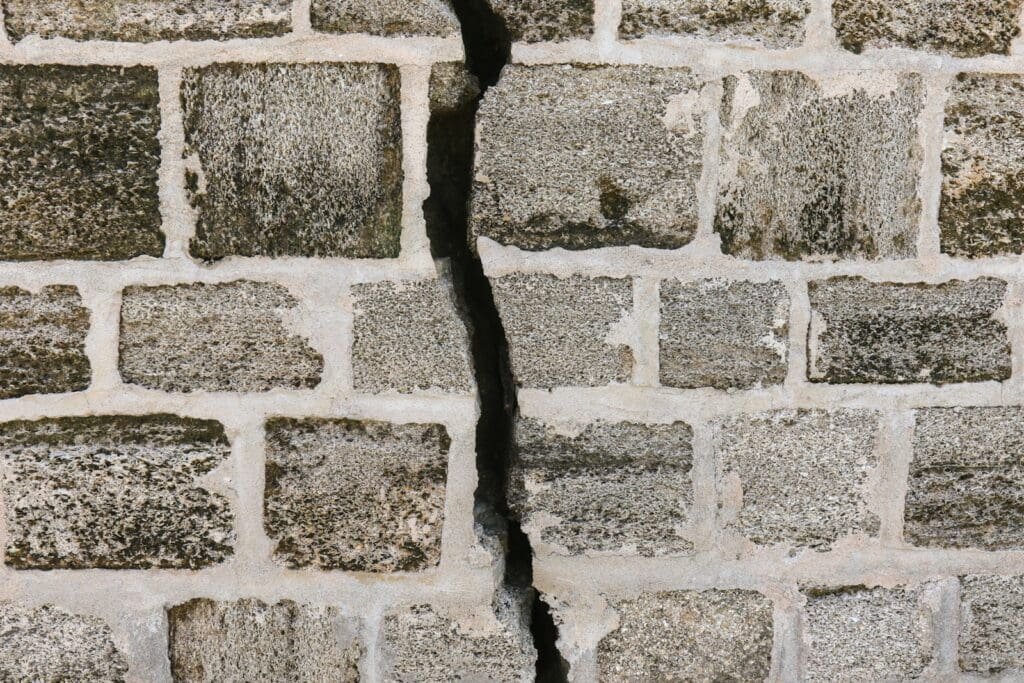
Definition of Masonry Cement
Masonry cement is a specialized blended cement used to make mortar for masonry applications. It consists of a mix of Portland or blended hydraulic cement and plasticizing materials such as limestone and other additives to enhance the mortar’s workability and durability.
Types of Masonry Cement
The strength of masonry cement is classified into different types, each suitable for specific applications based on performance requirements.
- Type N: General-purpose mortar with a compressive strength of 750 psi. It’s commonly used for both interior and exterior, above-grade applications.
- Type S: Medium-strength mortar with a compressive strength of 1,800 psi, ideal for below-grade applications like retaining walls and foundation walls.
- Type M: High-strength mortar boasting a compressive strength of 2,500 psi, used for severe load-bearing and reinforcement situations, such as foundations, retaining walls, and driveways.
Strongest Masonry Cement
When it comes to the strongest masonry cement, Type M cement is the leader:
Type M Masonry Cement: This is the best fit for high compression-strength applications. With a compressive strength of 2,500 psi, it’s primarily employed in severe environments subjected to frost and high-pressure conditions. It’s also suitable for constructing reinforced masonry columns, foundation walls, retaining walls, and concrete steps that bear substantial loads.
Applications of High Strength Masonry Cement
- Foundation and Basement Walls: With its high compressive strength, Type M masonry cement ensures durability and stability in foundational structures.
- Load-Bearing Walls: Ideal for walls that support roof and floor loads, essential for both residential and commercial buildings.
- Outdoor Pavement: The increased strength is beneficial for driveways and other high-traffic areas that experience heavy wear.
