Rich Mixture Concrete vs Regular Concrete
In the construction world, materials make a massive difference in a project’s outcome.
A particular material of interest is rich mixture concrete.
This type of concrete is unique due to its greater cement to sand ratio. This means it contains more cement and less sand than regular concrete, resulting in a denser, stronger, and more durable material.
Ideal for applications where more strength is needed.
Regular concrete, on the other hand, is the ‘bread and butter’ of many construction projects. It consists of standard ingredients: cement, sand, gravel, and water. This blend is used for a wide range of construction projects.
Let’s kick off our Ted Talk on Rich Mix.
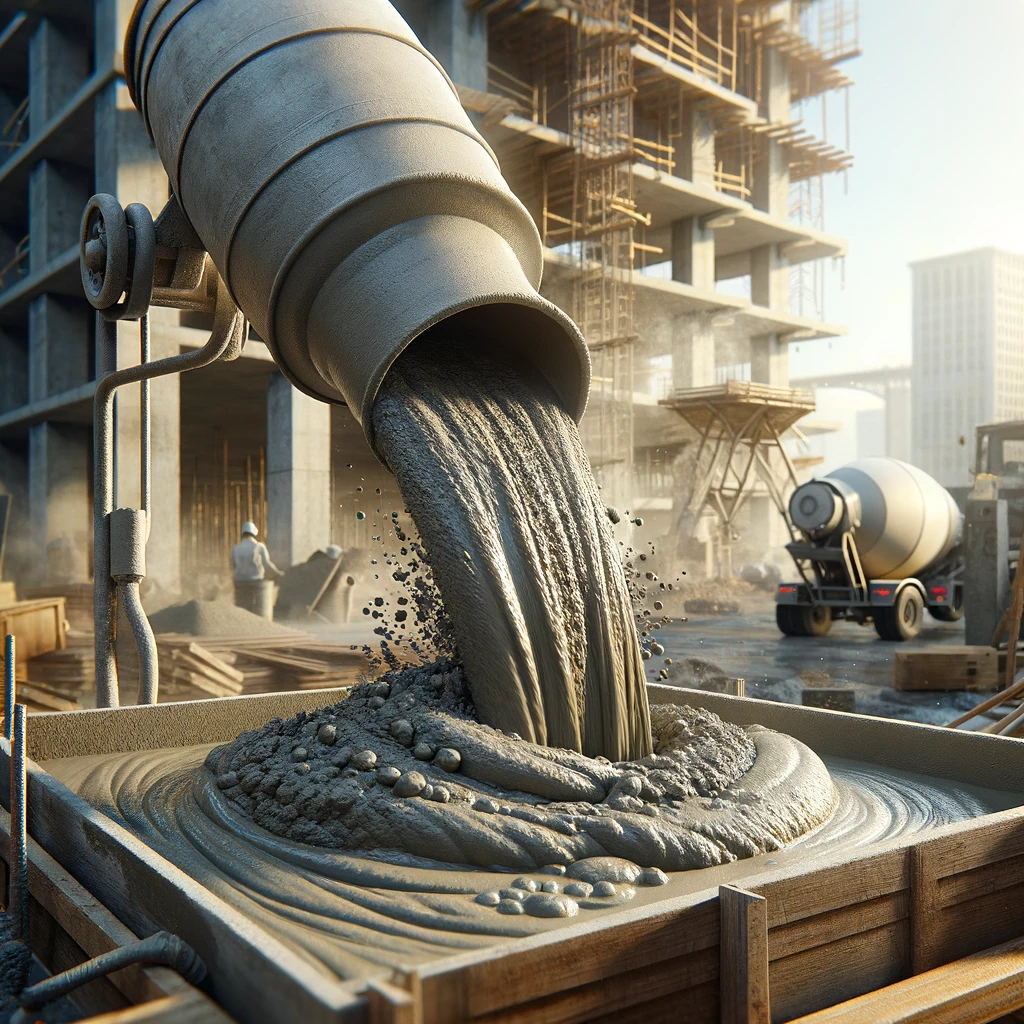
Table of Contents
Rich Mixture Concrete: Applications in Construction
Rich Mixture Concrete, often simply referred to as rich concrete, is a durable and versatile construction material.
Characterized by its high cement content, it’s widely used in many commercial construction scenarios, particularly when strength and durability are paramount.