- High-Rise Buildings: It offers the structural integrity required for vertical expansions and taller structures.
Comparative Strength Chart
Type of Mortar Cement | Compressive Strength (psi) | Typical Use |
---|---|---|
Type N | 750 psi | Above-grade exterior and interior walls |
Type S | 1,800 psi | Below-grade exterior and interior walls |
Type M | 2,500 psi | Load-bearing walls and severe condition structures |
Role of Environmental Factors
Environmental factors greatly influence the selection of masonry cement. For regions with severe weather conditions such as heavy rainfall, extreme wind, or seismic activity, Type M cement is often chosen due to its superior durability and robustness. It resists erosion and maintains structural integrity over extended periods.
For further reading on construction standards, consult the Portland Cement Association website, which offers detailed guidelines and recommendations for various masonry applications.
What is the Difference Between High-Strength Concrete and Normal Concrete?
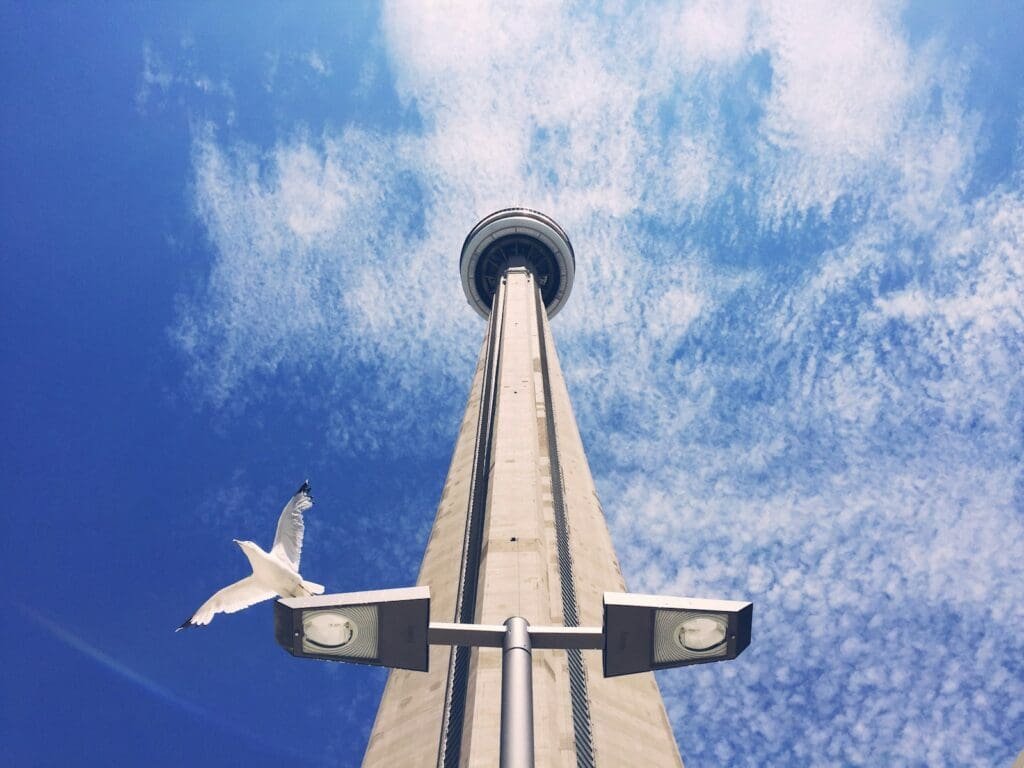
Introduction to Concrete Types
Concrete is a composite material widely used in construction, consisting of aggregate, cement, and water. It comes in various types, each designed for specific applications and performance requirements. The main types discussed here are high-strength concrete and normal concrete.
High-Strength Concrete
High-strength concrete is engineered to achieve a higher compressive strength typically over 6,000 psi (41 MPa). It’s designed to handle greater loads and is used in applications where structural integrity is essential.