Key Features of Rich Mixture Concrete
This type of concrete is defined by its high cement-to-aggregate ratio, typically exceeding the standard 1:2:4 ratio of cement, sand, and aggregate.
It often includes additional admixtures for enhancing its overall performance.
Strength and Durability
Rich Mixture Concrete is best known for its strength, boasting a higher compressive strength compared to standard concrete. Furthermore, its density renders it remarkably durable, thus lending itself to long-lasting construction projects.
Applications of Rich Mixture Concrete in Commercial Construction
1. Structural Applications
In high-rise buildings, bridges, and other large-scale commercial structures, Rich Mixture Concrete is the material of choice for the core structural elements. This includes foundations, support pillars, and load-bearing walls. This is primarily due to its high compressive strength and durability.
2. Concrete Pavements
Commercial entities such as malls, warehouses, and industrial parks which demand robust concrete pavements can greatly benefit from rich mixtures. Due to their high wear resistance and ability to withstand heavy loads, they offer an ideal solution for such settings.
3. Specialised Engineering Projects
In addition to mainstream commercial applications, Rich Mixture Concrete finds utility in specialised construction projects. This includes underwater construction, tunnel lining, and nuclear power plants where high durability is required. Special admixtures may be added to further enhance their performance in these unique construction environments.
Rich Mixture Concrete: A Recap
Features | Application |
---|---|
High cement-to-aggregate ratio | Enhances strength and durability |
High compressive strength | Ideal for large-scale structural applications |
High durability and wear resistance | Suitable for heavy-duty pavements |
Adaptable with admixtures | Works for specialised engineering projects |
In conclusion, Rich Mixture Concrete is a high-performance concrete mixture that offers enhanced strength and durability.
Its applications in commercial construction are varied and extensive, making it a versatile material that can cater to most demanding construction projects. If you are looking for a construction solution that prioritises strength and longevity, Rich Mixture Concrete might just be your answer.