- Compressive Strength: Usually ranges from 6,000 to over 20,000 psi (41 to 138 MPa).
- Applications: Commonly used in high-rise buildings, bridges, and heavy-duty industrial floors where significant strength and durability are necessary.
- Composition: Contains a higher ratio of cement to water, and often includes silica fume, fly ash, or slag to improve performance.
- Durability: Enhanced resistance to environmental factors like freeze-thaw cycles, abrasion, and chemical attacks.
Normal Concrete
Normal concrete, also known as regular or conventional concrete, is the most commonly used type and is suitable for general applications.
- Compressive Strength: Generally ranges from 2,500 to 5,000 psi (17 to 34 MPa).
- Applications: Frequently used in residential buildings, pavements, sidewalks, and other structures that do not require extraordinary strength.
- Composition: A balanced mix of cement, aggregates, and water, with optional additives like plasticizers or air-entraining agents to adjust properties.
- Workability: Easier to handle and place compared to high-strength concrete.
Comparative Analysis
To help visualize the differences, below is a comparison table:
Property | High-Strength Concrete | Normal Concrete |
---|---|---|
Compressive Strength | 6,000 – 20,000 psi (41 – 138 MPa) | 2,500 – 5,000 psi (17 – 34 MPa) |
Typical Applications | High-rise buildings, Bridges, Industrial floors | Residential buildings, Sidewalks, Pavements |
Main Components | Higher cement content, silica fume, fly ash | Traditional cement, aggregates, water |
Durability | Very high | Moderate |
Workability | Lower | Higher |
Use of Admixtures
Admixtures play a significant role in achieving the desired properties in both high-strength and normal concrete.
- High-Strength Concrete: Common admixtures include silica fume, which enhances strength and durability, and superplasticizers to improve workability.
- Normal Concrete: Admixtures like air-entraining agents improve resistance to freeze-thaw cycles, and plasticizers increase workability without affecting strength.
Cost Implications
While high-strength concrete offers superior performance, it comes at a higher cost due to more expensive materials and the need for precise mixing and placing techniques. Normal concrete, being less expensive, is often chosen for projects where cost-efficiency is essential.
For more detailed information on concrete types and their applications, the Portland Cement Association provides extensive resources and guidelines.
What Is Very High Strength Cement Used For?
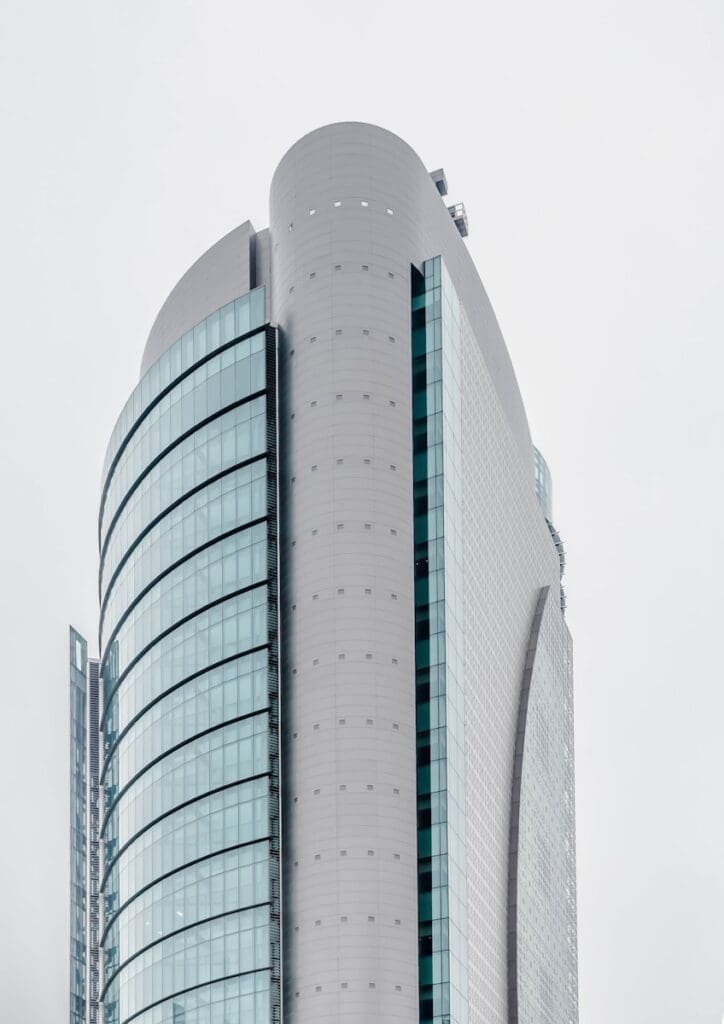
Introduction to Very High Strength Cement
Very high strength cement (VHSC) is a specialized type of cement designed to achieve extremely high compressive strengths, often exceeding 10,000 psi. This type of cement is engineered for applications that require extra durability and the capacity to handle extreme loads and stresses.
Applications of Very High Strength Cement
Very high strength cement is utilized in a variety of critical and demanding environments where conventional cement might not provide the necessary performance. Here are some key applications:
- Skyscrapers and High-Rise Buildings: VHSC is vital for the structural cores and foundational elements of super-tall buildings, which need to support immense vertical loads.
- Bridges and Overpasses: The compressive strength and durability of VHSC make it ideal for constructing long-lasting bridge structures that can bear heavy traffic loads and resist environmental degradation.
- Industrial Floors and Heavy Machinery Foundations: Facilities requiring robust floor slabs to withstand the weight and vibration of heavy machinery benefit significantly from VHSC.
- Nuclear Power Plants: The extreme loads and safety requirements of nuclear facilities necessitate the use of very high strength cement to ensure structural integrity and longevity.
- Marine Structures: Ports, offshore platforms, and other marine structures benefit from VHSC’s ability to endure harsh marine environments, including constant exposure to saltwater.
- Tunnels and Underground Structures: VHSC is used in tunnel linings and underground chambers that must support immense earth pressures and remain stable over time.
Key Properties of Very High Strength Cement
The exceptional performance of very high strength cement comes from its unique properties, which include:
- High Compressive Strength: Typically ranges from 10,000 to 20,000 psi, significantly higher than standard concrete.
- Low Permeability: Offers improved resistance to water and chemical ingress, which enhances durability.
- Superior Durability: Can withstand extreme environmental conditions, including freeze-thaw cycles and corrosive settings.
- Enhanced Bonding: Improved adhesive properties with steel reinforcements, essential for prestressed concrete structures.
Scientific Innovations and Development
The development of very high strength cement involves advanced materials science and engineering. Researchers continuously explore ways to optimize the composition and properties of VHSC using innovative techniques and additives:
- Supplementary Cementitious Materials (SCMs): Components like silica fume, fly ash, and ground granulated blast-furnace slag (GGBFS) are used to enhance strength and durability.
- Nanotechnology: Nano-silica and other nano-materials are integrated to improve cement particle packing and reduce voids, hence increasing strength.
- High-Performance Admixtures: Superplasticizers, accelerators, and other chemical admixtures are used to achieve desired rheological properties and accelerate strength gain.
Comparative Strength Performance
Below is a comparison between standard concrete, high-strength concrete, and very high strength cement:
Type | Compressive Strength | Typical Applications |
---|---|---|
Standard Concrete | 2,500 – 5,000 psi | Residential buildings, pavements |
High-Strength Concrete | 6,000 – 10,000 psi | High-rise buildings, bridges |
Very High Strength Cement | 10,000 – 20,000 psi | Skyscrapers, industrial floors, marine structures |
For further reading on advanced construction materials and their applications, visit the American Society of Civil Engineers (ASCE) website for in-depth resources and technical papers.