References
- Research Paper: Properties and Applications of High-Performance Concrete
- ACI Manual of Concrete Practice
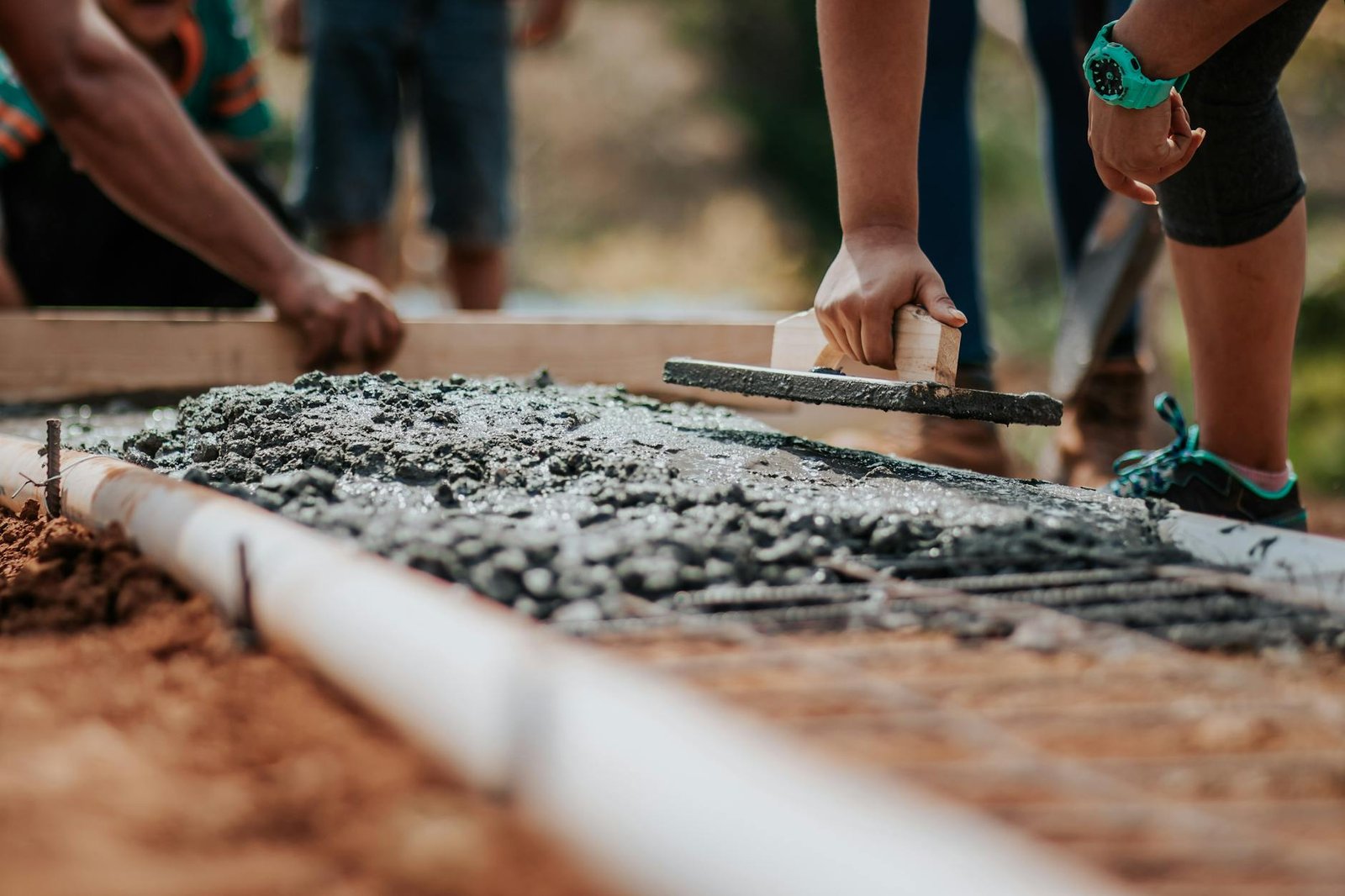
Cost Comparison: Rich Mixture Concrete vs. Regular Concrete
What Makes up Regular Concrete?
Regular Concrete is the basic type of concrete, typically composed of cement, gravel, sand, and water.
It’s the standard building material for numerous construction applications.
Here’s how it compares to its affluent counterpart.
Comparing Costs: Rich Mixture Concrete vs. Regular Concrete
Cost Breakdown
The cost comparison between Rich Mixture Concrete and Regular Concrete hinges on a few vital factors:
- The amount of each ingredient required
- Presence and cost of additives or special ingredients
- Costs associated with handling, mixing, and workability
Initial Material Costs
Rich Mixture Concrete tends to be more costly in initial material costs due to its higher cement content.
Operational Costs and Long-Term Value
While it may require a larger upfront investment, using rich-mixture concrete can result in long term savings. As this material typically requires less maintenance and offers better durability, investing in rich-mixture concrete can provide excellent long-term value, especially for large structures where strength and durability are paramount.
An Overview of Cost Comparison
It’s clear from our exploration that while the initial costs can be higher for Rich Mixture Concrete, the value it offers in terms of long-term strength, lifespan, and lower maintenance requirements can make it a smart investment.
Keep in mind these prices likely vary depending on many factors, including location, vendor pricing, and market fluctuations, so it’s essential to get accurate quotes before making a decision.
When deciding between rich mixture concrete and regular concrete, consider not just the initial costs but the long-term value and performance.
Reach out to your local contractors or construction material providers for a more detailed and accurate cost comparison tailored to your specific project and location.