Summing It Up
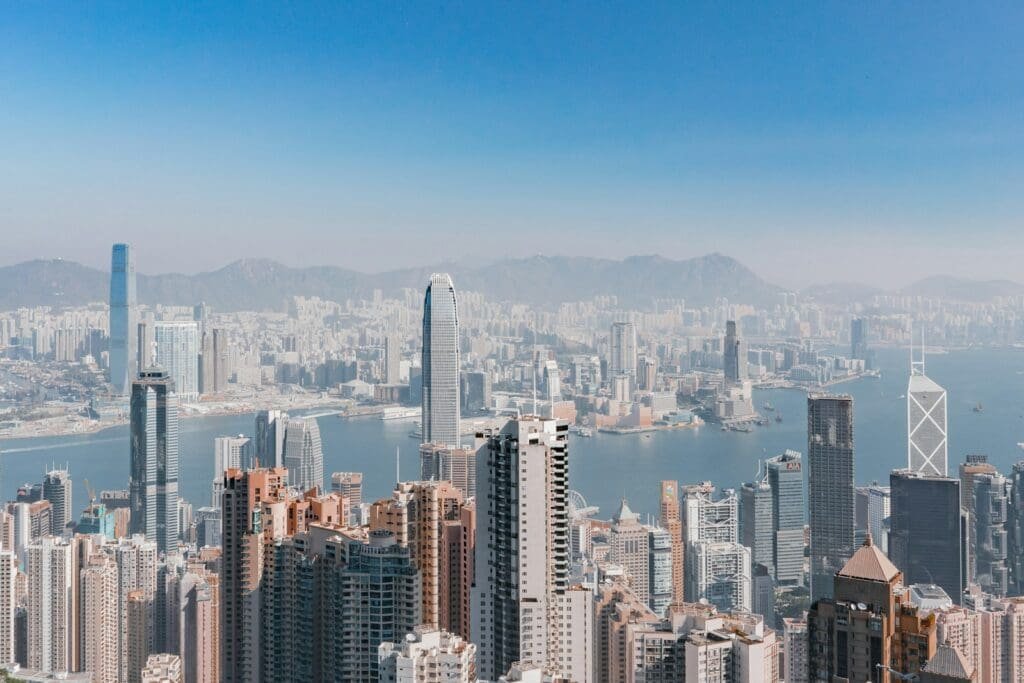
High strength masonry, masonry cement, different types of concrete including high-strength and regular, and very high-strength cement, each possess their distinct features, types, uses, and advantages.
High strength masonry helps create durable structures resistant to environmental factors, making it ideal for taller structures and buildings subject to greater loads. Masonry cement, classified into different types (Type N, Type S, and Type M), varies in strength for specific uses ranging from general-purpose to high-pressure conditions.
High-strength concrete and normal concrete differ in compressive strength, typical applications, components, durability, and workability.
Some applications demand even stronger cement; this is where very high-strength cement comes into play. Made to withstand pressures over 10,000 psi, it’s designed to help sustain structures like skyscrapers, high-rise buildings, and nuclear power plants.
Frequently Asked Questions – FAQs
What is High Strength Masonry?
High strength masonry uses higher compressive strength units and mortar than standard masonry, providing greater structural integrity. It’s used for taller structures or buildings subjected to high forces.
How Does Masonry Cement Vary in Strength?
Masonry cement is divided into Type N, S, and M, each boasting different compressive strengths for specific use cases. Type M cement, with the highest strength, is suited for load-bearing and high-pressure scenarios.
What’s the Difference Between High-Strength Concrete and Normal Concrete?
High-strength concrete offers a higher compressive strength, is used in demanding applications, and provides enhanced durability yet lower workability. In contrast, Normal concrete presents moderate strength and durability but better workability, ideal for general uses.
What is Very High Strength Cement Used For?
Very high strength cement, offering compressive strengths over 10,000 psi, is used in environments requiring extra durability and high load handling. Applications range from skyscrapers and nuclear power plants to marine structures and bridges.