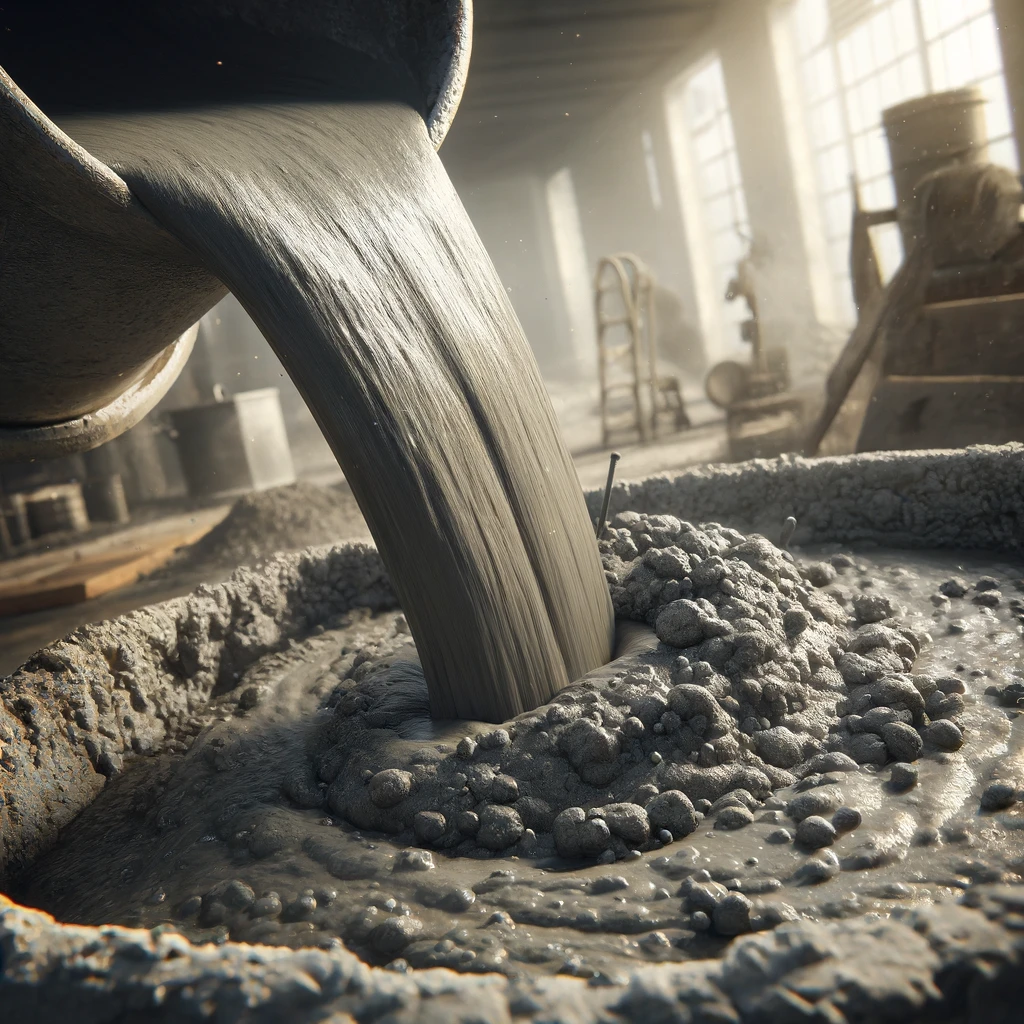
Potential Challenges of Using Rich Mixture Concrete
Potential Issues When Using Rich Mixture Concrete
1. Increased Shrinkage
Rich mixture concrete undergoes more shrinkage than traditional concrete given its higher cement content. This can result in cracking, a major concern for structural stability and aesthetics (source).
2. Cost Implications
The increased cement content in rich mixture concrete makes it more expensive. This can have significant cost implications on larger projects.
3. Workability Issues
This type of concrete can be tough to work with due to its high viscosity, particularly when pouring into complex moulds or intricate designs.
4. Risk of Water Bleeding
Rich concrete mixtures are prone to higher water bleeding, which could potentially weaken the concrete surface and negatively impact its long-term durability.
Quick Summary Table
Challenges | Details |
---|---|
Increased Shrinkage | Due to more cement, there’s a higher likelihood of shrinkage and cracking |
Cost Implications | Rich mixture concrete is pricier due to higher cement content |
Workability Issues | The mixture’s rheology can make it difficult to pour into complex moulds |
Risk of Water Bleeding | The mixture is prone to more water bleeding, which can weaken the surface |
In conclusion, although rich mixture concrete can provide increased durability and strength, it’s essential to consider the potential challenges when deciding whether it’s the right choice for your project.
Wrapping Up Rich Mix vs Regular
In unravelling the cost contrasts between rich mixture concrete and regular concrete, we’ve found several crucial distinctions.
Although rich mixture concrete commands a higher initial investment owing to its enhanced cement content, from our perspective, its quality and longevity bring exceptional long-term value.
Less maintenance and better durability can lead to significant financial offsets in the long run, especially for large-scale projects where stability and durability are vital.
In our experience, cost comparisons are impacted by a multitude of influences such as location, vendor pricing, and market oscillations. Procuring specific quotes is key in making educated choices about the suitable concrete type for your project. Thus, the emphasis should not only be on the upfront costs but also on long-term value and performance.
To conclude, we recommend reaching out to local contractors or construction material providers. They can offer a detailed and precise cost comparison in line with your unique project requirements and location. This will aid in the decision-making process, placing an importance on both financial and structural feasibility.